Клей фенолформальдегидный: Фенолформальдегидные клеи — Энциклопедия по машиностроению XXL
Фенолформальдегидные клеи — Энциклопедия по машиностроению XXL
Фенолформальдегидный клей ВИАМ Б-3 представляет собой продукт поликонденсации, получаемый из смолы ВИАМ-Б под воздействием керосинового контакта. Клей растворяется на ацетоне или этиловом спирте. [c.59]На рис. 12 приводятся опытные кривые ползучести при сжатии цилиндрических образцов отвердевшего фенолформальдегидного клея КБ-3, полученные в лабораторных условиях. Выравнивание кривой (10) по опытным данным дало и здесь очень хорошее соответствие. [c.46]
Коэффициент внутреннего трения истинного течения образцов фенолформальдегидного клея КБ-3 [c.46]
При длительном воздействии нагрузки сверхтвердые пропитанные древесноволокнистые плиты при растяжении имеют ясно выраженную затухающую ползучесть. Трехмерная сетчатая структура связующего (фенолформальдегидный клей) при растяжении может вытягиваться только до определенных пределов, после чего начинается ее разрушение.

Фенолформальдегидные клеи изготовляются из фенолформальдегидной смолы резольного типа и состоят из нее на 40—60%. Остальную часть составляют свободный фенол, свободный формальдегид и вода (от 50 до 20%). [c.150]
У нас в СССР были разработаны и получили широкое распространение фенолформальдегидные клеи марок Б и КБ—3.. [c.151]
Во многих случаях при соединении листовых элементов особенно большой прочности от клеевых щвов не требуется. В этих случаях на первый план выдвигается требование надежности и стойкости клеевого щва против старения в атмосферных условиях, а также экономические соображения. Этим требованиям отвечают клеи Б и КБ—3, а также слабо модифицированные клеи. Так, для склеивания между собой элементов из алюминиевых сплавов применяется фенолформальдегидный клей ФЭ—10, получаемый добавкой к смоле десяти процентов эпоксидной смолы.
Фенолформальдегидный клей марки Б горячего отверждения [c.157]
Фенолформальдегидный клей КБ-3 холодного отверждения
Фенолформальдегидный клей горячего отверждения марки ФЭ-10 Полиэфирный клей холодного отверждения марки ПН-1 Каучуковый клей холодного или теплого отверждения [c.157]
Склеивание древесностружечных плит с асбестоцементом может быть осуществлено на эпоксидном клее холодного отверждения или на фенолформальдегидном клее горячего отверждения 7 -20 [c.225]
К синтетическим относятся клеи Бф-2, Бф-4, Бф-6 — растворы фенолформальдегидных смол в спирте пли ацетоне эпоксидный клей Д-9 — синтетическая эпоксидная смола с добавлением отвер-дителя смолы — и ряд других клеев. Подробные сведения о марках клеев, их характеристики и рекомендации к их применению приводятся в справочной литературе [1, 34].
Известны клеи на основе фенолформальдегидных соединений разной модификации, применяемые для склеивания металлов друг с другом, а та кже пластмасс, керамики,
[c. 162]
Фенолформальдегидные смолы, модифицированные синтетическими каучуками, термопластами и некоторыми другими соединениями, составляют основу клеев с теплостойкостью до 200—350 С. [c.268]
Синтетические клеи служат для склеивания металлов, пластмасс (фенолформальдегидных пластиков, органического стекла и т. д.), древесины, фарфора и керамики в любом сочетании между собой.
Термореактивные пластмассы склеивают смоляными клеями типа ВИАМ Б-3 или КМ на основе соответственно фенолформальдегидной и мочевиноформальдегидной смол. После нанесения клея на склеиваемые поверхности и их сжатия смола должна перейти в термостабильное состояние. При комнатной температуре эта реакция длится несколько месяцев. Поэтому в клей добавляют специальные отвердители и выдержку производят при повышенных температурах. [c.673]
СКЛЕИВАНИЕ ДРЕВЕСНЫХ И БУМАЖНЫХ МАТЕРИАЛОВ. Различные породы дерева и древесные пластики склеивают синтетич.
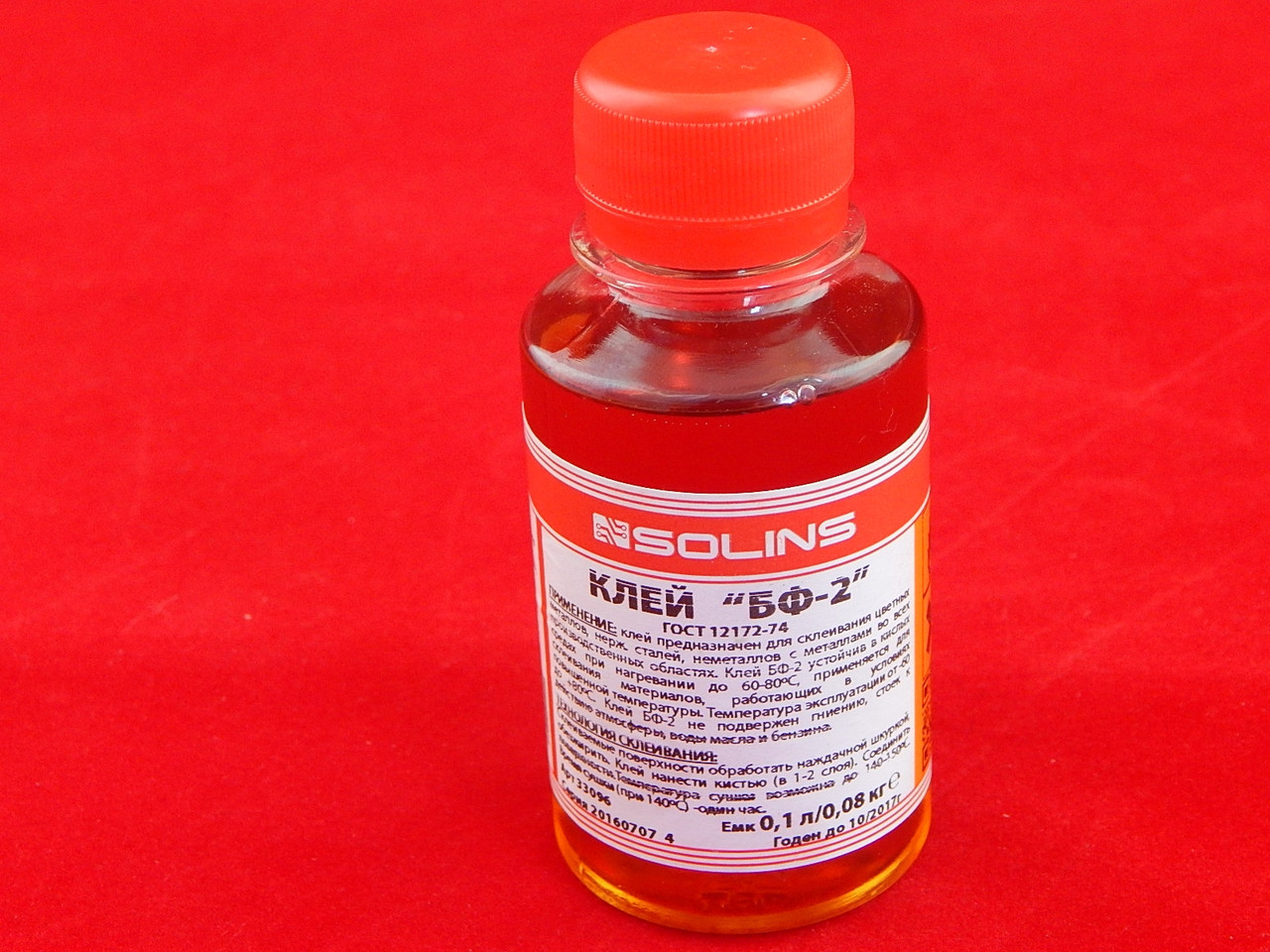
При использовании синтетич., в частности фенолформальдегидных, клеев темп-ра склеивания должна быть 50—60° повышать ее следует постепекно. [c.171]
В соответствии с ГОСТ 11519—65 разделяется по виду применяемого клея —на склеенную фенолформальдегидными клеями (марка ФОФ) и склеенную карбамидными клеями (марка ФОК) по виду материала рубашек — на одностороннюю, у которой одна рубашка из строганого, а другая из луш еного шпона, и на двустороннюю, у которой обе рубашки из строганого шпона по текстуре строганого шпона — на радиальную, полурадиальную и тангенциальную по виду обработки поверхностей рубашек — на нешлифованную и шлифованную с одной или двух сторон.
Для одновременного выполнения нескольких операций применяют универсальные деревообделочные станки. Для склеивания деревянных деталей применяют клеи казеиновые и из синтетических смол. Синтетические клеи более стойки к действию воды, микроорганизмов, старению и обладают повышенной прочностью. Качество клеевого соединения зависит от величины давления между склеиваемыми деталями, вязкости клея и температуры выдержки под давлением. Температура помещения, где выполняют склеивание деталей фенолформальдегидным клеем КБ-3 или СП-2, должна быть не ниже 16°С. Восстановленные деревянные детали должны быть без трещин, задиров и ступенчатости, торцы — чистыми, без отщепов и сколов.
Фенолформальдегидные клеи водостойки и не растворимы в кислоте, масле, бензине. Прочность клеевого шва на сдвиг достигает 100—130 кГ1см . Клеи эти имеют небольшой срок схватывания, относительно недороги и доступны. [c.151]
Для склеивания без нагрева, при холодном отверждении, применяется фенолформальдегидный клей КБ—3, получаемый из той же смолы Б путем добавки к ней контакта Петрова, являющегося отвердителем. Контакт Петрова состоит из керосина и добавляемой к нему в количестве 20% (по весу) кислоты. Для предотвращения разрушающего действия кислоты склеиваемые поверхности из алюминиевых сплавов и асбестоцемента необходимо грунтовать алюминий — клеем БФ—2, асбестоце-мен г — пол иметилметакрилатным грунтом П.
При всех положительных качествах фенолформальдегидных клеев в случае склеивания ими таких жестких материалов, как алюминий и асбестоцемент, обнаруживается большая хрупкость шва. Чтобы уменьшить хрупкость клеевого шва, фенолформаль-дегидную смолу модифицируют добавкой других смол (в основном эпоксидной) или каучуков, получая так называемые совмещенные клеи. Совмещенные клеи обладают высокой теплостойкостью (до 350°), повышенной прочностью — до 350 дают более эластичный шов, хорошо сопротивляющийся неравномерному отрыву. Но при склеивании они требуют продолжи-
Фанера, склеенная из трех и более слоев лущеного шпона, в зависимости от вида применяемого клея изготавливается следующих марок ФСФ — склеенная фенолформальдегидными клеями ФК — склеенная карбамидными клеями ФБА—склеенная альбумино-казен-новыми клеями (по требованию потребителя допускается склеенная казеиновыми клеями).
[c.23]
Особым случаем использования слоистых композиционных материалов, наиболее часто применяющихся в строительной промышленности, являются трехслойные панели. Они обычно состоят из двух относительно тонких облицовок, изготовленных из твердых, плотных и долговечных материалов, соединенных с относительно толстой сердцевиной (заполнителем) из легкого, менее прочного и менее жесткого материала. Облицовки и заполнитель могут, в свою очередь, быть выполненными из композиционных материалов, как например, облицованная стеклопластиками, армированная частицами панель (древесные частицы распределены в связующем из синтетической смолы). Для изготовления облицовок используется множество материалов, в том числе металлы, фанера, картон, асбоцемент, бетон в виде плит небольшой толщины и др. Сердцевина может быть выполнена из пенопласта, пенобетона, пеностекла, сот, деревянных или металлических решеток, фанеры, армированных частицами или волокнами плит и др. Для соединения заполнителя облицовок используются различные клеи.
Клеящая композиция для водостойкой фанеры (вес, ч.). Древесная мука — 1—5 мел молотый — 2—15 смола ФР-12 — 1—40 уротропин или параформ — 0,1—0,5 фенолформальдегидная смола С-1 —100. (Склеивание производят без сушки нанесенного клея.) [c.130]
Клей для крепления поливинилхлоридного пластика к древесной фибре (вес. ч.). Сополимер винилхлорида с ви-нидацетатом — 60—90 эпоксидная диановая смола — 5—30 фенолформальдегидная смола — 10—30 сложноэфирный полиуретановый каучук — 3—10 продукт 102-Т — [c.130]
Клей 3-300 (ТУ 38—5—372—68). Бута-диен-нитрильный каучук, смола бутил-фенолформальдегидная—101, хлорнайрнт. АГс. =29,5 2.5. [ЭА БНЗ=2,5 1]. мес [c.138]
Клеи на основе фенолформальдегидной смолы используются для склеивания металлов, пластмасс, керамики. Для уменьшения хрупкости фенолформальдегидную смолу соединяют с другими полимерами. Клеи ВК-3, ВК-4, ВК-13, ВК32-200 являются продуктом взаимодействия фенолформальдегидной смолы и синтетического каучука, клеи БФ-2 и БФ-4 — фенолформальдегидной смолы и бутвара, клей ВК-32-ЭМ — фенолформальдегидной и эпоксидной смол.
[c.269]
Склеивание древесины синтетич. клеями применяется в произ-ве мебели, фанеры, древесных пластиков, при изготовлении клееных деревянных конструкций для различных отраслей строительной техники, а также в быту. Древесину с другими неме-таллич. материалами склеивают гл. обр. фенолформальдегидными, карбамидными, смешанными мочевиномеламиноформаль-дегидными клеями, а также клеящими композициями из резорциновых и фенол-резорциновых смол. Значительно реже, преимущественно для соединения древесных материалов с металлами, используют полиуретановые и полиэноксидные клеи. Фенолформальдегидные и резорциновые клеи наиболее прочные и водостойкие служат гл. обр. при изготовлении изделий от-ветств. назначения в различных областях нар. х-ва и в произ-ве древесных слоистых пластиков. Осн. область применения карбамидных клеев, наиболее распространенным из к-рых является МФ-17,— мебельная пром-сть и фанерное произ-во. Для склеивания бумаги, картона и др. листовых целлюлозных материалов пригодны гл. обр. клеи растит, и животного проис-
[c.171]
Ф. Л. склеиваются столярным и фенольными клеями холодного отверждения, раствором поливинилхлорида в дихлорэтане. Смола 30 — фенолформальдегидная смола, модифицированная полиамидом, который вводится для повышения упругих св-в продукта применяется для изготовления штампов и мастер-моделей, Гарантийный срок хранения смолы в стеклянной или железной закрытой таре 1 год. Композиция для заливки в формы содержит смолу 30 (100 вес. ч.), формалин технич. (4 вес. ч.), отвердитель (контакт Петрова, 7 вес. ч.) и пластификатор (олеиновую к-ту, 1—3%). Композиция готовится тп1,ательным перемешиванием компонентов. Готовую композицию заливают в гипсовые или деревянные формы, покрытые разделит, составом. Формы подвергаются вакуумированию в течение 2—5 м при глубине вакуума не менее 150 мм рт. ст. для удаления пузырьков воздуха, захваченных при перемешивании и заливке смолы. Залитые формы выдерживают нри комнатной темн-ре до загустевания смолы. В отличие от неолей-корита, литых резитов и литого карболита, теплота экзотермич. реакции отверждения смолы 30 невелика, темп-ра в массе смолы после добавления отвердителя поднимается
[c.396]
Термореактивные полимеры — реактопласты не могут переходить в пластическое состояние при повышенной температуре. С этой точки зрения подобные полимеры можно рассматривать как термостабильные материалы. Образование пространственных структур этих полимеров происходит с последовательным возрастанием их молекулярного веса. В процессе образования термостабильного полимера постепенно уменьшается способность их размягчаться (переходить в пластическое Состояние), растворяться или набухать в ка-ком-нибудь растворителе. Эти полимеры можно формовать в изделия, наносить в виде лака или клея, а затем переводить в термостабильное состояние. К ним относятся прессмассы (фенопласты, карболит, аминопласты), композиционные материалы на основе фенолформальдегидных, эпоксидных, полиэфирных, кремнийорга-нических смол и их компаундов с различного род4 наполнителями (стекловолокно, древесная мука или опилки, маршалит, кварцевый песок и пр.).
[c.25]
В зависимости от водостойкости фанера выпускается следующих марок ФСФ — повышенной водостойкости, склеенная клеями типа фенолформальдегидных ФК и ФБА — средней водостойкости, склеенная клеями карбамидными или альбуминоказеиновыми. В зависимости от вида обработки поверхностей рубашек фанера изготовляется шлифованной или циклеванной с одной или двух сторон и нешлифованной. [c.22]
В соответствии с инструкцией № 74040-152-66 клей марки ИДС состоит (вес. %) идитол — 40,6 канифоль — 6,6 гидролизный спирт — 23,2 асбест марки М-6-40 или М-6-304,9 препарат ЖАФ (закисный железоаммопий-фосфат) — 24,7. Клей предназначается для приклеивания пенополистирола марки ПСБ-С, фенолформальдегидных пластмасс марок ФС-7з, ФФ и ФЛУз, экспанзита, пробковых и асбовермикулитовых плит к металлу, к стеклопластику и склеивания нлит между собой.
[c.60]
В соответствии с инструкцией № 74040-152-66 клей марки ЛКС состоит, вес. % нитроглифталевый клей ЛК-1—76 асбест марки М-6-40 или М-6-30—5 препарат ЖАФ —19. Клей предназначается для приклеивания фенолформальдегидных пластмасс марки ФС-72, ФФ, ФАУз, экспанзита, пробковых и асбовермикулитовых плит к металлу, стеклопластику и склеивания плит между собой. [c.60]
Синтетические клеи состоят из эпоксидных, фенолформальдегидных и других смол, растворителя (ацетона, этилового спирта) и отвердителя. В качестве отвер-дителей применяется 50%-ный раствор гексаметилен-диамина в спирте, нолиамин, малеиновый ангидрид и другие вещества. [c.388]
Термореактивная фенолформальдегидная смола может находиться в трех состояниях в стадии резол, резитол и резит. В стадии резол смола легко плавится и растворяется. При длительном хранении медленно, а при нагревании быстро смола переходит в состояние резит — нерастворимое и неплавкое, отвечающее полной поликонденсации. Состояние резитол — промежуточное. Резольное состояние смолы удобно для приготовления из нее клея.
[c.151]
Каучуковый клей — холодного или теплого отверждения, прочность щва на сдвиг достигает 140 кГ1см . Совмещенные клеи, модифицированные фенолформальдегидными смолами,, имеют еще большую прочность. [c.153]
Соединение аппаратов и деталей, изготовленных из пропитанного графита, осуществляется склейкой фенолформальдегидными вяжущими веществами, так называемыми арзамитами, а также различными клеями. Прочность таких клеящих веществ с пропитанным графитом достигает 25—30 кПсм . [c.75]
Термореактивные пластмассы склеивают смоляными клеями (ВИАМ Б-3, КМ и др.), в-которых фенолформальдегидная или мела-миноформальдегидная смола находится в термореактивной стадии. После нанесения клея на склеиваемые поверхности и их сжатие смола должна перейти в термостабильное состояние. При комнатной температуре эта реакция может продолжаться несколько месяцев. Поэтому в клей добавляют специальные отвердители и склеенные изделия выдерживают при повышенной температуре. [c.629]
Смола фенолформальдегидная — Энциклопедия по машиностроению XXL
Важнейшие термореактивные смолы фенолформальдегидные, моче-вино-формальдегидные, меламино-формальдегидные, эпоксидные, полиэфирные, полисилоксановые. [c.128]Этот метод, обладающий исключительно большой наглядностью и достаточно высокой точностью получаемых результатов, основан на способности некоторых прозрачных аморфных материалов (стекло, целлулоид, пластмассы из эпоксидных смол, фенолформальдегидные пластмассы и др.) изменять свои оптические свойства при упругом деформировании. Под нагрузкой эти материалы становятся оптически анизотропными, приобретая свойство двойного лучепреломления. Такие материалы в практическом обиходе принято называть оптически активными . [c.229]
Смола колумбийская R-39 133 Смолы фенолформальдегидные 123 [c.480]
Термореактивные смолы — фенолформальдегидная, эпоксидная, кремнийорганическая и другие, — быстро переходят при нагреве в вязкотекучее состояние с малой эластичностью и по мере увеличения пространственных связей быстро затвердевают, образуя пространственно сшитые макромолекулы. Формование изделий из термореактивных смол и их вспенивание выполняют на начальной стадии отверждения, когда молекулы смолы способны к вязкому течению. [c.239]
Стеклотекстолит представляет собой слоистый прессованный материал, состоящий из двух или более слоев стеклянной ткани, пропитанной термореактивной смолой. Применяют смолы фенолформальдегидную резольного типа, эпоксидную и кремнийорганическую. [c.243]
Текстолит. Этот материал получают путем прессования уложенных правильными слоями полотнищ ткани, пропитанной искусственной смолой фенолформальдегидного типа. [c.639]
Физические и диэлектрические свойства зависят от полимерного связующего. В качестве связующего применяют фенолформальдегид-ные, эпоксидные, кремнийорганические, меламино-формальдегидные и ненасыщенные полиэфирные смолы. Фенолформальдегидные смолы имеют хорошую адгезию к большинству наполнителей, термостойки, но требуют сравнительно высоких давлений при формовании изделий. Кремнийорганические смолы имеют хорошую водостойкость и повышенные диэлектрические свойства, но высокий коэффициент линейного расширения снижает механические свойства материала. [c.601]
С целью повышения прочности, плотности и износостойкости углеграфитовые материалы пропитывают металлами и смолами. Пропитанный графит выдерживает более высокие давления, но пределы его применения ограничивают температурная и коррозионная стойкость пропитки. В качестве пропитки в основном применяют металлы олово, свинец, баббит, бронзу, а из смол — фенолформальдегидную смолу. Углеграфиты, пропитанные ме- [c.57]
Заготовки, получаемые литьем в оболочковые формы, изготовленные из песчано-смоляных смесей, имеют более высокие точность размеров и формы и чистоту поверхности по сравнению с отливками, получаемыми при литье в обычные песчаные формы. В оболочковых формах изготовляют отливки из серого, ковкого и сверхпрочного чугуна, стали и цветных сплавов. Этим методом изготовляют обычно сложные и ответственные заготовки деталей весом до 100 кг. Оболочковые формы имеют прочные тонкие стенки толщиной 5—Ъ мм, состоящие из смеси 92—95% кварцевого песка и 8—5% термореактивной смолы (фенолформальдегидные смолы типа бакелита и др.). В настоящее время начинают широко применять быстротвердеющие смеси с жидким стеклом, бетонные и др. [c.13]
Физические и диэлектрические свойства зависят от полимерного связующего. В качестве связующего применяют фенолформальдегид-ные, эпоксидные, кремнийорганические, меламиноформальдегидные и ненасыщенные полиэфирные смолы. Фенолформальдегидные смолы [c.320]
Древесностружечные огнестойкие плиты изготовляются из древесных стружек и опилок антипирена, натрового мыла и термореактивных смол (фенолформальдегидных и мочевино-формальдегидных). Процесс изготовления плит состоит из следующих операций подготовка стружек и опилок, смешение массы с раствором антипирена и натрового мыла, сушка массы до влажности 4—5% в сушильных барабанах, смешение со связующими смолами, формование, горячее прессование при 120—140° С и обработка плит. [c.179]
Во время синтеза пластмасс условия образования макромолекул (вязкость среды, концентрация исходных веществ, их соотношение и т. д.) непрерывно изменяются. Поэтому в одной и той же пластмассе могут содержаться линейные макроструктуры с различным числом боковых ответвлений, имеющих различные длину и расположение. При наличии больших и часто расположенных ответвлений пластмасса приобретает большую растворимость, ее механическая прочность и теплостойкость уменьшаются. Такой разветвленной структурой обладают многие синтетические смолы (фенолформальдегидные, амино-формальдегид-ные, полиэфирные и т. д.) в промежуточной стадии смолообразования. [c.3]
Основной способ производства титановых отливок — литье в графитовые формы, литье в оболочковые формы, изготовленные из нейтральных оксидов магния, циркония или из графитового порошка, в качестве связуюш,его используют фенолформальдегидные смолы. При изготовлении мелких сложных тонкостенных отливок применяют формы, полученные по выплавляемым моделям. [c.173]
К синтетическим относятся клеи Бф-2, Бф-4, Бф-6 — растворы фенолформальдегидных смол в спирте пли ацетоне эпоксидный клей Д-9 — синтетическая эпоксидная смола с добавлением отвер-дителя смолы — и ряд других клеев. Подробные сведения о марках клеев, их характеристики и рекомендации к их применению приводятся в справочной литературе [1, 34]. [c.373]
Термореактивные — при первичном нагреве переходят в вязко-текучее состояние, но затем при этой же высокой температуре теряют свою пластичность и переходят в твердое, нерастворимое состояние. Процесс необратим, т.к. при нагреве происходит изменение структуры (например, фенолформальдегидная смола). [c.128]
Введение наполнителей, в частности минеральных, увеличивает стойкость фенольных смол. Фенолформальдегидная смола с асбестовым наполнителем Хейвиг 41 имеет превосходную радиационную стойкость и является одним из наиболее радиационноустойчивых пластиков. Без заметных изменений его можно облучать до доз 3,9-10 эрг г, а повреждение на 25% происходит при дозе 3,9 10 эрг г. Уместно отметить, что такие комбинации смол и наполнителей повышают и термостойкость материалов. Интересен тот факт, что асбест улучшает радиационную стойкость фенольных смол, но не влияет на стойкость каучуков. [c.60]
Текстолит. Для изготовления уплотнений применяют также текстолит, который получают путем прессования улонискусственной смолой фенолформальдегидного типа. Этот мате- [c.569]
Гетинакс электротехнический листовой (ГОСТ 2718-74) представляет собой слоистый прессованный материал, состоящий из двух или более слоев бумаги, пропитанной одной из термореактивных смол фенолформальдегидной и крезол-формальдегидной резольного типа, крезолфеноланилинфор-мальдегидной, эпоксидной. Прессование осуществляется под давлением 10…12 МПа при температуре 160 С. Гетинакс выпускают в листах шириной от 450 до 930 мм и длиной от 700 до 1430 мм. Применяют в качестве электроизоляционного материала для длительной работы при температурах от -65 до +105 С. Марки гетинакса обозначаются римскими цифрами от I до VIII [c.235]
Термореактивные пластмассы производят на основе термореактивных смол фенолформальдегидных, аминоальгидных, эпоксидных, полиамидных, кремнийорганических, ненасыщенных полиэфиров. Пластмассы на основе этих смол отличаются повышенной прочностью, не склонны к ползучести и способны работать при повышенных температурах. Смолы в пластмассах являются связкой и должны обладать высокой клеящей способностью, теплостойкостью, химической стойкостью в агрессивных средах, электроизоляционными свойствами, доступной технологией переработки, малой усадкой при затвердевании. [c.281]
Стеклотекстолит электротехнический листовой (ГОСТ 12652—74)— слоистый прессованный материал, состоящий из двух или более слоев стеклянной ткани, пропитанной термореактивиой смолой. ПримёнЛ 6т смолы фенолформальдегидную резольного типа, эпоксидную кремний органическую. Изготовляют восьми марок. [c.130]
Термореактивная смола, ) Фенолформальдегидная ) Фенолформальдегидная ) Фенол-и крезолформальде шиной от 0,5 до 1,5 мм. [c.298]
Замазки арзамит. Замазки арзамит представляют собой химически стойкие самозатвердевающие материалы органического происхождения. В состав этих замазок входят искусственная смола (фенолформальдегидная), вводимая в виде раствора (ар-замит-раствор), порошкообразные наполнители (графит, кремнезем, сернокислый барий и др.) и катализаторы-добавки, ускоряющие твердение замазок. В качестве катализатора чаще всего применяют химическое органическое вещество — паратолуолсуль-фохлорид. Наполнители и добавки составляют арзамит-порошок. [c.77]
Декоративный бумажнослоистый пластик — листовой материал, полученный горячим прессованием специальных бумаг, пропитанных термореактивными синтетическими смолами (фенолформальдегидны-ми и карбамидными). Основные требования, которым должны удовлетворять декоративные бумажнослоистые пластики, приведены ниже [c.73]
Для фиксации деталей от проворота используют горячую посадку, при которой металлическую обойму нагревают на 100— 150° С выше рабочей температуры, а затем в нее вставляют детали из силицированного графита. При остывании металлическая обойма плотно зажимает деталь из силицированного графита. Если необходимо обеспечить герметичность такой посадки, то ее выполняют с применением клеев или смол (фенолформальдегидной, эпоксидной и др.), которые наносятна деталь из силицированного графита. При такой посадке колец торцовых уплотнений клеящее вещество необходимо наносить только на цилиндрическую часть кольца. Применяют также и накидные гайки для закрепления уплотнительных колец. Вышеперечисленные методы закрепления уплотнительных колец торцовых уплотнений из силицированного графита требуют производить окончательную обработку (доводку) поверхности трения колец после закрепления их в обойму. [c.235]
Для ДФН-1, ДФН-2 и ДФНМ — стеклоткань марки Э толщиной 0,025, 0,06 и 0,1 мм. Лак маркп ЭКР-30 из эпоксидной смолы с отвердителем — смолой фенолформальдегидной резольного типа. Клей БФ-4, наполненный нитридом бора. Фольга никелевая электролитическая толщиной 50 мкм и фольга медная электролитическая оксидированная толщиной 35 и 50 мкм. [c.558]
Особым видом магнитомягких материалов, применяемых в технике высокочастотной многоканальной проводной связи и радиоэлектронике, являются магнитодиэлектрики. Благодаря мелкодисперсному состоянию магнитного материала и обволакиванию отдельных его зерен электроизоляционным материалом магнитодиэлектрики обладают высоким удельным сопротивлением и малыми потерями на вихревые токи, имея, однако, пониженные значения магнитной проницаемости. Основными видами магнитодиэлектриков являются алсифер с неорганической связкой из жидкого стекла алсифер с аминопластовой связкой алсифер с полистирольной связкой карбонильное железо со связкой из смолы фенолформальдегидного типа или двойной связкой — первый слой из жидкого стекла, второй из смолы фенолформальдегидного типа карбонильное железо с полисти-рольной связкой. На этих основах выпускается большое количество марок магнитодиэлектриков, отличающихся друг от друга размерами зерен магнитных материалов и количеством связующего. Потери в магнитодиэлектриках на высоких частотах определяются не только потерями в самом, магнитном материале, но также и диэлектрическими потерями в связующем материале. При выборе последнего следует учитывать технологические свойства (что важно при получении деталей сложной формы), а также механические свойства изделий. Кроме потерь мощности и начальной магнитной проницаемости, большое значение имеет температур- [c.304]
Более высокими качествами обладает усиленная древесина, представляющая собой многослойный березовый шпон (лигнофоли) или крошку (лигностоны), пропитанные фенолформальдегидными смолами и опрессо-ванные под давлением 300 — 500 кгс/см при 150 —180 С. [c.386]
Применяют графито(()торопластовые материалы на основе графита и фторопласта и графитопластовые материалы на основе графита и фенолформальдегидной смолы. Они сочетают свойства своих состав ляюн1Их. [c.381]
В графитовые формовочные смеси горячего отверждения СФТ-1, СФТ-1П в качестве связующего вещества вводят бакелитовый лак — раствор фенолформальдегидной смолы резольного типа в этиловом спирте, а в формовочную смесь ATM — фенолформальдегид-ную смолу № 18 в смеси с уротропином. Для с рмовочных смесей холодного отверждения используют фурановые смолы. [c.317]
Так. на основе одного полимера получают большую гамму материалов С фенолформальдегидной смолой наполнитель древесная мука — пресспо-рошок ткань — текстолит бумага — гетинакс, с очесами хлопка-волокнит, с древесным шпоном — древесно-слоистые пластики (ДСП) [c.127]
Асботекстолит — асбестовая ткань, пропитанная фенолформальдегидной смолой Это бензино — керосиностойкий материал с плотностью 1,6 г/см2 Он обладает хорошими фрикционными, электро- и тегшоизоляционноми свойствами Хорошо сопротивляется колебаниям температуры и влажности. Изготавливают лопатки ротационных бензонасосов, фрикционные диски, тормозные колодки. Выдерживает кратковременно высокие температурь я поэтому применяется в качестве теплозащитного и теплоизоляционного материала (1. ..4 часа при 250…500 С). [c.129]
Для изготовления деталей теплообменников применяют графитопла-сты-антегмиты, полученные путем прессования смеси порошков утлеграфита и фенолформальдегидной смолы. Выпускаются грубы диаметром от 25 до 118 мм, длиной до 6000 мм. Из антегмитов АТМ-1, АТМ-2 и ТАТЭМ изготавливают полосы, плитки, которые применяют для футеровки газоходов, стальных колонн и другого оборудования з целях зажиты от коррозии щш создания теплопроводных элементов для охлаждения или нагрева среды, а также кожухотрубные теплообменники. [c.140]
Фенолформальдегидные покрытия — Энциклопедия по машиностроению XXL
Для формирования фенолформальдегидных покрытий применяют бакелитовые краски ФЛ-723, ФЛ-724-1, ФЛ-724-2, представляющие собой суспензию цинка и алюминия в бакелитовом лаке. Эти краски поставляются в виде трех полуфабрикатов бакелитового лака марки А, спиртовой пасты цинкового крона и алюминиевой пудры. [c.131]Наиболее распространенным методом защиты металлов от коррозии в морской воде являются лакокрасочные покрытия на виниловой (этинолевые краски), фенолформальдегидной (краски АИШ), каменноугольной, битумной основе. Для подготовки металлической поверхности под покрытия применяют холодное фос- [c.403]
Покрытия на основе фенолформальдегидной смолы используют для защиты от коррозии внутренних поверхностей нефтепромысловых резервуаров и емкостей всех типов и назначений для слабоагрессивных условий эксплуатации, когда содержание кислорода не превышает [c.131]
Покрытие фенолформальдегидным грунтом ФЛ-013, по IV классу, для хранения в атмосферных условиях Гр. ФЛ-013. IVA [c.391]
Для рассматриваемого в данном случае покрытия используется битумная мастика № 580, состоящая из смеси битумов с асбестовым волокном и растительным маслом. Она наносится на металл, предварительно очищенный от окислов и других загрязнений. Грунт же наносится на покрытие для создания хорошей адгезии, в частности, фенолформальдегидный грунт В-329. С помощью покрытия, состоящего из двух слоев грунта и четырех-шести слоев битумной мастики, уплотняются как вальцовочные, так и сварные соединения (монтажные сварные швы трубных досок конденсаторов турбин и сварные швы в местах соединения досок с корпусом конденсатора). [c.349]
После пожара заводское здание было восстановлено. Колонны, несущие элементы, крыши, полы изготовлены из железобетона. Полы защищены кислотостойкой плиткой, армированной стекловолокном полиэфирной смолой и асфальтом. Поскольку перерабатываемые растворы содержат ионы хлорида, то все оборудование, которое не контактирует с органикой, защищено от коррозии гуммировкой. До пожара экстракционное оборудование было изготовлено из углеродистой стали и защищено от коррозии армированной асбестом фенолформальдегидной смолой. После пожара защитное покрытие было выполнено из пластика, армированного стекловолокном. Трубопроводы изготовлены из термостойкого стекла и армированного стекловолокном пластика. В качестве запорной арматуры используются остеклованные с мембранами из тефлона вентили Саундерса. Все чаны и смесители-отстойники имеют опорные стальные конструкции. В новом цехе отделение экстракции изолировано от других отделений, усилена его вентиляция, установлен сборный чан для слива органической фазы, увеличено количество дверей для выхода из здания. [c.89]
Полимеризация синтетических смол. Использование инфракрасных лучей целесообразно для запекания термореактивных смол в тонких пленках. Большой интерес представляет, в частности, использование инфракрасных лучей при полимеризации мочевино-формальдегидных и фенолформальдегидных смол, применяемых в качестве покрытий или пропиток на тонких подложках из бумаги и ткани. Достаточно отрегулировать надлежащим образом облучающий поток, чтобы получить в обрабатываемых веществах необходимую для работы температуру, порядка 120—150° С. Отметим, что при этом можно избежать перегрева в окружающем пространстве, так как повышение температуры происходит в самом слое обрабатываемого вещества. [c.341]
Покрытия эмалями на основе фенолформальдегидных смол марки ФЛ отличаются повышенной стойкостью к воздействию атмосферы и воды, а также к колебаниям температуры. [c.55]
Покрытия на основе бакелитовых лаков. Бакелитовые лаки изготовляют на основе фенолформальдегидных термореактивных ре-зольных смол. [c.56]
Бакелитовые лаки представляют собой растворы фенолформальдегидных смол в этиловом спирте. Бакелитовые лаки применяются для пропитки тканей и для покрытия дерева, керамики, железа, бетона и других материалов. Лучшие защитные свойства имеет лак № 86. [c.46]
На основе фенолформальдегидной смолы № 241 выпускаются также бензостойкие грунт Б-241/3 и эмаль Б-241/16 (ТУ ЯН 165—60). Покрытия из этих материалов отличаются высокой бензо- и водостойкостью и устойчивостью к действию водяного пара. Применяются в качестве защитных покрытий емкостей для хранения бензина и бензобаков автомашин. Растворителем служит сольвент каменноугольный. [c.36]
Для атмосферостойких применяются фенолформальдегидные эмали ФЛ-3 кремовая и ФЛ-20 вишневая (ВТУ КУ 380—54). Покрытия устойчивы к периодическому воздействию минерального масла, воды и бензина стойки к воздействию температуры до 150° С. Эмали наносятся по грунту в два-три слоя. Продолжительность сушки при 18—23° С длится 8 ч. [c.38]
Лак СБ-1с (ТУ МХП 2785—54). Лак представляет собой раствор сплава 100-процентной фенолформальдегидной смолы и плавленого янтаря с тунговым маслом в органических растворителях с добавлением парафина, линолеата, свинца и сиккатива. Применяется для покрытия деталей из цветных металлов, [c.38]
Для покрытия изделий, соприкасающихся при работе с минеральными маслами, предпочтение следует отдавать глифталевым и фенолформальдегидным эмалям, как наиболее маслостойким. [c.170]
Для грунтования черных и цветных металлов, а также деревянных поверхностей под лакокрасочные покрытия, стойкие в тропическом климате, могут быть использованы следующие грунты фенолформальдегидные ФЛ-ОЗ-К, ФЛ-ОЗ-КК, ФЛ-013 и ФЛ-ОЗ-Ж грунт-шпатлевка эпоксидная ЭП-00-10 акриловый грунт АГ-Юс, фосфатирующие грунты ВЛ-02, ВЛ-08, ВЛ-023 протекторные цинковые грунты и грунты на сополимере хлорвинила ХС-010, ВХГ-4007, а также новые грунты на основе эпоксидной и меламиноформальдегидной смолы (например, ЭП-09т и др.). [c.211]
В настоящее время наиболее широко используют покрытия на основе фенолформальдегидных, фуриловых, эпоксвдных, полиэфирных смол, а также на основе различных полимерных композиций. Для изоляции наружной и внутренней поверхностей трубопроводов используют полимерные материалы на основе термопластов. [c.131]
Особым типом прессованных пластин служат термореактивные декоративные листы, которые особенно часто применяют в строительной промышленности. Как правило, они состоят из нескольких слоев крафт-бумаги, пропитанных фенолформальдегидной смолой и облицованных декоративными листами, пропитанными и покрытыми меламинформальдегидной смолой. Декоративный лист чаще всего представляет собой бумагу с напечатанным рисунком, имитирующим фактуру дерева, ткани, мрамора и других материалов. Такое сочетание листов подвергается прессованию при температуре около 180° С и давлении 70—140 кгс/см . При такой обработке меламиновая поверхностная пленка становится прозрачной и стойкой против большинства обычных домашних растворителей. Она обладает также большей твердостью по сравнению с большинством органических отделочных материалов, таких, как глазури и лаки, но менее тверда, чем фарфоровая эмаль. Национальная ассоциация электропромышленников предлагает четыре стандартных типа декоративных листов [c.269]
В — от об. до т. кип. в растворах необработанной чистой кислоты любой концентрации [фурановые и фенолформаль-дегидные смолы с асбестовым наполнителем (хавег 41 и 60), эпоксидные смолы, армированные стекловолокном (фиберкаст), хлорированные полиэфиры (пентон), политетрафторэтилен (тефлон, хостафлон, флуон, кель F и др.), саженаполненные фенолформальдегидные смолы (баско-дур)]. И — трубопроводы, покрытия для резервуаров. [c.320]
Краевым эффектом времени называют возникновение со временем на контуре модели после ее обработки наблюдаемых полос интерференции, которые не связаны с напряжениями и деформациями, появляющимися в модели под действием нагрузки. Всякий раз, когда обрабатывается контур, влажность материала по краям изменяется, создавая краевой эффект. Лифт [19] одним из первых показал, что возникновение краевого эффекта объяС -няется поглощением или испарением влаги с поверхности модели. В некоторых случаях явление может протекать еще сложнее. Этот эффект можно предотвратить или затормозить,, если принять соответствующие меры. Модели фенолформальдегидных смол эффективно защищаются покрытиями из парафина (фиг. 5.43). [c.181]
Фенолформальдегидные смолы — продукты поликонденсации фенолов с альдегидами. В зависимости от их соотношения и режимов ведения процесса образуются смолы различного типа основные из них — резоль-ные (при избытке формальдегида) и новолач-ные смолы (при избытке фенола). Л. к. м. на основе этих смол образуют покрытия с хорошей атмосферо- и водостойкостью и очень высокой стойкостью к действию бензина и нефтяных масел. [c.194]
Покрытие фенолформальдегидным грунто-м ФЛ-013 по IV классу. Для [c.583]
Оболочковые формы изготавливают из формовочных песчано-смоля1Шх смесей с термопластичными или термореактивными связующими смолами. Если смола в смеси находится в порошкообразном состоянии, то такую формовочную смесь называют нетакированной, а если зерна песка покрыты сплошной тонкой пленкой смолы, то смесь будет плакированной. Формовочная смесь содержит наполнитель — мелкозернистый кварцевый песок — 100% связующее — пульвербакелит (фенолформальдегидная смола с добавками уротропина) — 6—7% увлажнитель (керосин, глицерин) — 0,2—0,5% растворитель (ацетон, этиловый спирт) — до 1,5 /о. [c.325]
Основная часть химически стойких покрытий на основе реак-топластов содержат в качестве полимерной основы эпоксидные, фенолформальдегидные, эпоксиноволачные, полиэфирные и винил-эфирные смолы, а также как низкомолекулярные, так и высокомолекулярные карбо- и гетероцепные каучуки полибутадиеновые, хлор-преновые и др. [c.240]
СКЛЕИВАНИЕ ДРЕВЕСНЫХ И БУМАЖНЫХ МАТЕРИАЛОВ. Различные породы дерева и древесные пластики склеивают синтетич. клеями (гл. обр. на основе фенольных и карбамидных смол), к-рые по стойкости клеевых соединений к действию воды, микроорганизмов и по прочности склейки значительно более эффективны, чем желатиновые и казеиновые клеи. Древесные материалы, склеиваемые синтетич. клеями, должны иметь влажность не более 14—16%. При большей влажности древесина деформируется, а клеящая способность синтетич. смол, нанесенных на нее, ослабляется. Перед склеиванием древесину высушивают. Поверхности склеиваемых деталей должны плотно прилегать одна к другой (допускается отклонение от параллельности склеиваемых поверхностей не более 0,5 мм). Склеиваемые детали из древесных слоистых пластиков должны иметь равномерно шероховатую поверхность. Глянцевую, блестящую поверхность фанеры, а также участки фанеры, в к-рых клей пробился на поверхность, зачиш ают циклей или шлифуют наждачной бумагой и удаляют пыль. Подготовленные под склейку заготовки хранят при соответствующей темп-ре и влажности воздуха в помещении, изолированном от пыли. В зависимости от условий склеивания клеи наносят на одну или обе склеиваемые поверхности. Фенолформальдегидными клеями, сильно впитывающимися в древесину, обычно покрывают обе поверхности исключение составляют твердые древесные породы. При одностороннем покрытии требуется клея 180—250 е/м , при двухстороннем — 250— 340 [c.171]
Ф. Л. склеиваются столярным и фенольными клеями холодного отверждения, раствором поливинилхлорида в дихлорэтане. Смола 30 — фенолформальдегидная смола, модифицированная полиамидом, который вводится для повышения упругих св-в продукта применяется для изготовления штампов и мастер-моделей, Гарантийный срок хранения смолы в стеклянной или железной закрытой таре 1 год. Композиция для заливки в формы содержит смолу 30 (100 вес. ч.), формалин технич. (4 вес. ч.), отвердитель (контакт Петрова, 7 вес. ч.) и пластификатор (олеиновую к-ту, 1—3%). Композиция готовится тп1,ательным перемешиванием компонентов. Готовую композицию заливают в гипсовые или деревянные формы, покрытые разделит, составом. Формы подвергаются вакуумированию в течение 2—5 м при глубине вакуума не менее 150 мм рт. ст. для удаления пузырьков воздуха, захваченных при перемешивании и заливке смолы. Залитые формы выдерживают нри комнатной темн-ре до загустевания смолы. В отличие от неолей-корита, литых резитов и литого карболита, теплота экзотермич. реакции отверждения смолы 30 невелика, темп-ра в массе смолы после добавления отвердителя поднимается [c.396]
Нанесение на контактные поверхности пористых маслоемких пленок металлов — одно из основных направлений повышения долговечности ограниченно-подвижных шарниров, работающих в условиях коррозионно-механического изнашивания [3]. Для защиты металлических поверхностей от изнашивания в условиях влияния разнга личных агрессивных сред используют покрытия на основе эпоксидной фенолформальдегидной, перхлорвиниловой [c.574]
В различных отраслях пищевой промышленности для защиты от коррозии внутренних поверхностей аппаратов, трубопроводов и арматуры применяют преимущественно следующие полимерные покрытия [13, 14] сополимерови-нилхлоридные фторопластовые пентапластовые поли-олефиновые (полиэтилен, полипропилен, полиизобутилен) полиуретановые фенолформальдегидные кремний-органические каучуковые эпоксидные. [c.17]
В качестве порошков при окраске в кипящем слое используют полиэтилен низкого и высокого давления, поливи-нилбутираль (бутвар), полистирол эмульсионный, полиамидную смолу марки АК-7, иолиоксиметилен, поливинилхлорид, сополимер стирола с метилметакрилатом, эпоксидную смолу марки Э-41, фенолформальдегидную смолу 108. Помимо основных компонентов вводят пигменты и красители, придающие покрытию термостойкость и другие свойства. В частности, для усиления адгезии порошков полиэтилена к обрабатываемой поверхности в порошок вводят графит, а для уменьшения адгезии пыли и пуха к покрытию в исходный порошок добавляют соединения типа ° [c.164]
Возможные повреждения полимерного покрытия обусловливают необходимость и в данном случае применять катодную защиту, поэтому к полимерному материалу предъявляется дополнительное требование — высокая щелочестойкость. Нещелоче-стойкие материалы, такие, как фенолформальдегидные смолы (термореактивные), при подщелачивании среды, вызванном катодной поляризацией, будут разрушаться, тем самым будет разрушаться и защитное покрытие. Опыты по использованию этих материалов в качестве грунтовки под битумное покрытие показали их непригодность в условиях катодной защиты. Поскольку термопластичные полимерные материалы обладают высокой устойчивостью к действию щелочей, то покрытия на их основе с успехом применяются совместно с катодной защитой. [c.128]
На поверхностях труб оросительных холодильников наблюдается образование солевых отложений из орошающей воды. Для борьбы с этим явлением и защиты от водной коррозии ВНИИСК (Всесоюзным научно-исследовательским институтом синтетического каучука) разработан и проверен метод защиты рабочей (со стороны воды) поверхности труб путем их покрытия специальным составом (на основе фенолформальдегидной смолы), предохраняющим от коррозии и образований отложений солей, микроорганизмов, водорослей и т. п. (см. инструкцию 2, стр. 214). [c.75]
Под химически стойкие покрытия рекомендуются следующие грунты фенолформальдегидные (под битумноасфальтовые лаки), перхлорвиниловые (под виниловые покрытия), эпоксидные (под покрытия на основе эпоксидных лакокрасочных материалов). Кроме того, под би-тумно-асфальтовые лаки может быть использован свин цово-суричный алкидный грунт, а под виниловые химически стойкие покрытия—лак ХСЛ с добавлением 20—25% диабазовой муки или свинцового сурика. Битумные и асфальтовые лаки могут наноситься на поверхность без грунта. [c.32]
Асбестоволокнит с фенолформальдегидной смолой в виде листов (фаолит) применяется для теплозащитного покрытия или кислотоупорного материала. [c.478]
Контактный способ формования применяют для изготовления корпусных крупногабаритных деталей из стеклоткани, стеклошпона и стекломатов. Раскроенные куски стеклонапол-нителя укладывают на форму-шаблон, которая покрыта по разделительному слою смолой. После прикатки валиками на первый слой наполнителя наносят смолу с отвердителем и ускорителем отвердения. Таким же образом накладывают последующие слои до получения требуемой толщины детали. В качестве связующих веществ используют смолы холодного отвердения или с подогревом до евысоких температур (фенолформальдегидные, эпоксидные, кар-бомидные). Смолы с высокой температурой отвердения и смолы с испаряемыми растворителями применять не рекомендуется, так как это приводит к образованию пузырей, вздутий и других дефектов. [c.665]
Нередко для окраски применяется способ струйного обливания, когда лакокрасочный материал наносится на поверхность в течение 1. .. 2 мин при помощи сопла, а затем изделие выдерживается 10… 14 мин в парах органического растворителя (сольвент, ксилол, уайт-спирит). В этом случае краска некоторое время остается в жидком состоянии и лучше стекает, значительно уменьщается поверхностное натяжение пленки в нижней части окрапшвае-мой поверхности, затем покрытие равномерно затягивается по всей поверхности. Этот способ в основном применяется при окраске алкидными, масля-но-фенолформальдегидными, битумными и водоразбавляемыми грунтовками и эмалями. Концентрация паров растворителя не должна превышать 50% их нижнего предела взрываемости и контролируется автоматическими сигнализаторами горючих газов типов СГГ-2 и СВК-3. При струйном обливе экономия лакокрасочных материалов доходит по сравнению с окунанием до [c.122]
На основе низковязкой перхлорвиниловой смолы, модифицированной глифталевой и фенолформальдегидной смолами, выпускаются эмали ХВ-113 (ВТУ УХП 181—60) зеленого, серого, голубого, красного и белого цвета. Эти эмали по сравнению с другими перхлорвиниловыми материалами имеют большую концентрацию связующего. Содержание сухого остатка увеличено до 39%, что позволяет снизить количество слоев покрытия и сократить расход дорогостоящих растворителей. [c.42]
Лaкoкpa oчньie покрытия на основе мочевино- и меламино-формальдегидных смол уступают по атмосферостойкости другим материалам, например алкидным, фенолформальдегидным и пр., поэтому для окраски изделий, продолжительное время подвергающихся атмосферным воздействиям, они не рекомендуются. [c.54]
Для атмосферостойких покрытий применяют большой ассортимент грунтов. Для грунтования черных металлов под алкидные, алкидномасляные и масляные эмали применяются грунт свинцовосуричный алкидный, грунт свинцовосуричный на натуральной олифе, грунт КФ-030, грунты фенолформальдегидные ФЛ-ОЗ-К, ФЛ-03-55, ФЛ-013 и глифталевый грунт ГФ-020. [c.168]
Оборудование, работающее в районах с повышенным коли-чеством атмосферных осадков и повышенной влажностью, необходимо защищать лакокрасочными материалами, обладающими минимальной пористостью и хорошей влагостойкостью, например фенолформальдегидными, на основе сополимера хлорвинила, эмалями ХВ алкидными или алкидномасляными. Для обеспечения качественного покрытия эти эмали рекомендуется наносить на грунты, содержащие в своем составе пассивирующие пигменты, например на грунты ГФ-031 или ФЛ-ОЗ-Ж, АГ-1 Ос и др. [c.170]
Фенолформальдегидный клей — Большая Энциклопедия Нефти и Газа, статья, страница 1
Фенолформальдегидный клей
Cтраница 1
Фенолформальдегидный клей ВИАМ Б-3 представляет собой продукт поликонденсации, получаемый из смолы ВИАМ-Б под воздействием керосинового контакта. Клей растворяется на ацетоне или этиловом спирте. [1]
Качество фенолформальдегидного клея и склеенных изделий по мере повышения в исходных фенолах высококипящей части явно ухудшается. [2]
В сборнике уделяется внимание переработке смолы и получению фенолформальдегидного клея, сульфосинтанов и других сланцепродуктов. [3]
В 1962 г. Институтом сланцев был разработан способ синтеза резольного фенолформальдегидного клея КИС-1 ( клей Института сланцев) из фракции фенолов сланцевой смолы, основная часть которых выкипает ниже 280 С. [4]
Дубровский комбинат выпускает небольшое количество волокнистых плит на основе фенолформальдегидного клея марки С-1. Это было вызвано некоторыми технологическими факторами, а не свойствами клея. [5]
Для склеивания без нагрева, при холодном отверждении, применяется фенолформальдегидный клей КБ-3, получаемый из той же смолы Б путем добавки к ней контакта Петрова, являющегося отвердителем. Контакт Петрова состоит из керосина и добавляемой к нему в количестве 20 % ( по весу) кислоты. [6]
На рис. 12 приводятся опытные кривые ползучести при сжатии цилиндрических образцов отвердевшего фенолформальдегидного клея КБ-3, полученные в лабораторных условиях. [7]
Фанерно-клееные трубы марок Ф-1 и Ф-2 изготовляются из березовой фанеры, склеенной фенолформальдегидным клеем. Они характеризуются малой массой и довольно высокой прочностью. [8]
Расход на 1 м1 шва казенно-цементного клея составляет 0 6 — 0 9 кг, а фенолформальдегидного клея — 0 4 — 0 7 кг. [9]
Фенолформальдегидная смола — Большая Энциклопедия Нефти и Газа, статья, страница 2
Фенолформальдегидная смола
Cтраница 2
Отверждение фенолформальдегидной смолы происходит в три стадии. При подсушке смолы или полуфабрикатов стеклопластиков при температуре 80 С смола переходит в следующую стадию ( В) — резитол, в которой может сохранять жизнеспособность довольно длительное время. [16]
Из резольных фенолформальдегидных смол и поливинил-бутираля получают универсальные клеи БФ, представляющие собой спиртовые растворы этих смол. [17]
Пропитка фенолформальдегидной смолой не только обеспечивает непроницаемость графитовой аппаратуры при работе с жидкостями, парами и газами, но и увеличивает механическую прочность графита в несколько раз. [18]
Пропиткой фенолформальдегидными смолами хлопчатобумажных и синтетических тканей с последующей полимеризацией получают текстолит, широко применяемый в электротехнической промышленности как изоляционный материал. Гетинакс получают в результате пропитки специальных сортов бумаги фенолформальдегидными смолами. При использовании в качестве наполнителей песка и асбеста получают фаолиты — материалы, из которых изготавливают трубы, ванны и другие изделия, применяемые для кислых растворов в химической промышленности. [19]
Обезжиренная поверхность фенолформальдегидных смол, как правило, гидрофобна. Ионы Sn2 при сенсибилизации адсорбируются на поверхности, гидрофилизируя ею. При активации адсорбция ионов Ag сопровождается их восстановлением, что способствует гидрофобизации поверхности. Растворы электролитов лучше смачивают обезжиренную поверхность формальдегидных смол. [20]
Механизм образования фенолформальдегидных смол очень сложен и еще окончательно не изучен. Поэтому рассмотрим его лишь в общих чертах. [21]
Изделия из фенолформальдегидных смол обладают высокими механическими и диэлектрическими свойствами, термостойкостью. Поэтому они широко применяются в различных отраслях промышленности. Из фенолформальдегидных смол получают пластические массы ( фенопласты), клей и герметики, антикоррозийные материалы, ионообменные смолы, лаковые покрытия и др. В СССР выпускается около 200 марок фенопластов. Их получают на основе новолачных и резольных смол с использованием наполнителей, пластификаторов и других добавок. В изделия фенопласты перерабатываются методом горячего прессования. [22]
На основе фенолформальдегидных смол изготовляют прессматериалы, слоистые пластики, клеи и покрытия преимущественно технич. Эти материалы атмосферостойки, способны работать в любых климатич. Применение их для бытовых целей ограничено, так как они окрашиваются только в темные цвета и не пригодны для хранения в них пищевых продуктов. Клеи на основе фенольных и модифицированных фенольных смол служат для склеивания металлов, резины, фторопласта, капрона и др. неметаллич. [23]
Клеи на основе фенолформальдегидных смол
В деревообрабатывающей промышленности используют однокомпонентные и многокомпонентные клеи с отвердителями и наполнителями. В качестве однокомпонентных фенолформальдегидных клеев в производстве высших сортов фанеры применяют смолу СФЖ-3011 (С-1) и смолу СБС-1 в производстве древесных пластиков, бакелизированной фанеры и древесной пресс-массы.[ …]
Следует отметить, что на основе фенолформальдегидных смол также можно готовить многокомпонентные клеи.[ …]
При изготовлении фанеры ФСФ, фанерных плит, при облицовывании шпоном деталей мебели и так далее применяют многокомпонентные клеи.[ …]
Основные рецепты фенолформальдегидных клеев даны в табл. 32.[ …]
Приготовленный клей требуется выдерживать в смесителе без перемешивания (0,5—1 ч), а затем подавать к месту переработки. Вязкость клея должна быть 90—150 с по ВЗ-4 при 20° С.[ …]
Особое место среди многокомпонентных клеев занимает пленочньш клей — пленка бакелитовая, изготавливаемая на основе резольных смол — водорастворимой фенолформальдегидной смолы ЦНИИФ С-50 или спирторастворимой СБС-1 и бумаги. Пленку бакелитовую применяют в производстве фанеры высших сортов, а также в производстве мебели. Физико-механические показатели пленки бакелитовой приведены в табл. 33.[ …]
Отверждение таких клеев при нагревании в результате реакции конденсации сопровождается выделением побочных продуктов — воды (в случае клеев, содержащих пароформ) и аммиака (в случае клеев, содержащих уротропин), С образованием пространственной структуры в процессе отверждения теряется подвижность клея, а следовательно, связываются образующимся резитом наполнитель и побочные продукты конденсации — вода или аммиак, которые могут выделиться из резита только за счет диффузии. Кроме указанных продуктов реакции в составе резита может быть часть непрореагировавших мономеров и катализаторов, применяемых при производстве исходных продуктов — фенола, формалина и других, т. е. кислоты, оснозания, соли. Поэтому приготавливать многокомпонентные клеи следует особенно тщательно, так как указанные наполнители, отвердители и примеси в исходных продуктах в значительной мере определяют свойства клеев и качество склеенной продукции.[ …]
К клеям холодного отверждения относятся клеи: ВИАМ Б-3, КБ-3, ВИАМ Ф-9, В31-Ф-9. Клеи готовят, смешивая исходные компоненты перед употреблением на месте применения. Свойства клеев холодного отверждения па основе немодифицированных фенолформальдегидных смол приведены в табл. 34.[ …]
Вернуться к оглавлению Фенолформальдегидные клеишироко используются в водонепроницаемых деревянных панелях и морской фанере BS 1088
Фенолформальдегидный клей является наиболее часто используемым клеем для изготовления ВОДОНЕПРОНИЦАЕМЫХ строительных панелей, балок и многих видов морской фанеры.
Вот ссылка на мою страницу о стандартах и сортах морской фанеры.
Это нелегко для домовладельцев, потому что для отверждения требуется высокое давление и температура.
Что такое фенолформальдегидный клей
Фенолформальдегидные смолы (PF) — это класс синтетических полимеров, получаемых реакцией фенола (спирта, полученного из бензина) с формальдегидом (полученным из метана.)
Хотя фенол, обычно используемый производителями, поступает из нефтехимических источников, продолжаются исследования по использованию био-масла из источников пиролиза для производства смолы PF, что снижает зависимость от ископаемого топлива. В настоящее время это не используется в коммерческих целях.
Бакелит, который является одним из первых широко производимых синтетических пластиков, представляет собой фенолформальдегидную смолу. Он широко использовался в качестве формовочного материала и появлялся в кухонной посуде, прозрачных пластиковых предметах, таких как ручки для волос, декоративные коробки и бесчисленное множество других предметов из пластика.Ранние телефоны были отлиты из бакелита.
Micarta, коричневый льняной картон, пропитанный пластиком, — еще один ранний продукт на основе фенолформальдегида, который выдержал испытание временем.
PF обладает высокой степенью сшивки, что делает отвержденную смолу твердой, термически стабильной, химической и водостойкой.
После того, как смола затвердела, ее нельзя изменить, кроме как механическими методами, такими как сверление или механическая обработка.
Фенолформальдегид также иногда называют фенольной смолой.
И мочевиноформальдегид, и фенолформальдегид выделяют формальдегид после производства. Фенолформальдегид значительно меньше выделяет газ. По этой причине иногда рекомендуется заменить строительную фанеру и деревянные панели, содержащие фенолформальдегид, на мебельную фанеру, содержащую карбамидоформальдегид. Со временем дегазация существенно снижается.
Вот статья, в которой рассказывается о дегазации газообразного формальдегида в изделиях из древесины.
Эту статью из Википедии может прочитать любой любитель химии.
Для чего используется фенолформальдегид?
Фенолформальдегидные смолы являются превосходными клеями для древесины и широко используются для изготовления деревянных панелей строительного класса, таких как фанера и ориентированно-стружечные плиты, которые должны быть водонепроницаемыми.
Отчасти успех этих клеящих смол обусловлен образованием связей между клеем и фенолоподобным лигнином, который является естественным компонентом древесины.
Фенольные смолы также используются для формования изделий, которые могут быть изоляционными и термостойкими. В этом случае добавляются различные наполнители, такие как ткань, волокна и хлопья. В некоторых случаях используются термостойкие ручки приборов, крышки распределителей и тормозные накладки. Шары для снукера и печатные платы — это другие продукты из фенольной смолы.
Статья Британской энциклопедии о фенолформальдегидной смолеХимическая компания поставляет промышленным предприятиям фенольные смолы. В нем есть объяснение 2 типов доступных фенольных смол: новолаков и резолов.Резолы — это смолы, используемые в основном для клеев для фанеры и дерева.
Интересно отметить, что старомодные клеи для крови своей водостойкостью обязаны природному содержанию фенолов.
Клей на основе резорцинатакже обязан своей влагостойкостью природным фенолам.
Какие преимущества фенолформальдегидного клея?
- Влагостойкость I типа — высшее качество. Это означает, что клей выдерживает испытание на кипение, когда образец подвергается нескольким циклам кипячения и сушки.Благодаря этой превосходной водостойкости клей соответствует требованиям стандартов BS 1088, BS 6566 и AS / NZS 2272. В игру вступают и другие факторы, такие как качество винира, но клей подходит для использования на море и на открытом воздухе.
- Устанавливает жесткий и жесткий.
- Фенолформальдегид существует достаточно давно, чтобы зарекомендовать себя в течение длительного времени.
- Фенолформальдегид вступает в реакцию с природным фенолоподобным лигнином, содержащимся в древесине, для улучшения сцепления с древесиной.
Каковы недостатки фенолформальдегидного клея (фенольная смола)
- Для отверждения требуется нагрев и давление.
- Он недоступен для любителей или небольших плотников из-за оборудования, необходимого для обеспечения тепла и давления.
- Фенолформальдегид следует использовать в хорошо вентилируемом помещении, поскольку неотвержденная смола вызывает раздражение и может быть токсичной. После отверждения он выделяет формальдегид. Однако дегазация меньше, чем у карбамидоформальдегидных клеев, и со временем значительно уменьшается.
- Он темного цвета, его можно увидеть в шве морской и внешней фанеры.
- Требуется хороший контакт и давление, чтобы обеспечить прочное соединение, и это не очень хороший материал для заполнения зазоров.
- Он дороже, чем клей карбамидоформальдегидный, что объясняет, почему он не используется для всей фанеры.
Можно ли использовать фенолформальдегид в судостроении?
Он широко используется в судостроении, но только для сборки поставляемой фанеры. Поскольку это требует тепла и давления, немногие деревообработчики могут с этим справиться.
Резорциноловый клей является очень близким родственником фенольных клеев и доступен для плотников. Он прочный, полимеризуется при комнатной температуре и обладает высокой водонепроницаемостью. Он сделан из фенольных соединений природного происхождения.
См. Мою страницу о резорциноловом клее
Мелкий шрифт
Я не претендую на звание эксперта. Я не инженер и не химик. Я делаю ошибки. Эта страница не является рекомендацией продуктов, а предназначена для информации и развлечения. ЕСЛИ вы хотите построить лодку, убедитесь, что вы используете материалы в соответствии с инструкциями производителя.Большинство неотвержденных смол и клеев опасно для здоровья, поэтому наденьте перчатки и работайте в хорошо вентилируемом помещении или наденьте паровую маску. Делай домашнее задание и будь в безопасности.
, напиши мне, если найдешь ошибки, я исправлю их, и мы все выиграем: Кристина
Клеи на основе карбамида и формальдегида, также известные как клей на основе пластиковой смолы. Характеристики и применение.
Мочевинно-формальдегидные клеи являются наиболее важным типом клеев, используемых при производстве фанеры и деревянных панелей.
Что такое карбамидоформальдегидный клей, также известный как клей для пластмассовых смол
Смола карбамидоформальдегидная — это линейка синтетических смол, полученных путем химической комбинации формальдегида (газа, полученного из метана) и мочевины (твердого кристалла, полученного из аммиака).Смолы карбамидоформальдегидные используются в основном для склеивания фанеры, ДСП и других изделий из дерева. Смолы UF полимеризуются в постоянно связанные сети, которые влияют на прочность отвержденного клея. После схватывания и отверждения карбамидоформальдегидные смолы образуют нерастворимую трехмерную сетку, которую нельзя расплавить или подвергнуть термоформованию.
Мочевина формальдегидная изоляция (UFFI) получила плохую репутацию, когда было обнаружено, что она выделяет формальдегид. Эта проблема больше не является серьезной проблемой, потому что практика добавления дополнительного формальдегида для обеспечения полной реакции больше не применяется в современных рецептурах.Выделение газа не является серьезной проблемой в судостроении.
Вот статья, в которой рассказывается о дегазация газообразного формальдегида в изделиях из древесины. pdf файл.
Любой любитель химии может прочитать эту статью из Международного журнала адгезии и адгезивов на карбамидоформальдегидных (УФ) клеящих смолах для древесины.
Для чего используется формальдегид мочевины?
Формальдегид мочевины — широко используемый клей для фанеры, ДСП, деревянных панелей и гнутых ламинатов.
Институт деревообработки включил мочевину Formaldehide в список 6 лучших клеев.
Если склеенный продукт имеет маркировку «мебельный», он, вероятно, содержит карбамид формальдегид и является водостойким. Если указано строительное качество, клей, скорее всего, представляет собой фенолформальдегид и полностью водонепроницаем. Вот ссылка на мою страницу о фенолформальдегидном клее.
Какие преимущества у карбамидоформальдегидного клея?
- Наборы жесткие и жесткие. Это преимущество для гнутых пластин, так как снижает упругость.
- Он используется долгое время и со временем доказал свою надежность. Он прост в использовании и не так требователен к качеству швов, как резорцин или полиуретан.
- Несмотря на то, что его необходимо зажать, он в некоторой степени заполняет зазоры и выдерживает нагрузку (прочный) и после схватывания можно шлифовать.
- Cured Strength UF превосходит древесину, поэтому прочность не является проблемой.
- В зависимости от рецептуры он имеет хорошее открытое время 20-30 минут и не схватывается, как некоторые другие клеи для дерева.Время зажима обычно составляет около 6 часов, в зависимости от температуры и марки.
- Формальдегид мочевины можно смыть водой, пока он не затвердел.
- Влагостойкость II типа. Это означает, что клей устойчив к многократному замачиванию и высыханию. В этом тесте он не кипятится, как клей для морской фанеры. Некоторые бренды, такие как Circa 1850 и Dural, заявляют о статусе водонепроницаемости для своих клеев на основе пластиковой смолы, но почти все бренды водостойкие.
- Поскольку это преимущественно бежевый цвет (цвет варьируется в зависимости от марки, от светло-коричневого до бежевого), он хорошо сочетается с древесиной без выраженных клеевых линий.
- Не деформируется и не ползет при высоких температурах.
- Не дорогой клей.
- Прост в использовании, обычно приобретается в виде порошка, смешиваемого с водой. Для застывания предпочитает более высокие температуры. Большинство брендов указывают 70 градусов F.
Каковы недостатки мочевиноформальдегидного (пластикового) клея
- При добавлении воды при высокой температуре отвержденный формальдегид мочевины может гидролизоваться с выделением формальдегида, что ослабляет клеевое соединение.По этой причине он считается не водонепроницаемым, а водостойким и не используется для изготовления морской фанеры.
- Формальдегид мочевины необходимо использовать в хорошо вентилируемом помещении, поскольку неотвержденная смола вызывает раздражение и может быть токсичной. Это не уникально, так как большинство неотвержденных современных клеев содержат серьезные предупреждения.
- Мочевинно-формальдегидный клей имеет ограниченный срок годности — один год. Его нужно хранить в сухом месте, поэтому он обычно продается в герметичных пластиковых контейнерах.
Можно ли использовать мочевину формальдегид в судостроении?
Водостойкость Формальдегид мочевины находит применение.Порча клея происходит во влажных и горячих условиях.
Его, безусловно, можно использовать в защищенном сухом месте, которое нельзя погружать в воду, но которое может иногда намокать. Он должен получить такую отделку, как краска или лак.
Самодельные самолеты люди успешно использовали их в течение многих лет.
На нем построено много лодок. Вот ссылка на всемирные форумы по яхтингу и лодочному спорту по клеям. Cascamite, Aerolite, Balcotan и др. Неоднократно упоминались как успешные клеи для лодок.
Это не единственный клей, используемый при постройке лодки, но его можно использовать вместе с эпоксидным или другим водонепроницаемым клеем.
С другой стороны, если вы облицовываете, вы не найдете лучшего клея.
Для улучшения водостойкости иногда добавляют меламин. Обычно это тот случай, когда производитель заявляет об улучшенной водонепроницаемости.
AkzoNobel производит клей на основе карбамида и формальдегида, а также другие клеи.Small Print
Я не претендую на звание эксперта.Я не инженер и не химик. Я делаю ошибки. Эта страница не является рекомендацией продуктов, а предназначена для информации и развлечения. ЕСЛИ вы хотите построить лодку с использованием клея на основе карбамида и формальдегида, убедитесь, что вы используете материал в соответствии с инструкциями производителя. Неотвержденная смола опасна для здоровья, поэтому наденьте перчатки и работайте в хорошо вентилируемом помещении или наденьте паровую маску. Делай домашнее задание и будь в безопасности.
Напишите мне, если найдете ошибки, я исправлю их, и мы все выиграем: Кристина
Возможное развитие фенолформальдегидного клея, полученного из дистиллированного черного щелока
Возможное развитие фенол-формальдегидного клея, полученного из дистиллированного черного щелока0101-A2
р.Судраджат и Хан Ролиади 1
Абстрактные
За последнее десятилетие в Индонезии произошел значительный рост целлюлозно-бумажной промышленности. Ежегодно производится не менее двух миллионов тонн бумаги с использованием определенного сырья, например быстрорастущие породы древесины, бамбук, солома и макулатура. Также происходит значительный рост доходов и расширение возможностей занятости на национальном уровне. К сожалению, с точки зрения окружающей среды, черный щелок, образующийся при переработке целлюлозы / бумаги, который до сих пор только сбрасывается или удаляется, вызывает беспокойство из-за токсичности содержащихся в нем фенольных соединений.Было отмечено, что только что выгружено около 13 000 тонн черного щелока с консистенцией 18% при одновременном производстве 15 000 тонн целлюлозы (в сухом виде).
Этот эксперимент был направлен на поиск подходящего метода устранения проблем, связанных с фенолом черного щелока, путем его дальнейшего преобразования в наиболее ценный клей, широко и широко применяемый в фанерной промышленности, то есть фенолформальдегид. Эксперимент был разделен на три стадии, а именно (а) извлечение фенола из черного щелока после первоначальной дистилляции; (b) выбор фенольных соединений из другого источника в качестве добавки для увеличения существующей концентрации фенола в дистиллированном черном щелоке; и (c) разработка оптимальной концентрации фенола, способной развить максимальную прочность сцепления фенолформальдегидного клея.
Оказалось, что извлечение фенола из дистиллированного черного щелока было низким (т.е. 12%). Выбранные кристаллы фенола (p.a) показали лучшие результаты, чем танин, в качестве химической добавки для повышения низкой концентрации фенола в черном щелоке, о чем свидетельствует улучшение свойств фанеры. Оптимальное соотношение добавки фенольных кристаллов к дистиллированному черному щелоку составляло 1:15 (мас. / Мас.). Максимальная сила сцепления фанеры, собранной с использованием фенолформальдегидного клея, полученного из смеси дистиллированного черного щелока и фенольных кристаллов, составляла 24.0 кг / см 2 . Этот показатель соответствует индонезийскому промышленному стандарту прочности сцепления фанеры (т. Е. 14,0 кг / см 2 ).
I. Предпосылки и значение
Черный щелок — это отработанные жидкие отходы, которые сливаются после стадии варки в процессе химической варки целлюлозы, преимущественно крафт, сульфит и соды. Одновременно с этим дренаж предназначен для отделения вареного (размягченного) древесного материала от черного щелока.Черный щелок может содержать растворенные органические древесные вещества (например, удаленные экстрактивные вещества, деградированные углеводы, фенольные соединения и т. Д.) И остаточные химические соединения для приготовления пищи и поэтому обычно токсичен. В отличие от черного щелока, полученного при производстве крафт-бумаги и сульфита, щелок, полученный в процессе производства соды, обычно не восстанавливается из химических веществ для приготовления пищи, а вместо этого просто сбрасывается или сливается на свалку или в водоемы (например, в озера, реки или моря). Фенольные соединения, которые образуются в результате разложения определенного химического компонента древесины (т.е.е. лигнин) во время варки целлюлозы предположительно обвиняют в токсичности черного щелока сульфита. Следовательно, большинство сообществ выступают против отказа от такого черного щелока, поскольку опасаются его негативного воздействия на их жизнь и окружающую среду.
Предполагаемые токсичные фенольные соединения на самом деле являются ценным веществом, которое теоретически может быть преобразовано в дорогостоящее или дорогостоящее фенолформальдегидное соединение. Фенолформальдегид широко и широко используется в качестве популярного клея в фанерной промышленности.
В связи с этим было предложено исследование / эксперимент для оценки возможности выделения / разделения фенольных соединений в содовом черном щелоке для их дальнейшего превращения в фенолформальдегид, который впоследствии был разработан как ценный клей при производстве / изготовлении фанеры. Соответствующие подробности процедур и результатов этого эксперимента будут опубликованы в ближайшее время.
II. Материалы и методы
A. Материалы
Черный щелок, использованный в качестве образца в этом эксперименте, был отходами варки, взятыми с целлюлозно-бумажной фабрики, которая использовала химический процесс соды, расположенного в Бандунге (Западная Ява).Другие химические вещества, которые также использовали, были танином, кристаллами фенола и кристаллами формальдегида.
B. Методы
1. Выделение / экстракция фенольных соединений из содового черного щелока
- Черный щелок сначала делали более щелочным путем добавления определенного количества технического раствора NaOH до тех пор, пока его pH не достигал примерно 10.
- Затем отбирали 10 мл черного щелока с добавлением NaOH и подвергали фракционной перегонке.
- Продолжительность перегонки регулировали до получения / сбора примерно 200 мл дистиллированного раствора черного щелока.
- Дистиллированный черный щелок помещали в специальный контейнер и затем подвергали качественному анализу для определения фенольных соединений.Таким образом, можно определить содержание и извлечение фенола на основе исходного черного щелока соды.
2. Концентрирование дистиллированного черного щелока
- Дистиллированный черный щелок концентрировали кипячением с обратным холодильником при умеренном нагревании. Тогда концентрированный дистиллированный черный щелок можно было бы приблизительно рассматривать как фенол.
- Фенол (концентрированный дистиллированный черный щелок) затем смешивали с кристаллами танина в трех соотношениях (мас. / Мас.), Т.е. последовательно 1: 3, 1: 5 и 1: 7.Смесь при каждом соотношении тщательно перемешивали до гомогенного состояния. Между тем, фенол также отдельно смешивали с кристаллами фенола в трех соотношениях (мас. / Мас.), Также подобных тем, что и для кристаллов танина.
- Смеси либо фенола и кристаллов танина, либо фенола и кристаллов фенола, в каждом из трех соотношений, реагировали с формальдегидом в соответствующей части 1,0: 1,2 (мас. / Мас.). Таким образом, будет образован фенолформальдегид, который будет использоваться в дальнейшем эксперименте в качестве клея при производстве / сборке фанеры.Полученная фанера была впоследствии испытана на ее прочность и другие связанные свойства, которые включали содержание влаги и плотность фанеры, а также прочность соединения клеевого шва (тела) в фанерном сборке.
- Оказалось, что прочность фанеры, скрепленной фенолформальдегидным клеем, в которой фенол был смешан с кристаллами танина, была значительно ниже, чем прочность фанеры, в которой фенол был смешан с кристаллами фенола. Следовательно, кристаллы фенола были предпочтительны в качестве добавки для повышения концентрации разбавленного фенола в дистиллированном черном щелоке.Затем смесь дистиллированного черного щелока и кристаллов фенола подвергали взаимодействию с формальдегидом для получения фенолформальдегидного клея, который в дальнейшем использовали в эксперименте по склеиванию фанеры.
3. Производство фанеры с использованием фенол-фенол-кристаллоформальдегидного клея
- В этом эксперименте отношения смеси кристаллов фенола и дистиллированного черного щелока были расположены на четырех уровнях (мас. / Мас.), То есть последовательно 1:10, 1:15, 1:20 и 1:25.Намерение состояло в том, чтобы выяснить, какое соотношение (а) может обеспечить фанеру в дальнейшем эксперименте по склеиванию с наиболее удовлетворительными (прочностными) свойствами.
- Смеси кристаллов фенола и дистиллированного черного щелока при их определенных соотношениях каждая отдельно реагировали с формальдегидом с образованием фенолформальдегида.
- Полученный фенолформальдегид в дальнейшем был использован в качестве клея в эксперименте по склеиванию при производстве / сборке фанеры. Впоследствии фанера была испытана только на прочность сцепления
4.Анализ данных
Эксперимент по производству фанеры, в котором использовалось каждое из четырех соотношений компонентов смеси как таковых между кристаллами фенола и дистиллированным черным щелоком, был повторен четыре раза. Полученные данные о свойствах фанеры (т.е. только прочности сцепления) были проанализированы с использованием полностью рандомизированного дизайна с односторонней классификацией. В этом отношении классом (единственным фактором) были присущие коэффициенты смешивания. Между тем, производство фанеры, которое реализовало использование смесей концентрированного дистиллированного черного щелока и кристаллов танина в определенных соотношениях; или между концентрированным дистиллированным черным щелоком и кристаллами фенола, также в аналогичном конкретном соотношении, также было воспроизведено четыре раза.Односторонняя классификация также использовалась для анализа результирующих данных такой фанеры (т. Е. Содержания влаги, плотности и прочности склеивания). В данном случае фактором является соотношение в смеси концентрированного дистиллированного черного щелока и кристаллов танина, а также между концентрированным дистиллированным черным щелоком и кристаллами фенола.
III. Результаты и обсуждение
1. Восстановление фенола; Концентрация фенола в черном щелоке соды перед перегонкой была относительно низкой, т.е.е. 2898,3 частей на миллион. Однако после перегонки концентрация фенола в дистилляте черного щелока составляла 348 частей на миллион. Таким способом можно определить степень извлечения фенола, которая составила около 12%.
2. Содержание влаги в фанере варьировалось от 12,6% до 14,4%. Однако дисперсионный анализ данных показал, что разные соотношения смешивания (т.е. 1: 3, 1: 5 и 1: 7) между концентрированным дистиллированным черным щелоком и кристаллами танина, а также между концентрированным дистиллированным черным щелоком и кристаллами фенола не соответствовали. оказывают значительное влияние на влажность.
3. Плотность фанеры составляла 0,59–0,69 г / см 3 . Оказалось, что разные соотношения смешивания концентрированного дистиллированного черного щелока и кристаллов танина, а также концентрированного дистиллированного черного щелока и кристаллов фенола существенно влияют на плотность, при этом чем выше доля кристаллов таннина или кристаллов фенола, тем выше плотность. Однако при определенном соотношении компонентов использование кристаллов фенола позволило получить фанеру с большей плотностью, чем при использовании кристаллов танина.
4. Прочность склеивания фанеры с использованием клея, в состав которого входят кристаллы танина, составляла примерно 1,64 — 6,32 кг / см 2 . Между тем, прочность соответствующей фанеры, в которой использовался клей, включающий кристаллы фенола, была значительно выше, что было доказано посредством дисперсионного анализа данных, то есть 18,36 — 24,96 кг / см 2 . Эта последняя цифра может соответствовать индонезийскому промышленному стандарту прочности сцепления фанеры (т.е. 14,0 кг / см 2 ).
5. Далее представлены результаты эксперимента по производству фанеры, который был осуществлен с использованием клея, полученного из смеси (реакции) дистиллированного черного щелока, кристаллов фенола и формальдегида. В таком составе, как описано ранее, отношения смеси кристаллов фенола и дистиллированного черного щелока варьировали на четырех уровнях. Оказалось, что соотношение уровней 1:10 позволило получить фанеру с наиболее удовлетворительной прочностью сцепления, т.е.е. 24,0 кг / см 2 , что также подтверждено анализом данных.
Рис. 1. Соотношение между соотношением фенола и дистиллята и прочностью сцепления фанеры с использованием клея, содержащего кристаллы фенола, а также содержащего кристаллы танина
Рис. 2. Зависимость отношения кристаллов фенола к дистилляту и прочности сцепления фанеры при использовании клея, содержащего кристаллы фенола
Выводы и предложения
Попытка лабораторного масштаба «Возможная разработка фенолформальдегидного клея, полученного из черного ликера дистиллированной соды» могла бы подытожить несколько примечательных и связанных с этим моментов, а именно:
Извлечение или содержание фенола из исходного (недистиллированного) содового черного щелока было относительно небольшим, т.е.е. 12 процентов. Так же была и концентрация фенола в дистиллированном черном щелоке, то есть 348 частей на миллион. Фактически, такой фенол должен был реагировать с формальдегидом с образованием фенолформальдегидного соединения (PF) в качестве клея для испытания склеивания фанеры.
Таким образом, дистиллированный черный щелок с низким содержанием фенола должен быть сконцентрирован путем добавления других фенольных агентов. Двумя предложенными агентами были кристаллы танина и кристаллы фенола. После этого смесь либо дистиллированного черного щелока и кристаллов танина, либо между дистиллированным черным щелоком и кристаллами фенола отдельно реагировала с формальдегидом в соединения PF для склеивания фанеры.
Оказалось, что плотность и прочность сцепления фанеры, скрепленной ПФ, содержащей кристаллы фенола, были выше, чем у фанеры, содержащей кристаллы танина. Следовательно, соединение PF с содержащимися кристаллами фенола было предпочтительным при его использовании в качестве клея для пробного склеивания фанеры.
Результаты показали, что оптимальное соотношение между добавкой кристаллов фенола и дистиллированным черным щелоком составляло 1:15 (мас. / Мас.). Таким образом, максимальная прочность склеивания фанеры, скрепленной клеем PF, полученным из смеси дистиллированного черного щелока и фенольных кристаллов, составляла 24.0 кг / см 2 . Этот показатель может соответствовать индонезийскому промышленному стандарту прочности сцепления фанеры (т. Е. 14,0 кг / см 2 ).
Черный щелок из дистиллированной соды указывает на обнадеживающие перспективы его добавления с формальдегидом в клей PF для склеивания фанеры. Тем не менее, такой черный щелок с низким содержанием фенола должен быть первоначально сконцентрирован путем добавления определенного количества кристаллов фенола перед смешиванием PF для достижения удовлетворительных характеристик (качеств) либо фанерного узла, либо его соответствующего клеевого тела. сам.
Ссылки
Бессельевр, Э. и М.Шартц. 1976. Обработка промышленных отходов. Mc Graw Hill Inc., Когакуша.
Хади Ю.С. 1979. Penggunaan kayu lapis yang tepat. Buletin Berita Ikatan Alumni Fakultas Kehutanan, Institut Pertanian Bogor, Bogor, (II) 1: 14-17.
Kliwon, S. 1988. Proses pembuatan kayu lapis. Пусат Пенелитян дан Пенгембанган Хасил Хутан, Богор.
Мемед Р., А. Сантосо, дан П. Сутиньо. 1990 г.Pengaruh komposisi perekat fenolформальдегид terhadap keteguhan kayu lapis sengon. Jurnal Penelitian Hasil Hutan, Pusat Penelitian Hasil Hutan, Богор, 8 (3): 105 — 108.
Р. Судрадджат дан Джохор Нинг. 1990. Экстракси фенол дари линди хитам проузес содовой варки dengan cara fraksionasi distilasi. Jurnal Penelitian Hasil Hutan, том 6 (2): 45-50.
1. Р. Судрадят и Хан Ролиади (ведущие)
Центр исследований и разработок лесных товаров
Технологии (RDCFPT)
Jl.Gunung Batu, P.O.Box 182, Богор 16001, Индонезия
Телефон: 62-251-633378, факс: 62-251-633188 и -633414
Электронная почта: [защита электронной почты] и [защита электронной почты]
Resin. Фенолоформальдегидная смола. Получение фенолоформальдегидной смолы
Получение смолы Получение смолы Получение смолыВсе, что нам когда-либо приходилось иметь дело со смолой , но, наверное, не интересно, где и как она образуется. Теперь смола представляет собой очень плотное, вязкое вещество с характерным запахом, знакомым черным или желтоватым цветом.Действительно, смолу можно получить из спилов деревьев (например, сосен).
Смола — отличный строительный материал, поэтому сейчас он использовался в строительных целях.
Конечно, не имея возможности синтезировать смолу , ранее использовались натуральные: янтарь (на самом деле это ископаемая натуральная смола!), Канифоль (используется при пайке), натуральный каучук, копал.
Все это смолы растительного происхождения . Но есть еще смолы животного происхождения , например шеллак .Шеллак широко использовался для изготовления пластин для вертушек, а спиртовой раствор этой смолы наносился на лаковые деревья.
Собственно пару веков назад шеллак считался очень дорогим материалом. Это объяснялось высокой сложностью его обработки из натурального материала. Высокая стоимость продукции заставляла покупать ее у жителей стран Юго-Востока (Индия, Индокитай).
Лишь в конце 19 века химики начали поиски решения этой проблемы.И, конечно же, был найден заменитель шеллака — фенолформальдегидная смола !
Смола фенолоформальдегидная — вещество, получаемое нагреванием смеси формальдегида (формалина) и фенола. Впервые эту химическую реакцию провел немецкий ученый Адольф Байер в 1872 году. В процессе химического взаимодействия формальдегида с фенолом образовались полимер и молекула воды. Конечно, когда у этой реакции был недостаток, который заключался в том, что смола была хрупкой, и реакцию проводили при температуре 140…180 0 ° C. Таким образом, вода, которая образовалась во время реакции, проходила парами.
Это было причиной появления пузырей и пустот. Американский химик Лео Хендрик Бакеланд (1863-1944) одним из первых нашел решение этой проблемы. С 1905 по 1909 год он обнаружил, что хрупкость полимера можно уменьшить, если добавить в реакционную смесь 40-60% древесной муки до затвердевания. Впоследствии древесная мука и другие нерастворимые твердые вещества в полученном полимере, улучшающие его свойства, стали называть наполнителями.Американский химик установил, что если синтез проводится при повышенном давлении, даже когда температура реакционной смеси выше 100 0 ° C, вода не превращается в пар, что положительно влияет на прочность смолы. Поскольку в смоле отсутствуют пузырьки воздуха, такая смола не содержит пустот. Бакелит был произведен промышленным способом в 1910 году, раньше других синтетических смол. В честь этого американского химика названа смола — бакелит .
Бакелит обладает высокой прочностью, жесткостью. Свойство бакелита не проводить электрический ток, широко используется при производстве электрооборудования: амуниции для лампочек, вилок и розеток. Из бакелита можно производить гетинакс (прессованный гальванический материал, пропитанный фенолформальдегидной смолой, в основе которого лежит бумага). Для этого бумагу сначала пропитывают смолой, затем сушат и прессуют под давлением от 10 до 15 атмосфер и температурой 150…160 0 с. Полученный твердый материал — гетинакс , при нагревании его — обугливается, но не размягчается! Но если заменить бумагу тканью — мы получим еще и достаточно прочный материал — текстолит (от лат. Textum — ткань и греч. Lithos — камень). Этот материал, как и гетинакс, широко применяется в электротехнике. Если вам нужно получить материал с очень высокой теплоизоляцией, используйте асбестовую ткань или стекловолокно (стекловолокно).
Получение фенолоформальдегидной смолы
Чтобы получить фенолформальдегидную смолу , нам понадобится 40% раствор формалина (или метаналя) и кристаллический фенол (если его нет, вы можете использовать концентрированный раствор фенола, он доступен в виде карболовой кислоты).При работе с этими веществами необходимо помнить, что они ядовиты.
Итак, чтобы получить фенолоформальдегидную смолу , нам необходимо смешать 2 г кристаллического фенола (или 4 мл концентрированного раствора карболовой кислоты) с 3 мл приготовленного формалина. Затем к смеси добавляют 3 капли концентрированной соляной кислоты HCl. Наблюдая, как смесь нагревается и закипает, превращаясь в вязкую стекловидную массу. Можно слегка охладить колбу при проточной реакции (при охлаждении реакция немного замедлится).
Стеклянной палочкой возьмите образец стекловидной массы и попробуйте растворить в различных растворителях (вода, спирт). Слежу за тем, чтобы масса растворилась.
На этом этапе образуются короткоцепочечные молекулы, и образуется новое вещество , резоль .
В дальнейшем мы получаем очень вязкую массу. Теперь, если мы возьмем образец и попробуем его растворить — он не растворится. Вещество приобрело пластичность за счет образования больших цепочек молекул. Это вещество называется resitol .
По окончании реакции трубку с вязким веществом поместить в емкость с кипящей водой. Постепенно фенолформальдегидная смола все больше затвердевает и превращается в камень. Чтобы получить его, разбив пробирку. Имеет красноватый цвет, не плавится и не растворяется. Если поместить кусок фенолоформальдегидной смолы в открытое пламя, он будет очень медленно гореть, обугливаться, немного искриться и окрашивать пламя в желтый цвет. При горении запах фенола. Остановить реакцию образования фенолоформальдегидной смолы на любой стадии можно, добавив в смесь щелочь (в щелочном растворе реакция идет намного медленнее).
Конденсация фенола с формальдегидом — Большая химическая энциклопедия
Сообщается, что промышленный взрыв был инициирован загрузкой гидроксида калия вместо карбоната калия в хлор-нитросоединение в сульфоксиде [1]. Сухой карбонат калия является полезным основанием для нуклеофильного замещения хлора в таких системах, реакция находится под контролем добавлением нуклеофила. Карбонат не растворяется в ДМСО и сам по себе не обладает значительной нуклеофильной активностью.Гидроксиды есть, чтобы создать соли феноксида в качестве первого продукта. Это лучшие нуклеофилы, чем их предшественники, а также нитросоединения, дестабилизированные основаниями. Результат жара и возможная потеря контроля. По мере приближения к точке кипения ДМСО также становится восприимчивым к экзотермическому разрушению, первоначально до метантиола и формальдегида. Метантиолат является даже лучшим нуклеофилом, чем феноксид, а также довольно эффективным восстановителем нитрогрупп, в то время как формальдегид конденсируется с фенолами при основном катализе в реакции, которая сама по себе вызвала множество промышленных сбоев и взрывов.Таким образом, есть выбор путей к катастрофе. Нуклеофильное замещение в промышленных масштабах в хлор-нитроароматических соединениях ранее продемонстрировало значительную опасность в присутствии воды или гидроксида, даже в растворителях, которые сами по себе не склонны к экзотермическому разложению [2], … [Pg.958]Настоящая соконденсация между фенолом и мочевина может быть осуществлена двумя способами (I) реакция метилолфенолов с мочевиной [98-101] (2) кислая реакция UFC (мочевино-формальдегидный концентрат) с фенолом с последующей щелочной реакцией [102,103].[Pg.1058]
Бэкеланд обнаружил, что относительно стабильный резольный форполимер может быть получен контролируемой конденсацией фенола и формальдегида в щелочных условиях. Эти линейные полимеры фенолформальдегида (PF) могут быть преобразованы в неплавкие сшитые полимеры, называемые резитами, путем нагревания или добавления минеральных кислот. Как показано в структуре 4.80, исходные продукты, полученные при конденсации формальдегида с фенолом, представляют собой гидроксибензиловые спирты. Линейный резольный полимер называется смолой A-стадии, а сшитый резит называется смолой C-стадии.[Стр.120]
Реакция важна, особенно когда, как в пункте (ii), она используется для производства фенольных метанолов. Формальдегид при конденсации с фенолами в присутствии кислотных или основных катализаторов дает смолистые вещества, которые при обезвоживании под давлением дают твердые смолы (бакелит, новолак). (См. J. S. C. I. (C. I.), 1937, 103). [Pg.71]
Методика, основанная на конденсации с фенолом и параформом (используемым в качестве источника формальдегида), была разработана для преобразования отработанного растворителя UNEX (CCD, PEG-400, Ph3-CMPO и FS-13) в твердую плавкую смолу. для утилизации.Полученный материал нерастворим в водных щелочных и кислых растворах и органических растворителях. Включение ФС-13 в сшитый полимер подтверждено физико-химическими методами. Термогравиметрия доказала стойкость отвержденной смолы к высоким температурам … [Pg.141]
Если полимерные процианидины, экстрагируемые из коры хвойных деревьев, будут использоваться в клеевых составах, требующих конденсации с фенолформальдегидными форполимерами, эти реакции должны быть выполнены в условиях кислого pH и из-за ограничений растворимости это, вероятно, потребует использования производных сульфоната.[Стр.201]
Лигнин можно модифицировать конденсацией с фенолом, формальдегидом, аминокислотами [3731] или солями диазония 1387,3881. [Pg.79]
Использование Органический синтез (конденсируется с фенолом и формальдегидом, сополимеризуется с малеиновым ангидридом), растворитель, краситель и фармацевтическое производство. [Pg.1238]
Сегодня формальдегид находит широкое применение для упрочнения желатина, консервирования пищевых продуктов, дезинфекции, дубления кожи и, что наиболее важно, в производстве смол путем конденсации с фенолом (бакелитом) и в синтетических органических химических веществах. промышленность.[Pg.136]
Сообщалось, что реакция крахмала с фенолом в присутствии кислоты Льюиса, такой как AICI3, приводила к получению смол с регулируемой вязкостью расплава.252 Вероятно, продукт является результатом гидролиза крахмала до глюкозы с превращением последнего в 5- (гидроксиметил) -2-фуральдегид, который впоследствии конденсировался с фенолом.253 Для реакции крахмала с фенолом без какого-либо катализатора требуются температуры между 200 и 260 ° C, и полученный смолистый продукт затем отверждается путем конденсации с формальдегид.254 Было сказано, что пережевывание глицерина или фенола с крахмалом и водой не связано с алкоголизом, а вместо этого приводит к образованию полимерных продуктов.255 Реакции с госсиполом256,257 и пропиленгликолем258, которые проводились в присутствии основного катализатора, на самом деле были реакции полимеризации, а не алкоголизы. [Pg.195]
Рис. 3. Конверсия формальдегида (7), выход дигидроксидифенилметана (a) и селективность (o) при конденсации с фенолом в течение 4-6 часов при 180 ° C, по сравнению сфенол / формальдегид-молярное соотношение. Катализатор SAPO-5. |
Рис. 4. Конверсия формальдегида при конденсации с фенолом в течение 4-4 часов при 180 ° C в зависимости от времени реакции. В качестве катализаторов использовали ALPO-5-P (o) и SAPO-5 (a). Молярное соотношение фенол / формальдегид 2/1. |
Таблица 1. Превращение формальдегида и селективность дигидроксидифенилметана при конденсации с фенолом для 4Vfe h при 180 ° C (молярное соотношение фенол / формальдегид 2/1). |
Эпоксидные фенольные клеи — это полиэпоксидные соединения, которые обладают реакционной способностью эпоксидной смолы и термостойкостью фенольной смолы. Их получают путем конденсации эпихлоргидрина и новолачных фенолов (соотношение фенол / формальдегид> 1). В недавнем японском патенте, выданном Mitsubishi Petrochemical Co., описывается получение эпоксидных смол конденсацией эпихлоргидрина с фенольными смолами, полученными из фенола и замещенных альдегидов, например, ванилина. Эти смолы (23) имеют высокое содержание эпоксидной смолы (эквивалентный вес эпоксидной смолы> 200) и относительно высокие температуры размягчения (85-95 ° C).[Pg.136]
Другой важный класс полимерных поверхностно-активных веществ, которые используются для деэмульгирования, — это те, которые основаны на конденсатах алкоксилированного алкилфенолформальдегида, с … [Pg.16]
Формальдегид полимеризуется путем конденсации с фенолом и мочевиной до образуют фенол- и карбамидоформальдегидные смолы, которые являются популярными и недорогими клеями. Это краски и покрытия, которые часто используются в покрытиях в сочетании с алкидными, эпоксидными, полиэфирными или акриловыми материалами для получения прочных гибких пленок. [Стр.240]
Структура альдегида, используемого для конденсации с фенольными соединениями, может варьироваться от формальдегида к другим [73], как показано ниже … [Pg.74]
Эти альдегиды реагируют при конденсации кислоты с фенолами с образованием новолачного типа. товары. Катализируемая основанием конденсация нецелесообразна для ацетальдегида, поскольку он подвергается быстрой альдольной конденсации и реакциям самоосмоления. Кислотная конденсация с участием ацетальдегида или его тримера, паральдегида и фенола дает растворимые и постоянно плавкие смолы, сравнимые с новолаками.Альдегид, не содержащий атома водорода, реагирует аналогично формальдегиду … [Стр.74]
Фенольные смолы были среди первых синтетических смол, исследованных индустрией нанесения покрытий, первоначально использовавшихся для изменения свойств лаков на масляной основе в качестве замены для некоторые натуральные твердые смолы. По существу, они представляют собой растворимые в растворителе фенолформальдегидные конденсаты с химически активными метилольными группами. Они широко используются в качестве сшивающих агентов для термореактивных покрытий для выпечки, в результате чего получаются пленки с превосходной стойкостью к растворителям и коррозии в сочетании с хорошими механическими свойствами.[Стр.68]
Формальдегид реагирует с фенолом путем электрофильного замещения в положениях 2, 4 и 6 фенола и впоследствии конденсируется, образуя плотно сшитую сеть. Эта реакция может катализироваться как кислотными, так и основными катализаторами. Природа полученного продукта во многом зависит от типа фенола, молярного отношения формальдегида к фенолу (f p) и используемого катализатора. Фенольные смолы в основном делятся на два широких класса — резолы и новолаки. [Стр.69]
Получено гидролизом 8-изобутирил-5-метоксиметиленокси-2,2-дим-этилхроман-7-ола (SM) в присутствии 2,4,6-тригидрокси-3-метил. -ацетофенон.Гидролиз SM происходит с высвобождением формальдегида, который конденсируется с фенолом в этих кислых условиях [5716]. [Pg.1603]
Конденсацию останавливают, устанавливая pH до 5-8. Форполимер стабилен в течение нескольких месяцев (> 38 ° C). Дальнейшая конденсация с дополнительным фурфуриловым спиртом или с альдегидами (фурфурол или формальдегид) и с фенолом или мочевиной снова активируется сильными кислотами. [Стр.118]
Смолы Phenohc получают путем конденсации фенола или замещенного фенола, такого как крезол, с формальдегидом.Эти недорогие смолы производились в промышленных масштабах более 100 лет, а в 1990-х годах их производили более 40 компаний в США. Они используются в качестве клея в фанерной промышленности и во многих приложениях, устанавливаемых под капотом, в автомобильной промышленности. Из-за цикличности автомобильной и жилищной промышленности потребление фенола для производства фенольных смол подвержено более сильным колебаниям цикличности, чем в экономике в целом. [Стр.291]
Resoles.Продвижение и отверждение резольных смол на стадиях реакции, аналогичных тем, которые используются для получения смолы, при pH 9 или выше и температуре реакции не должна превышать 180 ° C. Метилольные группы конденсируются с другими метилолами с образованием дибензиловых эфиров и реагируют в орто- и пара-положениях фенола с образованием дифеникнетиленов. Кроме того, дибензиловые эфиры удаляют формальдегид с образованием дифеникнетанов. [Стр.298]
Метиловый фиолетовый [8004-87-3] Cl Basic Violet 1 (17) получают окислением диметиланилина воздухом в присутствии соли, фенола и катализатора сульфата меди.Первоначально в этих условиях часть диметиланилина окисляется до формальдегида и / V-метиланилина. Затем формальдегид реагирует с диметиланилином с образованием N, N,] S7,1S7-тетраметилдиаминодифенилметана, который окисляется до гидроля Михлера [119-58-4]. Гидроль конденсируется с … [Pg.272]
Ди- и триизобутилсульфонами. Диизобутилен [18923-87-0] и тнизобутилены получают нагреванием сернокислотного экстракта изобутилена, полученного в процессе разделения, примерно до 90 ° C.В результате получается выход 90%, содержащий 80% димеров и 20% тримеров. Используйте центры на димере CgH, смесь 2,4,4-триметилпентена-1 и -2. Большая часть смеси димер-тример добавляется в бензин в качестве улучшителя октанового числа. Остаток используется для алкилирования фенолов с образованием октилфенола, который, в свою очередь, этоксилируется или конденсируется с формальдегидом. Водорастворимые этоксилированные фенолы используются в качестве поверхностно-активных веществ в текстильных изделиях, красках, герметиках и герметиках (см. Алкилфенолы). [Стр.372]
Бутилированные фенолы и крезолы.Бутилированные фенолы и крезолы, используемые в основном в качестве ингибиторов окисления и терминирователей цепей, производятся прямым алкилированием фенола с использованием широкого спектра условий и кислотных катализаторов, включая серную кислоту, -толуолсульфоновую кислоту и ионообменные смолы сульфоновой кислоты (110, 111) . За счет использования небольшого количества катализатора и короткого времени пребывания можно добиться преобладания первых образованных ортоалкилированных продуктов. Для получения 2,6-замещенных продуктов в качестве катализатора используют феноксиды алюминия, образующиеся in situ из алкилируемого фенола.Условия реакции контролируют, чтобы минимизировать образование термодинамически предпочтительных 4-замещенных продуктов (см. Алкилфенолы). Чаще всего используется — / fZ-бутилфенол [98-54-4] для производства фенонНС-смол. Группа трет-гути оставляет только два, а не три активных центра для конденсации с формальдегидом и, таким образом, изменяет характеристики смолы. [Стр.372]
Эпоксидные крезол-новолачные смолы (2) получают глицидилированием конденсатов о-крезол-формальдегид таким же образом, как и фенол-новолачные смолы.Конденсаты о-крезол-формальдегид получают в кислых условиях с соотношением формальдегид-о-крезол менее единицы. [Pg.363]
Минимальные скорости реакции составляют при pH 3, и, в отличие от фенолформальдегидных конденсатов, которые имеют минимум при pH 7, схватывание может происходить в нейтральных условиях. [Pg.662]
В коммерческой практике резорцин редко используется сам по себе, но в сочетании с фенолом при конденсации с формальдегидом. Таким материалом является Aerodux 185, представленный Aero Research Ltd (ныне частью Ciba-Geigy) в 1944 году.[Pg.662]
Фенолформальдегидная смола от Suketu Organics Pvt. Ltd .. Поставщик из Индии. Идентификатор продукта 242700.
Поставщик Из Индии
05-09 января
Фенолформальдегидная смола
25 кг в бумажных мешках с полипропиленовой подкладкой
Недавние обзоры пользователей
Этот пользователь еще не получил ни одного отзыва!
Статус проверки
Свидетельство о регистрации компании
Подтверждение личности представителя
Подтверждение предыдущего экспорта / импорта
Представитель компании прошел видеозвонок
Другие документы, такие как мандаты и сертификаты
Другие элементы, похожие на: Фенолформальдегидная смола
Поставщик из Бойзер, Махараштра, Индия
Фенольная смола Наша фенольная смола включает хлопья и порошок.У нас действительно есть порошок различного диапазона от короткого до длинного с хорошей дисперсностью. 25 кг в бумажных мешках с подкладкой из полипропилена. 12 м в 20-футовых контейнерах
Поставщик из Рышнов, Брашов, Румыния
Стерон fiii Используется в деревообрабатывающей промышленности для производства водостойкой фанеры.Контейнеры или брутто
Покупатель из Лудхиана, Пенджаб, Индия
.