Герметик олимп термостойкий: ОЛИМП Битумный кровельный герметик. ДЕКАРТ – производство и реализация лакокрасочных материалов
ОЛИМП Битумный кровельный герметик. ДЕКАРТ – производство и реализация лакокрасочных материалов
Атмосферостойкий кровельный герметик на основе битумного эластомера. Применяется для холодной склейки всех видов рубероида, толя и битумной черепицы, герметизации соединений и заполнения швов при монтаже кровли и водосточных систем, устранения мелких течей. Может наноситься на влажные поверхности.
Торговая марка: OLIMPДоступность: Пожалуйста, выберите необходимый атрибут(ы)
Артикул:
Габариты (Д x Ш x В), вес брутто:
Гарантия лучшей цены
199,00 ₽
≈686,21 ₽ за 1 л
Стоимость доставки:По Москве в пределах МКАД — от 300₽ за 3 часа!
По Московской области — от 1000₽ за 5 часов!
По Москве и МО при заказе от 5000₽ — БЕСПЛАТНО!
По России* при заказе от 10000₽ — БЕСПЛАТНО!
* ознакомьтесь с условиями или рассчитайте доставку в Телеге
В список желаний
ОСОБЕННОСТИ
- Для внутренних и наружных работ
- Предназначен для холодной склейки руберойда, толя, битумной черепицы, для герметизации соединений и швов при монтаже кровли и водосточных систем, для устранения мелких течей на горизонтальных крышах
- Обладает хорошей адгезией к кирпичу, бетону, черепице, древесине, практически ко всем металлическим поверхностям
- Может применяться на вертикальных поверхностях
- Может применяться в соединениях с небольшой подвижностью
- Может наноситься на влажные поверхности
- Оптимальная вязкость при нанесении
- Термостойкий от -40°С до +130°С
- Атмосферостойкий
ПОДГОТОВКА ПОВЕРХНОСТИ
Поверхность должна быть прочной, чистой и сухой, при необходимости обезжирить ее растворителем.
СПОСОБ НАНЕСЕНИЯ
Перед применением картридж выдержать при температуре около +20°С не менее 12 часов. Не применять при температуре ниже +5°C. Герметик наносить с помощью пистолета-апликатора.
- Срезать верхушку резьбовой части, плотно прикрутить наконечник
- Верхушку наконечника срезать под углом 45° на ширину заполняемого шва
- Картридж вставить в пистолет-аппликатор
- Равномерно заполнить шов и разровнять влажным шпателем
Поверхность герметика застывает примерно через 20 мин после нанесения. Полное высыхание в течение 2-3 дней. Сразу после работы инструменты очистить уайт-спиритом.
Термостойкий герметик «Олимп» в Новосибирске №23594275
Описание
Термостойкость до +1500 С;Для монтажа ПЕЧЕЙ, ДЫМОХОДОВ,ОТОПИТЕЛЬНЫХ И ТОПЛИВНЫХ СИСТЕМ;
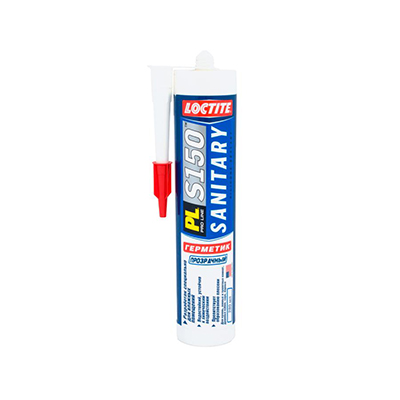
Герметик для соединений находящихся под воздействием высоких температур. Изготовлен на базе силиката натрия (не содержит асбеста). Подходит для контакта с бетоном, кирпичём и металлом.Не растрескивается и не крошится. Нельзя использовать для соединений, постоянно находящихся в контакте с водой. Не наносить при температуре ниже +5 С. Термостойкость застывшего герметика до +1500 .Предназначен для герметизации, заполнения швов, трещин, отверстий в печах, дымоходах, других отопительных системах.
Фотографии
Герметик термостойкий печной ОЛИМП в Твери
- Меню
- Каталог
- Назад
- Печи для бани
- Печи-камины
- Каминные облицовки
- Отопительные печи
- Котлы отопительные
- Садовые печи
- Дымоходы, баки
% PDF-1. 5
%
4 0 obj
>
endobj
xref
4 87
0000000016 00000 н.
0000002334 00000 н.
0000002430 00000 н.
0000003082 00000 н.
0000003671 00000 н.
0000004102 00000 п.
0000004136 00000 п.
0000004180 00000 н.
0000004222 00000 п.
0000004264 00000 н.
0000004306 00000 н.
0000005003 00000 п.
0000005748 00000 н.
0000005887 00000 н.
0000006528 00000 н.
0000007147 00000 н.
0000007347 00000 н.
0000007936 00000 п.
0000008065 00000 н.
0000008727 00000 н.
0000009279 00000 н.
0000009742 00000 н.
0000012391 00000 п.
0000013039 00000 п.
0000013104 00000 п.
0000013169 00000 п.
0000013234 00000 п.
0000013347 00000 п.
0000013458 00000 п.
0000013571 00000 п.
0000013640 00000 п.
0000013724 00000 п.
0000017088 00000 п.
0000017358 00000 п.
0000017528 00000 п.
0000017553 00000 п.
0000017861 00000 п.
0000017930 00000 п.
0000018023 00000 п.
0000034452 00000 п.
0000034712 00000 п.
0000034977 00000 п.
0000035002 00000 п.
0000035391 00000 п.
0000066825 00000 п.
0000067072 00000 п.
Термостойкий, отверждаемый УФ-излучением лак для экстерьера самолетов
Автор Ричард У.
Бэрд , старший инженер-химик и руководитель проекта, The Boeing Company
Рис. 1. Типичная картина обесцвечивания (показана в относительной шкале)Abstract
Мы оцениваем возможность разработки и внедрения термостойкой, отверждаемой ультрафиолетом прозрачной краски или лака для наружной отделки самолетов. Прозрачный слой защитит нижележащую краску от обесцвечивания при эксплуатации, тем самым улучшая ее внешний вид и технические характеристики. Представленные образцы непигментированного уретана были протестированы в соответствии с нашими требованиями к качеству отделки и инженерным характеристикам, с результатами, приближающимися к результатам аттестованных термически отвержденных уретанов для наружных работ.Были определены пути разработки и внедрения лака в производство. Испытания на выдержку при нагревании нескольких циклов составов прозрачных лаков от двух поставщиков показали существенно улучшенную термостойкость по сравнению с термически отвержденным прозрачным лаковым покрытием, используемым в качестве контроля.
Сводка
Были определены потенциальные возможности использования быстроотверждаемых красок для наружных работ для самолетов с целью сокращения времени цикла окраски и повышения качества отделки и долговечности для клиента авиакомпании.Мы определили, что значительные преимущества могут быть получены с помощью пигментированных и прозрачных красок, отверждаемых ультрафиолетом (УФ-отверждаемых), при нанесении на участки, требующие специальных покрытий, и когда эти покрытия будут вызывать недопустимые задержки в технологическом процессе, если время их отверждения не будет очень коротким.
Примером такого применения является выявленная потребность в термостойких покрытиях для вытяжных вентиляционных зон, что является предметом данной статьи. Был составлен список технических требований и требований к внешнему виду для этого термостойкого покрытия, включая уровень термостойкости, который считается необходимым для обоснования его использования.Эти требования основаны на требованиях, предъявляемых к краскам для наружных работ, квалифицированным в настоящее время, и включают дополнительные требования, специфичные для этого специального применения.
Два разработчика рецептур были определены как имеющие ресурсы и мотивацию для разработки УФ-отверждаемых лаков для наружного применения в самолетах. Чтобы облегчить процесс разработки, было налажено тесное сотрудничество между разработчиками рецептур, их поставщиками сырья и поставщиками оборудования для УФ-отверждения. Был установлен закрытый путь развития, который в конечном итоге привел к использованию в производстве лака, отверждаемого УФ-излучением.На каждом этапе разработки перед продолжением оценивается экономическое обоснование перехода к следующему этапу.
Недавно мы завершили несколько раундов тестирования, изменения состава и повторного тестирования рецептур лаков от этих двух поставщиков. Последние составы близки к удовлетворению основных технических требований, с небольшими корректировками, необходимыми для полного удовлетворения этих требований. Усилия разработчиков рецептур по повышению термостойкости этих формул привели к существенному улучшению по сравнению с термически отвержденным прозрачным лаком, испытанным в качестве контроля.
Проблема, которую необходимо решить
Обесцвечивание краски в результате воздействия тепла возле вентиляционных отверстий. Лаки, разрабатываемые в этой работе, были оценены на предмет их способности уменьшать пожелтение термически отвержденных уретановых красок, наносимых снаружи после небольших выхлопных отверстий на нижней стороне самолета. Рис. 1 представляет собой схематическое изображение вытяжного отверстия и области ниже по потоку, наиболее подверженной воздействию тепла. Эти краски подвергаются воздействию температур до 150 ° C (302 ° F) в течение длительного периода эксплуатации.В течение нескольких месяцев наблюдается сильное обесцвечивание (пожелтение и потемнение). Нанесение верхнего покрытия с соответствующим составом ограничит доступ кислорода воздуха к этой краске, тем самым замедляя процесс пожелтения. Лак должен иметь очень быстрое отверждение, чтобы свести к минимуму влияние процесса окраски из-за добавления шагов для маскировки, нанесения и отверждения лака, отсюда упор на составы, отверждаемые УФ-излучением.
Общая площадь, требующая защиты, относительно мала (<5 кв. М или <50 кв. Футов), поэтому ожидается, что готовые системы отверждения, разработанные для автомобильной отделки послепродажного обслуживания, могут быть адаптированы для этого применения.По крайней мере, одна такая система была сделана доступной с взрывозащищенной модернизацией, чтобы соответствовать требованиям NFPA Article 500, Class I, Division I (требование в наших покрасочных цехах).
Почему УФ-отверждение? Драйверы для использования УФ-отверждаемых авиационных красок.
Наилучшая возможность сократить время обработки краски — это стадия отверждения. В то время как самые быстрые термически отверждаемые формулы требуют нескольких часов для достижения состояния «высыхания до маски», УФ-отверждаемые краски полностью отверждаются за секунды. Более того, в этот момент они готовы к полету, а термически отвержденная краска требует дальнейшего отверждения, чтобы быть готовой к полету.Кроме того, поскольку УФ-отверждение может быть выполнено без нагревания покрасочного ангара, во время отверждения краски могут выполняться другие работы, в отличие от термически отвержденной краски. Краски, отверждаемые под действием УФ-излучения, обладают дополнительным преимуществом, помогая снизить выбросы летучих органических соединений (ЛОС), поскольку они обычно содержат до 100% твердых веществ. (В рецептуре краски «100% твердых веществ» весь лакокрасочный материал, который достигает детали, остается сохнуть без потерь на испарение. Это включает реактивный разбавитель в составах, отверждаемых УФ-излучением.)
Требования к УФ-отверждаемому термостойкому лаку для наружных работ.
Для получения максимальной пользы от использования УФ-отверждаемого термостойкого лака для наружных работ необходимо выполнить ряд требований. Вместе они представляют собой серьезную задачу по формулированию и интеграции процессов, аналогичную той, с которой сталкивается автомобильная промышленность, но с несколькими дополнительными проблемами, уникальными для отделки коммерческих самолетов. Требования к термостойкости лака в настоящее время разрабатываются.
Требования включают:
- Распыляемость близка к свойствам термоотверждаемых красок.
Для оптимального качества отделки и удобства использования в магазине краска должна иметь вязкость при распылении, аналогичную вязкости термически отверждаемых формул, и аналогичную «выравнивающую» способность (способность образовывать гладкую пленку) и устойчивость к растеканию и потеканию. Чем ближе характеристики распыления к характеристикам обычной краски, тем быстрее будет процесс обучения для маляров. Доработки будут сведены к минимуму.Типичный подход состоит в том, чтобы составить краску с высокой вязкостью при комнатной температуре, а затем нагреть краску, чтобы снизить вязкость до диапазона, пригодного для распыления. Затем выравнивание и устойчивость к образованию провисаний регулируются скоростью восстановления вязкости по мере охлаждения пленки краски на поверхности.
- Требование «времени зависания». Вязкость при комнатной температуре должна быть достаточно высокой, чтобы выдерживать пленку толщиной около 0,002 дюйма (для адекватной защиты находящейся под ней краски), нанесенную одним слоем на вертикальную поверхность в течение периода, достаточного для того, чтобы дать время вернуться во влажное состояние.
пленка с полимеризационными лампами.Использование тиксотропных добавок обычно необходимо для увеличения «времени выдержки» до приемлемой длины при сохранении хорошего выравнивания. Без этих добавок краска либо (1) продолжала бы медленно «выравниваться», в конечном итоге развивая провисания после интервала, который обычно слишком короткий, чтобы дать время вернуться с системой отверждения, либо (2) выравнивалась бы не полностью, оставляя неприемлемо грубый «оранжевый» -peely »финиш.
- Требования к процессу отверждения. Сложность оборудования, вес, стоимость и энергопотребление должны быть минимизированы.Выработка озона должна быть минимизирована или предотвращена для получения максимальной экологической выгоды. Оборудование должно быть безопасным в использовании, портативным и достаточно легким, чтобы работать на передвижной малярной платформе или тележке. Краска должна быть достаточно чувствительной, а УФ-излучение — достаточно высоким, чтобы обеспечить достаточно высокую степень покрытия отверждающими лампами по окрашенной поверхности, чтобы максимизировать экономию времени растекания и компенсировать более высокие затраты на оборудование, связанные с УФ-отверждением.
Также существует требование пожарной безопасности, предусматривающее взрывозащищенное исполнение (NFPA Article 500, Class-I, Division-1), чтобы обеспечить отверждение в ангаре для краски.Эти факторы, как правило, отдают предпочтение системе отверждения УФ-А с одной лампочкой, которая либо является искробезопасной, либо может быть заключена в оболочку инертного газа с положительным давлением.
- Требование отверждения от чрезмерного распыления. Поскольку невозможно направить 100% капель избыточного распыления в выхлопную систему ангара для краски, каждая поверхность ангара в конечном итоге покрывается тонким слоем капель избыточного распыления. Это не проблема для термоотверждаемых красок; капли просто затвердевают там, где они приземляются. В случае УФ-отверждаемой краски капли избыточного распыления будут оставаться влажными неопределенно долго, что явно недопустимо.Процесс вторичного отверждения («двойное отверждение») является типичным подходом: капли избыточного распыления в конечном итоге достаточно затвердевают с помощью механизма вторичного отверждения, чтобы минимизировать проблемы безопасности (обычно в течение 12–24 часов).
Этот вторичный механизм не требует УФ-облучения и может действовать в темноте.
- Технические и внешние требования. В дополнение к вышеперечисленным, формула краски должна удовлетворять всем техническим требованиям и требованиям к внешнему виду, установленным для термически отверждаемой краски.В Таблице 1 (стр. 44) перечислены технические характеристики и внешний вид, используемые в качестве предикторов успешного прохождения квалификационных тестов и тестов внешнего вида. Таблица 2 (стр. 45) иллюстрирует прогресс, достигнутый в удовлетворении этих требований в формате «стоп-сигнал» (зеленый = обгон, красный = сбой, желтый = незначительный обгон, требуется регулировка).
- Требования к жаростойкости. Наконец, состав краски также должен быть устойчивым к пожелтению и замедлять процесс пожелтения основной краски до такой степени, чтобы оправдать время и затраты на добавление дополнительного слоя краски.Это требование оказалось особенно сложным, и, хотя в достижении этой цели был достигнут значительный прогресс, мы не можем предвидеть, в какой степени обесцвечивание может быть в конечном итоге смягчено.
По этой причине мы установили требование «наилучшая доступная производительность». Этот неопределенный уровень будет оцениваться для определения экономического обоснования применения лака в качестве термостойкого покрытия.
Прогресс на сегодняшний день
Мы протестировали составы прозрачных лаков от двух поставщиков. Составы прошли несколько циклов тестирования, изменения состава и повторного тестирования. В настоящее время мы достигли существенного снижения обесцвечивания УФ-отверждаемого прозрачного лака, нанесенного на контрольное цветное покрытие, по сравнению с термически отвержденным контрольным прозрачным покрытием, нанесенным на то же самое цветное покрытие. Эти составы прозрачных лаков также проходят требования прикладных и инженерных испытаний, с незначительными корректировками, необходимыми для перехода к полной батарее квалификационных испытаний. Однако неясно, наблюдаем ли мы еще какое-либо уменьшение обесцвечивания основной краски. В ближайшие месяцы мы планируем испытать несколько новых составов, которые, как мы надеемся, улучшатся.
При испытаниях на пропитку алюминиевые образцы для испытаний были покрыты стандартным набором термоотверждаемых красок (конверсионное покрытие, грунтовка и пигментированный уретан), а затем покрыты и отверждены термически отвержденным или отверждаемым ультрафиолетом прозрачным лаком. Измерения цвета и блеска были получены до экспонирования и несколько раз во время экспонирования для выявления тенденций.Панели подвергались воздействию температур от комнатной до 150 ° C (302 ° F). Значения цвета использовали для получения дельта-Е как функции времени выдержки и температуры.
Рисунок 2. Результаты теплового замачивания: Delta-E в зависимости от температуры через 60 дней, термически отвержденное цветное покрытие + прозрачные лаки На рисунке 2 показано наблюдаемое поведение дельта-E (следовательно, обесцвечивание) при продолжительности замачивания 60 дней в диапазоне температура выдержки изучена. На каждом графике дельта-Е нанесена в зависимости от температуры выдержки. На трех графиках показана термически отверждаемая белая краска (цветное покрытие) без прозрачного лака (темно-синий), та же краска с наиболее эффективным термически отверждаемым прозрачным лаком (светло-синий) и с наиболее эффективными лаками, отверждаемыми УФ-излучением (красный и фиолетовый) от двух поставщиков.
После 60-дневного замачивания было замечено незначительное обесцвечивание при «контрольном» замачивании при комнатной температуре и при 70 ° C (158 ° F), что близко к максимальной температуре, наблюдаемой вдали от вентиляционных отверстий горячего выхлопа. Значительное изменение цвета наблюдалось для всех комбинаций красок, испытанных при 120 ° C (248 ° F) и 150 ° C (302 ° F). Эти температуры были выбраны для имитации условий около вентиляционных отверстий горячего выхлопа. В исследованном диапазоне температур выдержки наблюдается постоянное улучшение прозрачных лаков, отверждаемых УФ-излучением, по сравнению с прозрачными лаковыми покрытиями, хотя ни один из прозрачных лаков, отверждаемых УФ-излучением, не продемонстрировал каких-либо явных доказательств уменьшения обесцвечивания основной пигментированной краски. Значительный масштаб улучшения (около 50% для наиболее эффективной рецептуры) дает нам надежду на то, что мы сможем, по крайней мере, сопоставить характеристики белой краски с системой «базовый слой-прозрачный лак».
Эти результаты, вместе взятые, являются очень многообещающими, учитывая, что после длительного периода разработки мы находимся в той точке, где мы можем квалифицировать один или оба из этих УФ-отверждаемых составов в соответствии с применимыми внешними спецификациями для использования в качестве универсального. , быстросохнущий лак.
Разработка УФ-отверждаемой краски в Boeing — закрытый процесс
Рисунок 3.Блок-схема разработкиПроцесс разработки шел по схеме, показанной на рисунке 3. Это серия этапов разработки, связанных между собой воротами. На каждом этапе оцениваются результаты тестирования и выполняется анализ бизнес-модели, чтобы поддержать решение о переходе к следующему этапу. Фазы разработки следующие:
- Определение разработчиков рецептур.
Мы начали процесс разработки с поиска в отрасли разработчиков рецептур, у которых либо был готовый продукт, способный удовлетворить наши требования, либо у которых были ресурсы и заинтересованность в разработке для нас лака.Мы определили двух разработчиков рецептур, которые начали процесс составления и предоставления жидких и отвержденных образцов для тестирования. Пока мы работаем с этими разработчиками рецептур, мы продолжаем проверять наличие дополнительных источников либо готового продукта, либо возможности разработки продукта, отвечающего нашим требованиям.
- Итеративное скрин-тестирование представленных материалов. Для ускорения процесса тестирования используется серия экранных тестов, которая является подмножеством полной батареи квалификационных тестов, включенных в спецификацию краски.Батарея для испытаний приведена в таблице 1. Первые пять свойств проверены только на образцах, нанесенных и отвержденных в нашей лаборатории. Они дают нам общее представление о свойствах спрея и отвердителя и, следовательно, о пригодности формулы для нанесения.
Все образцы проверены на остальные перечисленные свойства. Все остальные свойства, за исключением термостойкости, дают нам представление об общих технических характеристиках краски для наружных работ.
После начальных испытаний следует несколько итерационных циклов тестирования, отчета о результатах составителям рецептур и представления переработанных рецептур до тех пор, пока мы не протестируем рецептуры, которые близки к удовлетворению требований экранных тестов.Как и ожидалось, самые большие проблемы заключались в обеспечении адекватной поверхности и сквозного отверждения с помощью одной луковицы, а также в устойчивости к пожелтению во время ускоренного атмосферного воздействия. Однако полученные на сегодняшний день результаты предлагают способы удовлетворения этих требований путем корректировки формулы краски и процесса отверждения.
- Квалификационные испытания и включение в спецификацию. Как только мы получим формулу, удовлетворяющую требованиям экранного теста, она пройдет через всю батарею квалификационных тестов.
Мы ожидаем еще нескольких итерационных циклов тестирования и повторной подачи в виде корректировок пакета фотоинициатора, тиксотропов и других добавок, а также остаточных корректировок реактивных компонентов разбавителя и олигомера.
- Параллельная разработка системы лечения. Параллельно с составлением краски мы оценили несколько подходов к процессу отверждения. Чтобы получить адекватное сквозное отверждение при наименьшем времени воздействия и наименьшем УФ-излучении, олигомерная смола, реактивный разбавитель и фотоинициатор должны быть оптимизированы с учетом энергетической освещенности и спектральной мощности системы отверждающих ламп.Для формул, которые в настоящее время разрабатываются, мы определили оптимальный диапазон УФ-излучения и диапазон плотности энергии для получения сквозного отверждения с максимальной степенью покрытия (то есть минимальным временем отверждения) для разрабатываемых формул красок.
Чтобы удовлетворить наши требования к безопасности и технологическому процессу, мы делаем упор на технологию УФА с одной лампочкой. Мы приняли обычную технологию УФ-ламп из-за ее технической зрелости. Хотя отверждение на основе светодиодов было бы идеальным для нашего применения — и хорошо зарекомендовало себя для отверждения пленок с печатной краской, — ему все еще не хватает технической зрелости в уровнях производительности, необходимых для отверждения пленок краски с требуемой степенью покрытия.Эта технология быстро развивается, и мы будем тестировать составы, излеченные с помощью этой технологии.
Доставка ультрафиолетового излучения на окрашенную поверхность может быть достигнута либо (1) светильниками для ультрафиолетовых ламп, установленными по всему ангару и окружающими самолет (включая нижние блоки пола), либо (2) сканированием ламповой системы по поверхности. Первая схема, в то время как концептуально простая (просто нажмите переключатель, чтобы воздействовать на лечение) и быстрая (все окрашенные области экспонируются одновременно), была отклонена как чрезмерно дорогостоящая и небезопасная из-за рассеянного УФ-излучения. Кроме того, поскольку во время лечения ангар будет закрыт, одновременное выполнение операций невозможно. Таким образом, мы переняли идею сканирования УФ-лампами окрашенной поверхности, как это делается в автомобильной промышленности. В нашем случае движется массив ламп, а не окрашенная поверхность. Таким образом, фактическое эффективное время отверждения — это время, необходимое для «окраски» поверхности с необходимой плотностью энергии на единицу площади УФ-излучения. Это общее время отверждения зависит не только от УФ-излучения и чувствительности краски, но и от времени, необходимого для установки и перемещения ламп отверждения по всей окрашенной поверхности.
- Масштабирование для отверждения больших тестовых подложек. Когда мы получаем подходящую формулу краски и связанный с ней процесс отверждения в лабораторном масштабе, следующим шагом будет масштабирование до лабораторной системы, способной отверждать большие субстраты способом, имитирующим процесс покрытия методом «проталкивания щеткой», ожидаемый на самолет.
- Нанесение и отверждение на смоделированных секциях самолета. Следующим этапом разработки является масштабирование до серийного прототипа системы отверждения, которая является взрывозащищенной и способной работать на платформе для покраски или мобильной тележке на полу.Этот прототип будет оцениваться при моделировании типичных сценариев покраски самолетов и устранении любых остаточных проблем с системой отверждения или красками. Для этих испытаний будут использоваться сломанные панели обшивки фюзеляжа, размер которых аналогичен площади, которая будет окрашиваться при производстве, которые будут проводиться в покрасочном ангаре с малярами, которые будут красить самолеты клиентов.
- Заводские испытания на самолетах заказчиков. Наконец, если все будет продолжаться номинально, мы перейдем к системе отверждения с сетчатой конфигурацией и производственным испытаниям на самолетах заказчиков, выбранных таким же образом, как и для любых новых систем покрытия или маркировки.
По мере завершения каждого этапа разработки мы будем проводить бизнес-пример для перехода к следующему этапу. В настоящее время мы оцениваем лучший способ прохождения квалификационного тестирования. После того, как одна или несколько красок пройдут батарею квалификационных тестов, мы вернемся к бизнес-модели, чтобы определить, имеет ли смысл переходить к первоначальной реализации. Последующие этапы разработки (крупномасштабные лабораторные испытания, малярные испытания и производственные испытания) будут соответственно спланированы.Очевидно, что в любой момент бизнес-модель может не завершиться, и тогда результаты будут задокументированы для возможной повторной оценки в будущем по мере улучшения технологий и изменения потребностей бизнеса.
Однако, даже в случае решения о прекращении работы, мы ожидаем, что уникальные ресурсы для тестирования приложений и лечения, выделенные для разработки, можно будет использовать другими способами. Примером этого может быть предоставление услуг по тестированию в поддержку контрактных исследований и разработок, порученных нашим лабораториям.
Совместные усилия
Как описано ранее, разработка успешной формулы УФ-отверждаемой краски должна быть увязана с разработкой системы отверждения для нее. Чтобы облегчить этот процесс, оба составителя красок тесно сотрудничают с разработчиком системы отверждения и поставщиками сырья, а также с конечным пользователем. Встречи между различными заинтересованными сторонами проводятся для управления процессом разработки, в частности, для обеспечения наиболее эффективного использования ресурсов и опыта.
Выводы
Для достижения цели создания лака, отверждаемого под действием ультрафиолетового излучения, который обеспечивает эффективную защиту от обесцвечивания, вызванного воздействием тепла, предстоит еще многое сделать. Даже если мы не добьемся полезной термозащиты, формулы лаков, разработанные в этой работе, могут найти применение в качестве специальных покрытий в других частях самолета. Если в ходе дальнейшей работы будут разработаны пигментированные версии, возможно больше приложений.
Ричард У. Бэрд имеет 26 лет инженерного опыта в компании Boeing, в том числе 23 года в сфере коммерческих самолетов и исследований и технологий Boeing.Его достижения включают разработку УФ-отверждаемых внешних декоративных покрытий; разработка и внедрение прочных декалей и аппликаций для экстерьера; разработка новых процессов внешней отделки; испытания и внедрение экологически чистых и более прочных отделочных материалов и герметиков для наружных и внутренних работ; и физико-химические характеристики отделки и процессов отделки. Бэрд имеет степень бакалавра наук. по химии от Калифорнийского технологического института и М.С. в области химического машиностроения Массачусетского технологического института.
Высокотемпературные покрытия для защиты от окисления и эрозии жаропрочных углеродистых материалов в высокоскоростных потоках
[1]
Д. Г. Рохини, Р. Рама, Углерод-углеродные композиты — обзор.Defense Sci. J. 43 (4) (1993) 369-383.
DOI: 10.14429 / dsj.43.4291
[2] С.Чжан, Ю. Чжан, А. Ли и др., Углеродные композиты, в: X-S. Йи, С. Ду, Л. Чжан, (редакторы), Разработка композитных материалов, т. 2, Springer, Сингапур, 2018 г., стр. 531-617.
[3]
Дж. Э. Шиэн, К. Бескинг, Б.Дж.Салливан, Углерод-углеродные композиты, Annu. Rev. Mater. Sci. 24 (1994) 19-44.
DOI: 10.1146 / annurev.ms.24.080194.000315
[4] Н.С. Якобсон, Д. Исследования микроструктуры окисления Карри армированного углерода / углерода, Углерод. 44 (2006) 1142-1150.
DOI: 10.1016 / j.carbon.2005.11.013
[5]
В. И. Костиков, А. Варенков, Сверхвысокотемпературные композиционные материалы, Интермет Инжиниринг, Москва (2003).
[6] М.Бакос, Углерод-углеродные композиты: поведение к окислению и защита покрытий, J. Phys. IV Франция. 03 (C7) (1993) 1895–1903. DOI: https://doi.org/10.1051/jp4:19937303.
DOI: 10.1051 / jp4: 19937303
[7]
ИКС. Ян, Ч. Чжао-хуэй, Ч. Фэн, Высокотемпературные защитные покрытия для композитов C / SiC, J. Asian Ceram. Soc. 2 (2014) 305-309.
[8] В.С. Терентьева, А.И. Еремина, А. Астапов и др. Влияние архитектуры и элементно-химического состава на структуру и свойства углеродсодержащих композиционных материалов // Композиты: механика, расчеты, приложения. 2 (3) (2011).
DOI: 10.1615 / compmechcomputapplintj.v2.i3.60
[9]
П. А. Троуэр, Дж.К. Богне, Г.К. Мэтью, Влияние окисления на структуру и прочность графита-I: материалы различной структуры, Углерод. 20 (6) (1982) 457-464.
DOI: 10.1016 / 0008-6223 (82)
-1[10] Дж.L. Wood, J.X. Zhao, R.C. Брэдт-младший Уокер, Влияние окисления на прочность графита на изгиб, Углерод. 19 (1) (1981) 61-62.
DOI: 10.1016 / 0008-6223 (81)
-6 [11]
К. Л. Лутра, Окисление углерод / углеродных композитов — Теоретический анализ. Углерод. 26 (1988) 217-224.
DOI: 10.1016 / 0008-6223 (88)
- -1
- Этилен-акриловый эластомер Vamac ® : термостойкость до 175 ° C с превосходной гибкостью, маслостойкостью и химической стойкостью. Vamac ® Ultra HT AEM обеспечивает постоянную термостойкость до 175 ° C с пиковыми температурами до 200 ° C.
- Kalrez ® детали из перфторэластомера: термостойкость до 327 ° ° C и стойкость к более чем 1800 химическим веществам, многие составы доступны для различных приложений.
- Сравнение размеров в паре с объективом F4 с максимальным разрешением 600 мм (эквивалент 35 мм)
1.Компания A: Полнокадровая зеркальная камера: прибл. 5500 г
2. OM-D E-M1X: прибл. 2300 г - Если рычаг мощности назначен рычагу Fn, рычаг Fn не может быть отключен.
- Гарантированная рабочая среда (согласно методам тестирования Olympus) — IPX1. Кабель дистанционного управления
- RM-CB2 не имеет защиты от брызг и пыли.
- 1 Рекомендуемые аксессуары
Anker PowerPort Speed 1 PD30 (быстрое зарядное устройство USB)
(Используйте кабель Anker USB PowerLine II USB-C и USB -C 3.1 (Gen2).
Anker PowerCore +26800 PD (портативное зарядное устройство)
(Используйте прилагаемый кабель.) - 2 Требуется выходной источник питания 9 В 3 А, 15 В 2 А или 15 В 3 А. Зарядка доступна только при выключенной камере. Эту функцию нельзя использовать при уровне заряда батареи 10% или меньше.
- Anker, PowerCore и PowerPort являются товарными знаками или зарегистрированными товарными знаками Anker Japan Co., Ltd. или ее дочерних компаний.
- Согласно условиям тестирования Olympus
- Фотографии предназначены только для иллюстративных целей.
[12] П.А. Троуэр, Дж. К. Богнет, Мэтью Г. К. Влияние окисления на структуру и прочность графита-I: материалы разного строения, Углерод. 20 (6) (1982) 465-471.
[13]
Дж. Родригес-Мирасол, П.А. Троуэр, Л. Радович, О стойкости к окислению углерод-углеродных композитов: важность волокнистой структуры для реакционной способности композита, Углерод. 33 (4) (1995) 545-554.
DOI: 10.1016 / 0008-6223 (94) 00180-8
[14] В.Ли, С. Донг, З. Ван и др., Изготовление и свойства 3-D композитов Cf / SiC – ZrC с использованием прекурсора ZrC и поликарбосилана, J. Am. Ceram. Soc. 95 (4) (2012) 1216-1219.
DOI: 10. 1111 / j.1551-2916.2012.05116.x
[15] ИКС.Ву, Л. Радович, Ингибирование каталитического окисления углерод / углеродных композитов легированием бором, Углерод. 43 (8) (2005) 1768-1777.
DOI: 10.1016 / j.carbon.2005.02.029
[16]
С. Э. Ю, М.К. Seo, B.S. Ким, С.Дж. Парк, Влияние MoO3 на механическое межфазное поведение и антиокисление композитов, армированных углеродными волокнами, J. Ind. Eng. Chem. 30 (2015) 29-32.
DOI: 10.1016 / j.jiec.2015.04.025
[17] В.Фен, З. Ван, Х. Дж. Чжоу и др., Анализ микроструктуры композитов Cf / SiC – ZrC как при производстве, так и при испытаниях в плазменной аэродинамической трубе, Ceram. Int. 40 (1) (2014) 1199-1204.
DOI: 10. 1016 / j.ceramint.2013.05.097
[18] Z.Х. Ян, Х. Чжан, Ю.С. Е., Получение композита Cf / HfC реактивной фильтрацией из расплава с использованием сплава на основе Hf, Mater. Sci. Форум. 816 (2015) 126-132.
DOI: 10.4028 / www.scientific.net / msf.816.126
[19]
Ф. Ульманн, К. Вильгельми, С. Шмидт-Виммер и др., Получение и характеристика ZrB2 и TaC, содержащих композитов Cf / SiC, посредством процесса полимерной инфильтрации-пиролиза, J. Eur. Ceram. Soc. 37 (5) (2017) 1955- (1960).
DOI: 10.1016 / j.jeurceramsoc.2016.12.048
[20]
С.Лабрукер, Х. Бланшар, Р. Пайлер и др., Повышение стойкости к окислению межфазной поверхности в композитах C / C. Часть I. Стойкость к окислению углеродных волокон с покрытием B – C, Si – B – C и Si – C, J. Eur. Ceram. Soc. 22 (7) (2002) 1001-1009.
DOI: 10.1016 / s0955-2219 (01) 00410-1
[21] Л.А. Ткаченко, А.Ю. Шаулов, А.А. Берлин, Защитные термостойкие покрытия из углеродных материалов, Неорг. Mater. 48 (3) (2012) 261-271.
[22]
К. -D. Ся, К.-Х. Лу, Й. Ян, Повышение стойкости к окислению углеродных волокон с помощью покрытий из оксикарбида кремния, New Carbon Mater. 30 (3) (2015) 236-243.
DOI: 10.1016 / s1872-5805 (15) 60188-3
[23] Ю.-З. Ян, Ж.-Л. Ян, Д.-Н. Фанг, Прогресс исследований теплозащитных материалов и конструкций гиперзвуковых аппаратов, Прил. Математика. Мех. 29 (1) (2008) 51-60.
DOI: 10. 1007 / s10483-008-0107-1
[24] В.Терентьева С., Богачкова О. Горячева, Патент РФ № 94008267/02. (1994).
[25]
Ю.Ян, К. Ли, Г. Лиу и др., Устойчивое к абляции композитное покрытие HfC-TaC-SiC для композитов C / C, нанесенных сверхзвуковым напылением плазмы в атмосфере, J. Ceram. Sci. Technol. 7 (4) (2016) 379-386.
[26] ГРАММ.В. Молев, Н. Мирзабекянц, Способы повышения стойкости углеродных материалов к окислению на воздухе при повышенных температурах, Химия твердого топлива. 1 (1998) 89-100.
[27]
ГРАММ. А. Кравецкий, В.В. Родионова, Ю.М. Дворянчиков, С.А.Колесников, Углеродокерамические композиционные материалы с защитными эрозионно-стойкими покрытиями, Новые огнеупоры. 2 (2007) 47-53.
DOI: 10.1007 / s11148-007-0027-3
[28] Э.Афанасьев, Ю.Ф. Климов, Р.И.Бурикова, Патент РФ No 2004104295/04. (2004).
[29]
С. Солнцев С.В., Исаева Н.В. Швагирева, Г.А. Соловьева, Патент РФ No 2000130627/03. (2000).
[30] В.И. Змий, С.Г. Руденький, В.В. Кунченко и др. Термостойкие комплексные покрытия на углеродных материалах, Пробл. В. Sci. Tech. 2 (90) (2014) 158-161.
[31]
В. С. Терентьева, А. Астапов, А. Еремин, Патент РФ No 2012146451/03. (2012).
[32] Б.Zou, Y. Hui, W. Huang et al., Защита от окисления углеродных композитов с помощью плазменного напыления покрытия ZrB2 – SiC – Si / Yb2SiO5 / LaMgAl11O19 во время термоциклирования, J. Eur. Ceram. Soc. 35 (2015) 2017- (2025).
DOI: 10.1016 / j.jeurceramsoc.2015.01.015
[33]
А. Н. Астапов, В. Терентьева, Обзор отечественных разработок в области защиты углеродистых материалов от газовой коррозии и эрозии в высокоскоростных потоках плазмы. J. Цветные металлы. 57 (2) (2016) 157-173.
DOI: 10.3103 / s1067821216020048
[34] Т.Л. Дами, О. П. Бахл, Б. Р. Awasthy, устойчивые к окислению углерод-углеродные композиты до 1700 ° C, углерод. 33 (1995) 479-490.
DOI: 10. 1016 / 0008-6223 (94) 00173-w
[35] Дж.-К. Юн, Г.-Х. Ким, К.-Т. Hong et al., Патент США 2006003567 A1. (2004).
[36] Р.Шао, патент США 2007172659 A1. (2006).
[37]
X. Ян, Л.Вей, У. Сонг, Поведение окислительных защитных покрытий для композитов PIP – C / SiC при 1500 ° C, Ceram. Int. 38 (2012) 9-13.
DOI: 10.1016 / j.ceramint.2011.06.063
[38] Т.Л. Дхами, О.П. Бахл, Проблемы в технологиях углеродных / углеродных композитов, Carbon Sci. 6 (3) (2005) 148-157.
[39]
W. Г. Фаренгольц, Диаграмма волатильности ZrB2, J. Am. Ceram. Soc. 88 (2005) 3509-3512.
[40] ИКС.Джин, X. Фан, С. Лу, Т. Ван, Достижения в стойкости к окислению и абляции высоко- и сверхвысокотемпературной керамики, модифицированной или покрытой углеродно-углеродными композитами, J. Eur. Ceram. Soc. 38 (1) (2018) 1-28.
DOI: 10.1016 / j.jeurceramsoc.2017.08.013
[41]
W. К. Трипп, Х.С. Грэм, Термогравиметрическое исследование окисления ZrB2 в диапазоне температур от 800 до 1500 ° C, J. Electrochem. Soc. 118 (1971) 1195-1199.
[42] С.Р. Левин, Э.Дж. Опила, М. Halbig et al., Оценка сверхвысокотемпературной керамики для использования в авиационных двигателях, J. Eur. Ceram. Soc. 22 (2002) 2757-2767.
[43]
Z. Чен, X. Xiong, G.D. Li и др., Текстурная структура и поведение при абляции покрытия TaC на углерод / углеродных композитах, Appl. Серфинг. Sci. 257 (2010) 656-661.
DOI: 10.1016 / j.apsusc.2010.07.064
[44] М.М. Опека, И. Талми, Дж. Зайкоски, Выбор материалов на основе окисления для гиперзвуковых аэродинамических поверхностей 2000 ° C +: теоретические соображения и исторический опыт, J. Mater. Sci. 39 (2004) 5887-5904.
DOI: 10. 1023 / b: jmsc.0000041686.21788.77
[45] Р.Рао, В. Венугопал, Кинетика и механизм окисления ZrC, J. Alloys Compd. 206 (1994) 237-242.
[46]
ГРАММ.Д. Ли, Х. Сюн, Б.Ю. Хуанг, Ю.Л. Цзэн, Характеристика окисления и механизм окисления покрытия TaC, Чин. J. Цветные металлы. 17 (3) (2007) 360-367.
[47] С.Ф. Тан, К.Л. Ху, Дизайн, изготовление и свойства сверхвысокотемпературных керамических композитов, армированных углеродным волокном, для аэрокосмического применения: обзор, J. Mater. Sci. Technol. 33 (2017) 117–130.
[48]
Д. Чо, Б. Юн, Микроструктурная интерпретация влияния различных матриц на абляционные свойства композитов, армированных углеродным волокном, Compos. Sci. Технол, 61 (2) (2001) 271-280.
DOI: 10.1016 / s0266-3538 (00) 00212-8
[49] W.Г. Фаренгольц, Г. Хильмас, И. Талми, Дж. Зайкоски, Огнеупорные дибориды циркония и гафния, J. Am. Ceram. Soc. 90 (5) (2007) 1347-1364.
DOI: 10. 1111 / j.1551-2916.2007.01583.x
[50] А.Л. Чемберлен, В. Г. Фаренгольц, Г. Э. Хилмас, Д.Т. Эллерби, Высокопрочная керамика на основе диборида циркония, J. Am. Ceram. Soc. 87 (2004) 1170-1172.
DOI: 10.1111 / j.1551-2916.2004.01170.x
[51]
Ф. Монтеверде, А. Беллози, С. Гвиччарди, Обработка и свойства композитов на основе диборида циркония, J. Eur. Ceram. Soc. 22 (2002) 279-288.
DOI: 10.1016 / s0955-2219 (01) 00284-9
[52] С.Ран, С.Г. Хуанг, О. Ван дер Бист, Дж. Влейгельс, Высокопрочная керамика на основе ZrB2, полученная реактивным импульсным электрическим током спекания порошков ZrB2 – Zrh3, J. Eur. Ceram. Soc. 32 (2012) 2537-2543.
DOI: 10. 1016 / j.jeurceramsoc.2012.02.035
[53] П.Франке, Д. Нойшютц (ред.), Двоичные системы. Часть 2: Элементы и бинарные системы от B — C до Cr — Zr. Springer, Берлин, Гейдельберг (2004).
DOI: 10.1007 / b76783
[54] П.Соколов, В.А. Муханов, Т. Шово, В.Л. Соложенко, О плавлении карбида кремния под давлением, Журнал сверхтвердых материалов. 5 (2012) 76-78.
DOI: 10.3103 / s1063457612050097
[55] Ю.Л. Ван, Х. Сюн, X.J. Чжао и др., Структурная эволюция и механизм абляции покрытия из карбида гафния на композите C / C в среде кислородно-ацетиленовой горелки, Corros. Sci. 61 (2012) 156-161.
DOI: 10.1016 / j.corsci.2012.04.033
[56] С.Л. Ван, К.З. Ли, Х.Дж. Ли, Ю.Л. Чжан, Микроструктура и сопротивление абляции наноструктурированного покрытия ZrC для углерод / углеродных композитов, Матер. Lett. 107 (2013) 99-102.
[57] ЧАС.Ву, HJ. Ли, К.-Г. Fu et al., Микроструктуры и сопротивление абляции ZrC-покрытия для покрытых SiC углерод / углеродных композитов, полученных сверхзвуковым плазменным напылением, J. Therm. Спрей Технол. 20 (2011) 1286-1291.
DOI: 10.1007 / s11666-011-9676-3
[58] Ю.Цзэн, Д. Ван, X. Xiong и др., Устойчивый к абляции карбид Zr0.8Ti0.2C0.74B0.26 для окислительных сред до 3000 ° C, Nat. Commun. 8 (15836) (2017) 1-9.
[59] ИКС.Xiong, Y.L. Ван, Г.Д. Ли и др. Защитное покрытие HfC / ZrC для защиты от абляции углерод / углеродных композитов, Corros. Sci. 77 (2013) 25-30.
DOI: 10.1016 / j.corsci.2013.06.042
[60] Ю.Л. Ван, Х. Сюн, Г.Д. Ли и др., Свойства получения и абляции покрытия Hf (Ta) C соосаждения для углерод / углеродных композитов, Corros. Sci. 66 (2013) 177-182.
DOI: 10.1016 / j.corsci.2012.09.016
[61] Э.Л. Кортрайт, Дж. Т. Пратер, Г. Холкомб и др., Окисление карбида гафния и карбида гафния с добавками тантала и празеодима, Oxid. Встретились. 36 (1991) 423-437.
DOI: 10.1007 / bf01151590
[62] А.A. Appen. Термостойкие неорганические покрытия, Химия, Ленинград (1976).
[63] ГРАММ.Бобров, А.А. Ильин, Применение неорганических покрытий (теория, технология, оборудование), Интермет Инжиниринг, Москва (2004).
[64] В.С. Терентьева, А. Астапов, А. Еремин, Анализ перспективных антиоксидантных покрытий для высокотемпературных углеродсодержащих композиционных материалов (обзор) // Коррозия: материалы, защита. 1 (2014) 30-42.
Термостойкие эластомеры | Полимеры DuPont Performance
Термостойкие эластомеры, испытанные на практике
Термостойкие эластомеры DuPont подтверждены обширными испытаниями, экспертами по применению и реальными характеристиками.
В автомобильной промышленности меньшие по размеру и более экономичные автомобильные двигатели делают вещи более горячими под капотом. В производстве энергии глобальный спрос на надежные источники энергии увеличивает интервалы технического обслуживания.
Всякий раз, когда возникает проблема поддержания высоких характеристик при высоких температурах и агрессивных химикатах, термостойкие эластомеры DuPont предлагают полный ассортимент экономичных вариантов.
Указание правильного материала
Часто тепло — не единственная проблема для приложения.Выбор термостойкого эластомера, который также обладает требуемым сочетанием гибкости, прочности и химической стойкости, может стать ключом к успеху.
Вот краткий обзор термостойких эластомеров DuPont:
Автоиндустрия Фокус: DuPont ™ Vamac ®
Этилен-акриловый эластомер Vamac ® (AEM) является наиболее широко применяемым эластомером в автомобильной промышленности. Это предпочтительный материал для шлангов, амортизаторов, уплотнений, башмаков и прокладок благодаря сочетанию долговечной гибкости, устойчивости к нагреванию и автомобильным смазкам.
Доступно множество марок Vamac ® , обеспечивающих точные характеристики, необходимые для конкретных приложений.
Потребители требуют новых инноваций. Vamac ® Ultra HT этилен-акриловый эластомер (AEM) обеспечивает постоянную термостойкость до 180 ° C с пиками до 200 ° C и улучшенные механические свойства. Разработано для работы со шлангами и воздуховодами автомобильных турбонагнетателей, когда среда в двигателе становится более горячей и с которой становится труднее обращаться. Обладая оптимизированной структурой и химическим составом, новое поколение Vamac ® обеспечивает значительные улучшения, особенно при наличии моторных и трансмиссионных масел или кислот в системах рециркуляции выхлопных газов и закрытой вентиляции картера.
Лучшие в своем классе эластомерные уплотнения: DuPont ™ Kalrez ®
Для наиболее сложных случаев герметизации лучше всего подходят детали из перфторэластомера (FFKM) DuPont ™ Kalrez ® . Проверенные в самых агрессивных применениях, его улучшенные свойства помогают поддерживать целостность уплотнения и помогают снизить затраты на обслуживание и эксплуатацию. Детали и уплотнения Kalrez ® выдерживают более 1800 различных химикатов, обеспечивая при этом высокотемпературную стабильность ПТФЭ (327 ° C).
Детали Kalrez ® разработаны с учетом свойств, позволяющих удовлетворить особые требования к применению во многих отраслях промышленности. Детали Kalrez ® , от смазочных материалов для реактивных двигателей и ракетного топлива до скважинных нефтяных сред и вакуумных уплотнений, продемонстрировали свою способность работать в самых сложных условиях. Детали Kalrez ® доступны во многих составах в виде стандартных уплотнительных колец или могут быть специально разработаны для уникальной посадки. Производственные мощности Kalrez ® зарегистрированы в соответствии со стандартом ISO 9000, а запасные части полностью отслеживаются.
* Подразделение фторэластомера Viton ® теперь является частью компании Chemours. Посетите Chemours.com для получения дополнительной информации.
* Для получения информации о неопрене обращайтесь на http://www.denka.co.jp/eng/organic/product/
Поставка AUTO MANAS 23. Герметик термостойкий RTV герметик термостойкий уплотнитель-
Описание продукта:
Герметик готовится с применением передовых технологий производства.Однокомпонентный, высокая прочность уплотнения, хорошая термостойкость, прочная атмосферостойкость, не провисающее покрытие поверхности, хорошая маслостойкость, отсутствие коррозии, отсутствие раздражающего газа, отсутствие усадки отверждающих веществ, легкое удаление коллоидов, нетоксичность защиты окружающей среды. Он не ограничен размером и формой связывающей поверхности. Он может заменить все виды резиновых прокладок, асбестовых прокладок, пробковых прокладок и бумажных прокладок, которые могут эффективно предотвращать утечку воды, масла и газа, а также имеют хорошее уплотнение и эффект утечки.
Область применения:
Этот клей может заменить все виды резиновых прокладок, асбестовых прокладок, пробковых прокладок и бумажных прокладок, что может эффективно предотвратить утечку воды, масла и газа и имеет хороший герметизирующий эффект. Он подходит для плоской герметизации машин, автомобилей, мотоциклов, тракторов, судовых двигателей, коробок передач, масляных баков, электромеханического оборудования, электроприборов, инструментов, электронного и химического оборудования, а также для герметизации стыков труб и поверхностей стыков крышки.
Инструкции:
1. Очистите поверхность клея водой, пылью, маслом, пятнами ржавчины и другими загрязнениями;
2. Проколите патрубок трубы колпачком, равномерно нанесите гель от внешнего края к внутреннему краю толщиной около 1,6-3,2 мм, с хорошей герметизацией.3. Примерно через 10-20 минут после нанесения клея, когда поверхность пленки вступит в реакцию, выровняйте две уплотнительные поверхности и прижмите их, чтобы затянуть;
4, при комнатной температуре 25 ℃ размещен через 10 или 24 часа после использования, эффективность герметизации очень высока;
5.Для необработанного геля накройте крышку тюбика, вымойте руки чистой водой и очистите инструменты. Примечания: 1. Обеспечьте вентиляцию рабочего места, чтобы избежать контакта с детьми;
2. Во время работы надевайте кожаные перчатки. При прикосновении к коже или глазам немедленно промойте их водой или обратитесь за медицинской помощью;
3. Хранить в прохладном, сухом и проветриваемом месте, беречь от высоких температур;
4. Перед использованием партиями пользователь должен сначала провести эксперимент, чтобы не повлиять на эффект склеивания из-за неправильной эксплуатации.
Надежность E-M1X | OM-D | Olympus
E-M1X был разработан для обеспечения производительности и функциональности, чтобы удовлетворить потребности занятых фотографов, с упором на создание стабильного захвата при горизонтальном или вертикальном положении, а также элементы управления, которые позволяют фотографу сосредоточиться во время съемки с видоискателем.
Встроенная вертикальная ручка
Встроенная вертикальная ручка обеспечивает такой же захват и позволяет контролировать положение камеры в вертикальном или горизонтальном положении.Разработан с глубокими упорами для пальцев как в вертикальном, так и в горизонтальном положении, чтобы фотографы могли снимать стабильно и в течение длительного времени.
Непревзойденная портативность
Непревзойденная портативность системы Micro Four Thirds действительно проявляется при переноске камеры с прикрепленным телеобъективом. Конструкция системы позволяет снимать с рук супертелеобъектив и удерживать камеру в течение длительного периода времени.
Оптимальные элементы управления для съемки в видоискателе
Эргономичное расположение: одна функция для каждой кнопки
Эргономичная компоновка с единственной функцией для каждой кнопки позволяет фотографам управлять элементами управления, сосредоточившись на съемке через видоискатель. Высота и форма каждой отдельной кнопки варьируется во избежание неправильного использования.
Настраиваемый C-LOCK
E-M1X включает настраиваемую блокировку, которую можно активировать для блокировки работы кнопок и рычагов. Это дополнение к стандартному LOCK для управления камерой в вертикальном положении.
Видоискатель с большим увеличением и скоростью
Новый видоискатель с усовершенствованной оптической конструкцией с четырехэлементной конфигурацией асферических линз и линз с высоким показателем преломления создает ведущий видоискатель в отрасли.Видоискатель E-M1X имеет высокое 0,83-кратное увеличение (эквивалент 35 мм) с четким отображением изображения от края до края без искажений. Работая с максимальной частотой кадров 120 кадров в секунду, высокоскоростной электронный видоискатель с прогрессивной разверткой сводит к минимуму задержку отображения до 0,005 секунды для плавного отображения быстро движущихся объектов. Два высокопроизводительных процессора изображений TruePic VIII более плавно воспроизводят темные тона на дисплее. Компоновку видоискателя можно настроить в соответствии с вашими предпочтениями и при увеличении 0.Было выбрано 74x (эквивалент 35 мм), он оптимизирован так, чтобы съемочная информация не накладывалась на объект; чтобы ваш фокус оставался на съемке движущихся объектов.
Конструкция с повышенной пыленепроницаемостью, брызгозащищенностью и морозостойкостью
Защита от атмосферных воздействий E-M1X превосходит традиционный стандарт защиты от атмосферных воздействий IPX1, обеспечивая спокойствие и надежность в суровых условиях. Эта конструкция позволяет снимать без погодных условий и без дождя.Защита от пыли, брызг и замерзания сохраняется даже при подключении кабелей к клеммам удаленного кабеля, микрофона и наушников. Резиновое уплотнение, используемое в камерах Olympus Tough, используется для герметизации каждой крышки камеры, включая слот для SD-карты.
Система удаления пыли
Компания Olympus первой изобрела систему уменьшения пыли и имеет долгую историю надежности.Сверхзвуковой волновой фильтр (SSWF) вибрирует со скоростью более 30 000 раз в секунду, мгновенно удаляя грязь и пыль. E-M1X имеет новое покрытие сенсора, чтобы уменьшить вероятность попадания пыли на фотографии до 10 или предыдущих моделей, что позволяет менять линзы даже в тяжелых условиях.
Конструкция отвода тепла
1. Тепловая трубкаКонструкция отвода тепла в E-M1X достигается за счет использования тепловой трубки для отвода тепла, выделяемого во время съемки.В частности, эта функция ограничивает проблемы, вызванные повышением температуры при непрерывной съемке или съемке видео в жаркую погоду.
Аккумулятор большой емкости
В E-M1X можно установить две литий-ионные аккумуляторные батареи BLH-1, такие же, как и в OM-D E-M1 Mark II. Батарейки можно легко заменить, даже если камера установлена на монопод или штатив. Кроме того, E-M1X также совместим со стандартом USB PD [1] [2] для максимальной мощности 100 Вт.Две батареи можно зарядить всего за два часа.
Высокопрочная створка
Прочная заслонка рассчитана на 400 000 операций [*] .
Новый пользовательский интерфейс
Новый пользовательский интерфейс был разработан на основе отзывов фотографов и включает новую функцию «Мое меню».Эта новая функция позволяет фотографам создавать собственное специальное меню для прямого доступа к 35 элементам на 5 вкладках, по 7 элементов на каждой вкладке. Новый пользовательский интерфейс также позволяет быстро выбирать несколько изображений, поворачивая диск при одновременном нажатии кнопки фильма для стирания или порядка обмена.