Композитный клей: Клеи — Композитные материалы R-G-COMPOSITES.RU
Методы соединения и крепления композитных панелей
Склеивание Алюминиевые поверхности композитов могут склеиваться любыми клеями для металлов или соответствующими универсальными. При склеивании композитов с другими материалами необходимо использовать высокоэластичные клеи (например, однокомпонентные на полиуретановой основе). При склеивании больших поверхностей материалов различных химических групп рекомендуется предварительное тестирование для уточнения реакции поверхностей, так как различия в коэффициентах линейного растяжения могут спровоцировать нежелательные деформации.
В случае, если в качестве наполнителя композита используется полиэтилен, склеивание панелей встык практически неосуществимо, что обусловлено низкой поверхностной энергией данного полимера. Можно воспользоваться современными специальными клеевыми составами для полиэтилена и полипропилена, но наилучшим решением все-таки будут другие методы соединения – сварка или механическое крепление.
При отсутствии высоких требований к прочности изделия или при фиксации деталей небольших размеров можно воспользоваться двусторонними клеящими лентами с максимальным уровнем адгезии. Разъемные соединения удобно осуществлять с помощью таких монтажных средств, как самоклеящиеся «липучки» и «застежки».
Сварка
Сварку композитных материалов можно производить наиболее популярным методом для соединения полимерных материалов – сваркой горячим воздухом (t = 260 – 270 °С) с применением сварочной проволоки (припоя). При помощи сварочных аппаратов внутренний слой композита и сварочная проволока нагреваются и прочно соединяются. Решающими факторами качественного соединения являются: необходимая подготовка свариваемых поверхностей, качество сварочной проволоки, горячий воздух без посторонних примесей, необходимые температура и давление прижима, скорость сварочного процесса.
Для достижения оптимального качества соединения перед работой свариваемые торцы композита должны быть скошены. Угол скоса зависит от профиля и ширины проволоки. После того как кромки подготовлены таким образом, сварку необходимо произвести в течение 24 часов. Это требование обусловлено возможной реакцией наполнителя с кислородом, которая может затруднить сварку или снизить прочностные качества сварного шва.
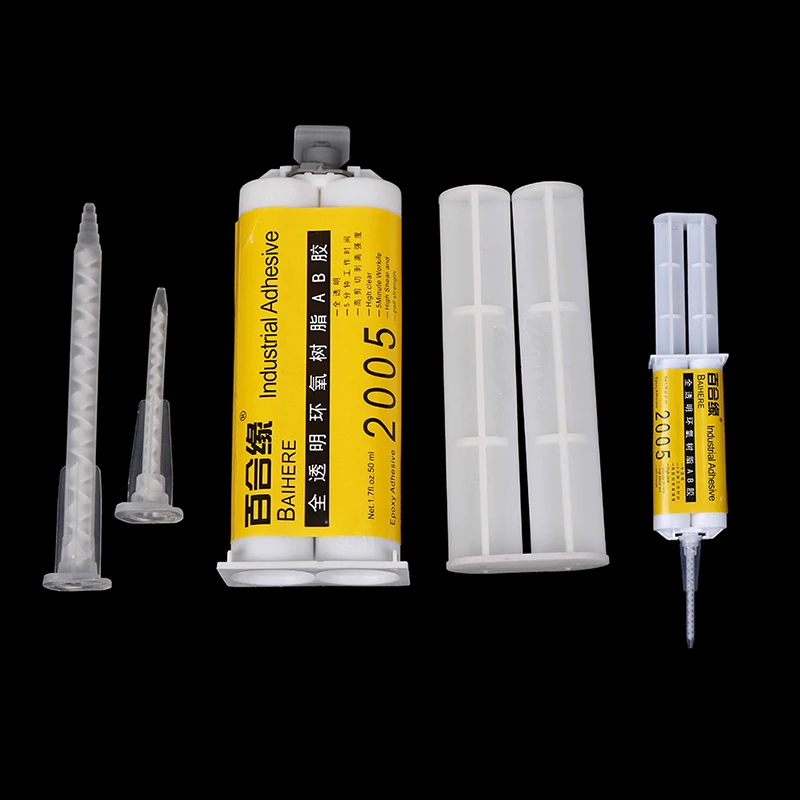
Для соединения композитных панелей с полиэтиленовым наполнителем рекомендуется использовать мягкий полиэтиленовый припой, поверхность которого перед сваркой зашкуривается.
После сварки на поверхности соединения образуется сварной наплыв. Его удаление производится с помощью фасонного ножа после полного остывания шва. Лезвие ножа при этой операции необходимо держать с максимальным наклоном к поверхности сваренных деталей.
Примечание: существуют композиты, внутренний слой которых представляет собой не сплошной наполнитель, а профилированный полимерный (ПЭ) тонкий лист с воздушными продольными секциями. Такие материалы из-за незначительной контактной поверхности не могут подвергаться склеиванию встык и сварке.
Механическое соединение
Методы механического соединения композитов в легких конструкциях аналогичны методам работы с пластиками и листовыми металлами.
При использовании панелей в строительных целях и при изготовлении крупногабаритных рекламных конструкций к вопросу крепления необходимо подходить со всей ответственностью. В этих случаях от прочности соединения зависит не только внешний вид изделия, но и человеческая и имущественная безопасность. Для композитных панелей были разработаны специальные самозавинчивающиеся шурупы. Наконечник шурупа выполнен в виде сверла из закаленной стали. Именно на этой части элемента крепления лежат основные нагрузки по просверливанию отверстия не только в композите, но и в материале несущей конструкции, например в стальной обрешетке.

Шурупы для композитных материалов имеют следующие особенности:
— диаметр части шурупа, закрепляемой в несущей основе меньше диаметра подшайбовой части. Это необходимо для надежной фиксации шурупа в тонком слое алюминия панели.
— диаметры резьбы также отличаются – срединная резьба меньше по диаметру, чем подшляпковая. Этим обеспечивается дополнительное уплотнение.

Композиты, как и прочие материалы, под действием перепадов температур расширяются и сжимаются. При установке панелей на улице учет этого фактора особенно важен. Коэффициент линейного расширения композита основывается на свойствах алюминиевого покрытия и имеет значения 0,023 – 0,025 мм/м°С в зависимости от производителя. Во избежание необратимых деформаций необходимо правильно рассчитать диаметр монтажных отверстий и зазоров в профилях в соответствии с возможными максимальными и минимальными эксплуатационными температурами. Форма профиля должна обеспечивать надежную фиксацию панели в любых температурных условиях и при максимальных механических нагрузках (ветровых, вибрационных и т. п.).
Клепание
Композитные панели можно соединять заклепками, подходящими для алюминия. При эксплуатации конструкции на улице или во влажных помещениях рекомендуется использовать глухие заклепки из алюминия или нержавеющей стали и оставлять зазор, необходимый для свободного движения листа при расширении.
Винтовое соединение
При монтаже композитных панелей внутри помещений можно использовать металлические или деревянные винты с головками самых разнообразных форм. Для создания аккуратного соединения и во избежание повышенных локальных внутренних напряжений при использовании винтов с потайной головкой предварительно необходимо расширить отверстие зенкерным инструментом. При постоянной температуре в помещении оставлять зазоры для свободного движения материала нет необходимости.

Профили
Прочные соединения при изготовлении рекламных конструкций можно создавать с помощью самых разнообразных профильных систем. Внутри помещений широко используются пластиковые и алюминиевые П-, U–, Г- и Н-образные профили, а также разборные рамки с защелкивающимся механизмом.
Уличные условия требуют более внимательного подхода. Панель в профиль должна устанавливаться с зазором, обеспечивающим свободное движение материала. При крупных габаритах конструкций для повышения их устойчивости к различного рода нагрузкам и в целях безопасности желательно профиль зафиксировать в нескольких точках с помощью винтов и его полочки прижать к поверхности панели (если толщина и материал профиля позволяют это сделать).
Для монтажа вентилируемых фасадов на российском рынке существует несколько специализированных профильных систем.
Внимание! При монтаже конструкций, состоящих из нескольких (или многочисленных) одинаковых панелей, необходимо каждую из них устанавливать в одном и том же направлении. Это легко будет сделать, если предварительно не удалять защитную пленку с маркировкой. Пренебрежение этим правилом может привести к тому, что под разными углами обзора и при яркой освещенности одинаковые элементы конструкции будут смотреться по-разному.
Кластер «Композиты без границ»
Клеи и клеевые пленки обеспечивают надежное склеивание соединений из различных материалов, в т.ч. для склеивания композитных сотовых конструкций с обшивкой, для склейки металлических и неметаллических деталей. Пленочные и вспенивающиеся клеи компании «ИТЕКМА» оптимально подходят для заполнения сотовых конструкций при изготовлении сэндвич-панелей.
Двухкомпонентный тиксотропный клей АТ-44 – двухкомпонентный тиксотропный клей, обеспечивающий надежное склеивание соединений из различных материалов. Конструкции, склеенные клеем марки АТ-44, можно эксплуатировать при температуре от минус 60 °С до плюс 85 °С. Клей доступен в тубах.
Преимущества:
- Тиксотропный клей, пригодный для заполнения щелей любой толщины
- Отверждение при комнатной температуре
- Хорошие механические свойства
- Не нужно дозировать компоненты: при выдавливании из тубы поступает необходимое количество каждого компонента
Однокомпонентный пленочный клей КП-120 предназначен для склеивания деталей и сотовых конструкций с температурой применения изделий до 180°С. Клей КП-120 подходит для склейки металлических и неметаллических деталей, для склеивания сотовых конструкций с обшивкой. Температура эксплуатации изделий лежит в температурном интервале от -60 до +180°С.

Преимущества:
- Высокая прочность и жесткость
- Хорошая липкость.
Однокомпонентный пленочный бисмалеимидный клей КПБ-250 предназначен для склейки металлических и неметаллических деталей, для склеивания сотовых конструкций с обшивкой. Температура отверждения клея составляет 180°С, постотверждения 230°С. Температура эксплуатации изделий достигает 250°С.
Преимущества:
- Высокая прочность и жесткость;
- Хорошая липкость;
- Высокая температура эксплуатации.
Пленочный вспенивающийся бисмалеимидный клей КВБ-250 предназначен для склеивания сотовых конструкций. Температурный интервал эксплуатации клеевых соединений от -60 °С до +250 °С.
Технические характеристики:
- Предел прочности при отрыве клеевого соединения сотового заполнителя из фольги AMг-2H толщиной 0,03–0,04 мм со стороной ячейки 2,5 мм с обшивкой при температуре 25°С не менее 2 МПа
- Предел прочности при отрыве клеевого соединения сотового заполнителя из фольги AMг-2H толщиной 0,03–0,04 мм со стороной ячейки 2,5 мм с обшивкой при температуре 250°С не менее 2 МПа
Преимущества:
- Вспенивается при отверждении и заполняет полости;
- Высокая температура эксплуатации
Области применения:
- Склеивание панелей сотового заполнителя между собой и с элементами силового каркаса, а также для усиления сотового заполнителя в зонах передачи сосредоточенных нагрузок при изготовлении трехслойных сотовых конструкций.
Однокомпонентная синтактная бисмалеимидная паста ПБ-250 предназначена для получения жесткой синтактной пены в процессе отверждения. Подходит в качестве заполнителя для сотовых конструкций.
Преимущества:
- Низкая плотность
- Высокая прочность и жесткость
- Длительный срок хранения
Области применения:
- Формирование локальных усилений в трехслойных сотовых конструкциях.
Полный перечень продукции представлен на сайте компании — ссылка на каталог клеев и клеевых пленок
Производитель – ООО «ИТЕКМА»
debang jiarun блок композитный клей a / b клей
изделие: debang jiarun блок композитный клей a / b клей
описание и спецификация:
пакет |
металлическая упаковка / 25 кг / баррель |
функции |
1, большая сила сцепления 2, высокая вязкость 3, хорошая стабильность 1, используется для усиления каменного блока и соединения задней стороны. 2, в процессе обработки камня, потери, разрушения краев, трещины и повреждения могут произойти из-за резкой вибрации пилы, текстуры камня, неправильного направления резания. |
заявление |
1, смешайте клей со скоростью 3: 1, клей следует использовать сразу после приготовления. 2, для светло-мраморного мрамора, как белый мраморный гвоздь, который имеет трещины, трещины, затычки, ослабление проблем |
меры предосторожности |
1, хранится в прохладных местах без прямого солнечного света и плотно закрывается после использования. 2, перчатки, дыхательную маску и защитные очки должны быть подготовлены на рабочем месте. |
подробное изображение
блочная инъекция клея:
Алмазный камень с клеем имеет очень хорошее проникновение на камни блоков.
упаковка и доставка
у dialead есть два разных пакета для доставки клея.
для металлического бочки он может упаковать 200 кг на баррель.
для пластиковой бочки он может упаковывать 1000 кг на баррель.
оплата и доставка
внутренние клиенты:
эпоксидный клей debang jiarun stone может занимать около 80% доли внутреннего рынка. такие компании, как пятая галерея, камень dongsheng, камень sanxiang и т. д., сотрудничали с нами в течение многих лет.
тур по фабрике
с передовыми технологиями и оборудованием, представленными из Германии, dialead является крупнейшим производителем клея во всемирно известном каменном городе-shuitou. слябовый клей для светлого цвета и темного цветного камня, эпоксидная смола для ремонта ониксовой плиты, вакуумный клей для блочного и блочного композитного адгезивного клея, все это входит в нашу сферу деятельности. наши продукты хорошо приняты в Иране, Турции, Таиланде и т. д.
свяжитесь с нами
контактное лицо: mr diors
mob / whatsapp / wechat: 0086 18150515179
тел: 0086 595 22308536
факс: 0086 595 22308537
электронная почта: diors@dlstonetools.com
Что такое композитные материалы
Как и из чего строят яхты, какие технологии используют, что такое композит, чем отличается эпоксидная смола от полиэфирной, и как в этом задействован карбон? Мы решили разом ответить на все вопросы о технологии производства и написали большой лонгрид о том, как строят суда из стеклопластика — какие бывают материалы и методы. А в конце статьи подробно рассказали, что из этого используем мы на верфи Pacifico.
Что такое композит
Композиты — группа материалов, состоящих из нескольких компонентов, один из которых выполняет армирующую функцию, а второй связующую.Например, железобетон — это вид композита. В этом соединении железо выполняет армирующую функцию, а бетон — связующую. Композит, который используют в судостроении, называется стеклопластиком или углепластиком. Базово он состоит из стеклоткани или углеткани и смолы.
Особенность композитов, что готовый материал обладает гораздо большей прочностью и жесткостью, чем его ингредиенты по отдельности. А значит готовое изделие весит меньше. В судостроении важно сделать корпус максимально легким — чем он легче, тем более мореходная, быстрая и экономичная получается лодка. Поэтому композитные материалы как нельзя лучше подходят для этой задачи.
Из чего состоит композит
Композит, из которого строят суда, базово состоит из 4-х типов материалов:- связующее вещество (смола)
- армирующее вещество (ткань)
- средний слой (наполнитель для сэндвича: пена или сотовый материал)
- поверхностный слой (краска/гелькоут)
Если объяснять упрощенно, то композит производят следующим образом — ткань пропитывается жидкой смолой с отвердителем, высыхает и отвердевает.
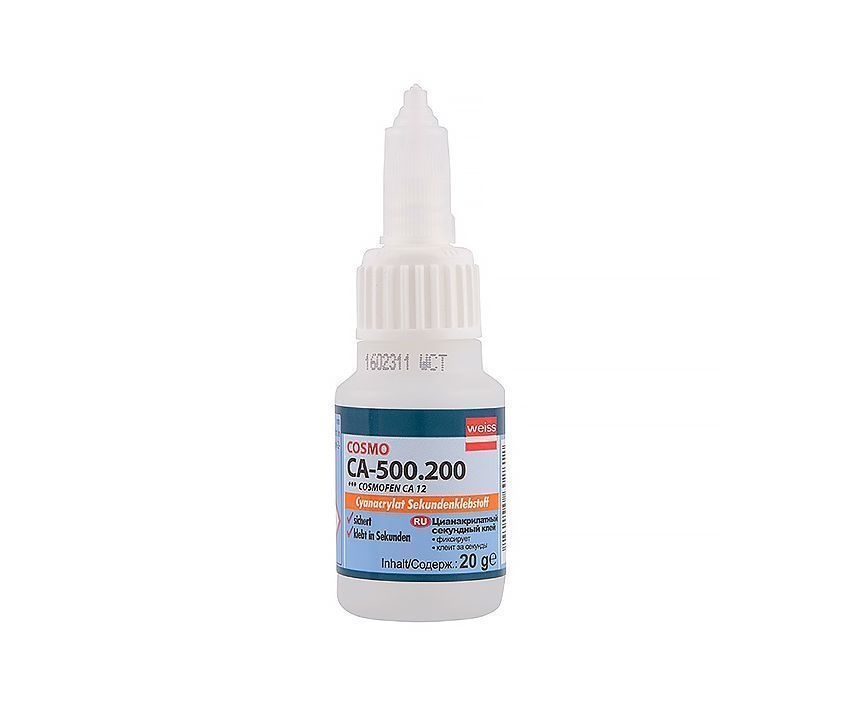
Для более сложных и больших конструкций, например, прогулочных катеров, используют композитный сэндвич. В композитном сэндвиче появляется средний слой — пена. Она закладывается между двумя армирующими слоями ткани, все вместе пропитывается смолой и в результате получается монолитный материал обладающий еще большей поверхностной прочностью, но при этом все еще достаточно легкий.
Разберем отдельно каждый тип материалов.
Смола
Смола — связующую вещество, которое пропитывает все слои композита и превращает их в готовую монолитную деталь. В судостроении используется 3 типа смолы:- эпоксидная
- эпоксивинилэфирная
- полиэфирная
Эпоксидная смола — самая прочная и дорогая. За счет повышенной прочности для изготовления детали ее требуется меньше, чем полиэфирной смолы, а значит сама деталь получается легче.

Эпоксивинилэфирная — это соединение на основе эпоксидной смолы. В отличие от эпоксидной смолы оно уже содержит стирол, но в меньших количествах, чем полиэфирная смола. По цене и прочности это промежуточный вариант между эпоксидной и полиэфирной смолой.
Полиэфирная — дешевая и наименее прочная, содержит стирол. Изделия из нее получается тяжелее и со временем начинают впитывать воду. Полиэфирная смола более хрупкая, поэтому корпуса из нее со временем нуждаются в ремонте. Корпус из полиэфирной смолы в среднем служит до 20 лет.
Ткань
Ткань в судостроении выполняет роль армирующего вещества — с помощью нее изделию задается форма, она берет на себя нагрузку на скручивание. Ткань дает конструкции прочность на растяжение или сжатие.В судостроении используется три типа ткани:
- стекломат
- стеклоткань
- углеткань
Стекломат — рубленные спресованные волокна стекловолокна.

Стеклоткань — стекловолокна, которые сплетено таким образом, что у ткани есть конкретное направление. Виды плетения бывают разными и от них зависит под каким углом ткань абсолютно устойчива на растяжение. Грамотный проект яхты учитывает особенности направления ткани и четко регламентирует какой тип плетения надо использовать на конкретных участках конструкции. Благодаря сочетанию разных типов плетения получаются максимально прочные детали, устойчивые к любым видам нагрузок.
Углеткань — тоже самое, что стеклоткань, только из углеволокна. У нее тоже есть разные типы плетения и направления. Углеволокно примерно в 2 раза прочнее, чем стекловолокно — точное соотношение зависит от типа плетения. Но стоит в 20 раз дороже.
Если упрощенно, то благодаря повышенной прочности на одну и ту же деталь углеволокна уходит в 2 раза меньше, чем стекловолокна. В результате деталь из углеволокна получается примерно в 2 раза легче. Готовый материал изделия из углепластика называется карбон. Полностью из карбона строят самые дорогие и быстрые гоночные яхты в мире.
Средний слой
Средний слой нужен, чтобы добавить расстояния между несколькими армирующими слоями ткани, и тем самым повысить поверхностную плотность изделия. Дело в том, что сама по себе ткань дает нужную прочность только на скручивание или сжатие, но не дает необходимой поверхностной прочности — деталь получается слишком тонкой.В теории, увеличить толщину и соответственно поверхностную прочность можно просто наложив больше слоев стеклоткани, но тогда мы получим слишком большой вес, и при этом избыточную прочность к скручивающим нагрузкам.
Поэтому, чтобы соблюсти баланс между весом, поверхностной прочностью и устойчивостью к скручиванию, используют принцип сэндвича и прокладывают армирующие слои легким наполнителем. Чаще всего в производстве используют следующие типы наполнителя:
ПХВ — пенополивинилхлорид.

Coremat — состав, сделанный на основе тех же соединений, что и стекловолокно. Стоит значительно дешевле, чем ПХВ, но итоговое изделие получается тяжелее. По своему принципу он похож на стекломат, но весит меньше и впитывает меньше смолы. Поэтому если сравнивать, что лучше — просто накатать больше ткани или использовать coremat, выгоднее выбрать coremat.
Если нужен максимально легкий и быстрый корпус, лучше использовать ПХВ. Если нужно получить дешевую, но тихоходную лодку — выгоднее использовать coremat.
Поверхностный слой
Поверхностный слой — внешний слой корпуса, который дает цвет и защищает от поверхностных повреждений. Обычно его делают из гелькоута или полиуретановой краски.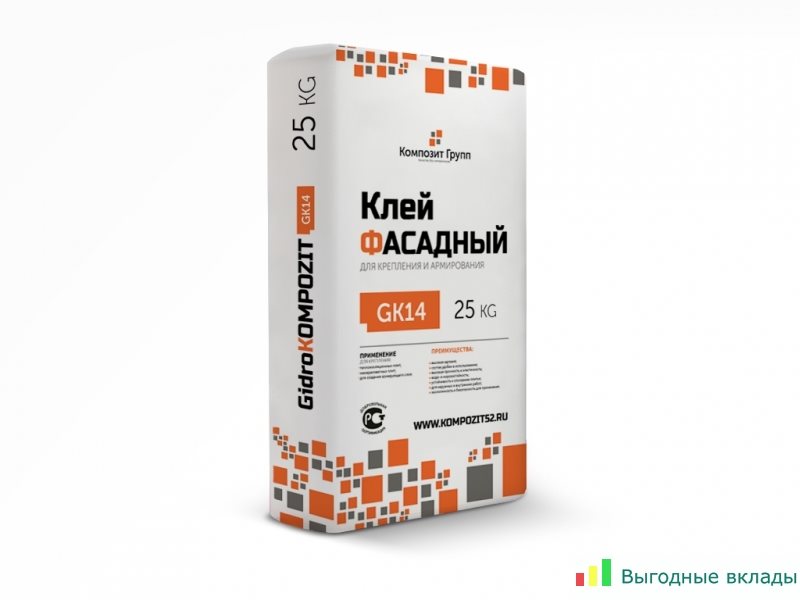
Гелькоут — соединение по составу очень похожее на смолу, оно тоже может быть на полиэфирной, эпоксидной или эпоксивинилэфирной основе. Если упрощенно, это густая смола с конкретным цветом. Гелькоут достаточно устойчив к поверхностным воздействиям. Закладывается в матрицу, как один из слоев монолитного корпуса.
Полиуретановая краска — тип краски, который хорошо защищает от внешних воздействий. Краска предлагает большой выбор цветов и стоит дороже. Наносится сверху на готовое изделие.
Как строят корпус
Чтобы построить яхту из композита, нужна матрица — форма, в которую будут выкладываться слои ткани и смолы, чтобы в итоге получился корпус. Можно сделать одну матрицу для всей нижней части корпуса — тогда он будет полностью монолитный. Можно сделать несколько маленьких матриц и производить детали по отдельности, а потом вручную собирать их в одно целое — такой метод используют при производстве больших корпусов длинной от 20 метров.В любом варианте укладывать слои и добиваться отвердевания можно разными способами. Вот основные методики изготовления готового корпуса:
- ручная формовка
- ручная формовка + вакуумное обжатие
- вакуумная инфузия
- запекание (prepeg)
Ручная формовка — самый трудоемкий и наименее технологичный метод. Рабочие вручную выкладывают ткань в матрицу и пропитывают ее смолой с помощью валика. Для упрощения работы есть специальный инструмент — чоппер. В него загружают смолу и рубленный стекломат, он соединяет внутри эти два компонента и распыляет их как бы из пистолета. Этот метод обычно используют для полиэфирной или эпоксивинилэфирной смолы. Вручную невозможно изготовить композитный сэндвич.
Минусы:
— итоговые изделия получаются тяжелыми из-за избытка смолы
— вручную трудно сделать весь корпус равномерным
Плюсы:
— дешево, просто, не требует специальных знаний и оборудования
Ручная формовка + вакуумное обжатие — в этом случае слои ткани и смолы также наносятся вручную, потом на них надевается специальный мешок, который откачивает лишний воздух и избыток смолы. Воздух — это пузырьки в смоле, которые так или иначе там появляются при методе ручной формовки. Эти пузырьки нарушают однородность корпуса и снижают его прочность. При откачке воздуха финальное изделие получается практически таким же прочным, как при методе вакуумной инфузии. Откачивать воздух можно после укладки каждого слоя по отдельности или после формовки всех слоев. Используется в основном в работе с эпоксидной смолой.
Композитный сэндвич можно изготовить только с помощью метода вакуумного обжатия или вакуумной инфузии.
Минусы:
— трудозатратно, долго и дорого
— нужно специальное оборудование
Плюсы:
— метод дает гарантированный результат, трудно что-то испортить в процессе
Вакуумная инфузия — в этом случае все сухие компоненты сэндвича (кроме смолы) выкладываются в форму-матрицу. Потом матрицу накрывают специальным вакуумным мешком, который откачивает весь воздух и сжимает компоненты. Затем вместо вакуума в деталь подается смола. Благодаря вакууму удается максимально точно контролировать количество смолы, а значит производить детали минимального веса. Метод требует высококвалифицированных специалистов и сложного оборудования. Если в производственном процессе допустить ошибку, есть риск испортить весь корпус и все задействованные материалы.
Минусы:
— нужно специальное оборудование
— требует строителей высокой квалификации
Плюсы:
— безупречное качество корпуса при соблюдении технологии
— при работе с большими объектами выгоднее с точки зрения трудозатрат
Запекание (prepeg) — самый высокотехнологичный метод, используется исключительно при работе с углеволокном. Для него необходим специально оборудованный цех-печь, где можно четко контролировать температуру и влажность.
Корпус яхты изготавливают из особого вида углеткани, сразу пропитанной смолой. Такая ткань перевозится в холодильниках и имеет короткий срок хранения. Из нее вручную формуют корпус яхты при температуре около 18 градусов и влажности не больше 60%. Потом конструкция обжимается вакуумным мешком и целиком запекается при температуре около 100 градусов.
Этот метод позволяет создать максимально легкий и прочный корпус. Например, вес яхты длиной 72 фута без оснастки, оборудования и киля получается около 2700 кг. Запекание используют в строительстве самых быстрых в мире гоночных яхт.
Плюсы:
— минимальный вес корпуса при нужной прочности
Минусы:
— очень дорогие материалы
— сложный и трудоемкий технологический процесс
Какие материалы и технологии используют на верфи Pacifico
Создание корпуса на верфи Pacifico Yachts состоит из нескольких этапов. Для каждой модели есть своя матрица и свои особенности производственного процесса в зависимости от технического проекта и итоговых характеристик яхты.Поэтому разбирать этапы будем на конкретном примере — строительстве корпуса Pacifico Voyager 99. Нижняя часть корпуса этого проекта полностью монолитна, поэтому формуется в одной большой матрице.
Этап 1. Работа начинается с подготовки и полировки внутренней поверхности матрицы.
Этап 2. После подготовительных работ, наносят внешний слой — гелькоут. Мы используем гелькоут на полиэфирной основе и наносим его пистолетом.
Этап 3. После этого вручную формуется «корка» из стекломата и эпоксивинилэфирной смолы. «Корка» нужна для того, чтобы основной слой корпуса из эпоксидной смолы крепко соединился с полиэфирным гелькоутом.
Этап 4. После того, как сформирована «корка», начинается формовка основного слоя — вручную укладывается сухая основа композитного сэндвича: стеклоткань + ПХВ + углеткань. Плетение и направление ткани выкладывается строго в соответствии с техническим проектом.
Этап 5. Корпус формуется методом вакуумной инфузии: конструкция обтягивается вакуумный мешком, из детали откачивается воздух, затем подается эпоксидная смола.
Этап 6. Смола отвердевает в течение 24 часов, затем корпус извлекается из матрицы и на нем начинаются технические работы.
В результате мы получаем эпоксидный корпус из стеклопластика, армированный углеволокном. Композитный сэндвич с ПВХ добавляет поверхностной прочности — корпус легко выдерживает удар кувалдой или столкновение с камнем, но все еще остается достаточно легким. Сочетание этих технологий и материалов позволяет нам строить быстрые и относительно экономичные катамараны, но при этом сохранять адекватную стоимость конечного продукта.
В этой статье мы разобрали большинство материалов и технологий производства. От них во многом зависят качество и технические характеристики готовой лодки: скорость, экономичность, долговечность и, конечно, цена. Но важно понимать, что в этом деле нет черного и белого, нет однозначно правильных или неправильных подходов к производству — каждый из них отвечает определенной задаче.
Чем химическая пломба отличается от световой | Программа для стоматологии Dental4Windows
Когда пациент обращается в государственную стоматологическую клинику с медицинским полисом с целью постановки пломбы, врач может предложить ему «доплатить за световую пломбу». Часто это вызывает непонимание у пациента и является источником конфликтных ситуаций. В чем здесь дело – попробуем разобраться в этой статье.
Сегодняшняя программа государственных гарантий в Москве и некоторых других регионах страны четко разделяет пломбы по классу используемого материала. Бесплатно устанавливают пломбы из цемента и композита химического отверждения, а пломбы из «светового» композита, при установке которых используют специальную лампу с синим светом, устанавливают за счет средств граждан, т.е. платно. В каких случаях можно ограничится бесплатной химической пломбой, а когда стоит доплатить за световую?
Чтобы понять, в чем разница между указанными технологиями, обратимся к истории развития стоматологических материалов для восстановления твердых тканей зубов. До середины прошлого века наиболее распространенным материалом для пломбирования зубов являлась амальгама – смесь серебра, ртути и других металлов. Такие металлические пломбы до сих пор широко ставят во многих зарубежных странах – в бюджетной стоматологии. В нашей стране от амальгамы отказались в 90-е годы в пользу композитов и цементов, которые на тот момент уже доказали свою эффективность благодаря развитию технологий.
Цементы
Так называемые стекло-иономерные цементы имеют широкое применение в современной стоматологии. Они представляют собой смесь порошка – мелкоизмельченного стекла и жидкости – органической кислоты или воды. Эти два компонента смешивают, полученной смесью заполняют кариозную полость, жидкость вступает в реакцию с окружающей средой, и пломба становится твердой.
Цементы имеют много положительных качеств:
- биосовместимость с тканями зуба
- выделение ионов фтора, что способствует профилактике вторичного кариеса
- отсутствие усадки материала
- соответствие цвету зубов
- быстрая постановка пломбы без использования адгезивов («клей» для пломбы)
- невысокая стоимость
Однако, несмотря на все положительные свойства, они имеют и свои существенные ограничения:
- адгезия цементов примерно в 10 раз ниже, чем у композитов, поэтому пломбы из цементов чаще выпадают;
- цементы недостаточно прочны, ими нельзя восстанавливать поверхности жевательных зубов;
- цементы имеют жидкую консистенцию, с их помощью нельзя восстановить отсутствующую часть зуба, ими можно только заполнять полости;
- цементы непрозрачны, их нельзя использовать для пломб на передних зубах, поскольку такие пломбы будут всегда заметны.
Цементы часто используют в качестве прокладочного материала под композиты при пломбировании больших полостей (биосовместимость, отсутствие усадки). Их широко используют в детской стоматологии на молочных зубах, а также для любых временных пломб. С помощью цементов можно ставить небольшие полноценные пломбы там, где отсутствуют жевательные нагрузки, например, в местах соприкосновения зубов при неглубоком кариесе.
Во всех остальных случаях пломбы из цемента являются именно «бюджетным» вариантом – быстро и бесплатно. О качестве вы можете судить сами, когда такая пломба выпадет или раскрошится.
Химические композиты
Изобретение техники кислотной протравки (Buonocore, 1965) и использование в качестве компонента пломбировочного материала мономер Bis-GMA (Bowen, 1962) положили начало «веку адгезивной стоматологии». Первые химические композиты появились в середине 60-х годов прошлого века. Тогда композитные материалы еще не обладали особо выдающимися качествами по сравнению с цементами и пластмассой, поэтому их применение было ограниченным. Тем не менее, композиты показали более высокую прочность и более высокие показатели адгезии к тканям зуба за счет использования адгезивов.
Широкое распространение композитных материалов началось на рубеже 1980-х годов, когда появились материалы светового отверждения. Преимущество световых материалов над композитами химического отверждения быстро стало очевидным, в связи с чем многие производители стоматологических материалов закрыли производство химических композитов, и полностью перешли на выпуск световых. Все научные разработки в области химических композитов были свернуты в пользу «света». Можно с уверенностью сказать, что световые композитные материалы пришли на смену композитам химического отверждения.
Сегодня химические композиты – тупиковая ветвь эволюции. Это материалы, разработанные в 70-е годы прошлого века. Большинство современных стоматологических клиник, как за рубежом, так и в России, химические композиты не используют.
Единственным достоинством химических композитов является их более низкая цена, благодаря чему они стали, помимо цементов, еще одним «бюджетным» материалом. Однако, существенные недостатки химических композитов дают повод для размышления, стоит ли «гробить» зуб постановкой химической пломбы или все-таки лучше найти средства и доплатить за световую.
Адгезия у химических композитов в несколько раз ниже, чем у световых, соответственно, пломбы будут выпадать. Основная проблема всех композитов – усадка при полимеризации, которая ведет к нарушению краевого прилегания и отрыву пломбы в области дна полости, что, в свою очередь, приводит к воспалению пульпы – пульпиту.
Химические композиты можно было бы использовать для очень небольших пломб, но все дело в том, что у взрослых людей небольших полостей практически не бывает. Маленькая черная точка на поверхности зуба, как верхушка айсберга, скрывает под собой значительный объем кариозных тканей, требующих удаления.
Использование химических композитов в детской стоматологии также нецелесообразно, поскольку на молочных зубах лучше использовать современные стекло-иономерные цементы.
Таким образом, постановка пломбы из химического композита является не более чем первым шагом по пути дальнейшего разрушения и потери зуба. Вот вам и весь «бюджет».
Композиты светового отверждения
Световые композиты уже много лет являются самым распространенным пломбировочным материалом во всем мире. В 1980-е годы появились материалы с различными размерами частиц наполнителя, предназначенные для пломбирования различных групп зубов: макронаполненные (макрофильные), микронаполненные (микрофильные), гибридные. В 90-е годы все компании-производители трудились над разработкой универсальных пломбировочных материалов. С приходом технологий «нано» в распоряжении стоматологов появились поистине универсальные материалы – наногибриды. Сегодня такие композиты имеются в каждом стоматологическом кабинете.
Основная проблема любых композитных материалов – усадка при полимеризации, была решена за счет нанесения материала небольшими порциями и засвечиванием. Как вы понимаете, с композитами химического отверждения это невозможно, поскольку пациенту пришлось бы по несколько минут сидеть с открытым ртом, ожидая, пока застынет очередная порция материала.
Световые композиты сегодня чаще называют не пломбировочными, а реставрационными материалами. С их помощью можно не только ставить пломбы, но и проводить сколь угодно сложные эстетико-функциональные реставрации. Технология отверждения материала светом сделала из врачей-стоматологов, ранее лишь ставивших пломбы, художников и скульпторов. Теперь они могут подбирать материалы по цвету и прозрачности, комбинируя их друг с другом. Могут восстанавливать даже полностью разрушенные зубы, ремонтировать старые пломбы и реставрации, разворачивать криво стоящие зубы, восстанавливать поверхности передних зубов и многое другое.
Несомненно, работа со световыми композитными материалами требует высокой квалификации врача-стоматолога, поэтому, если вас интересует эстетическая реставрация, тщательно выбирайте врача, ориентируясь на примеры его работ и рекомендации знакомых.
Резюмируя, можно привести сравнительную таблицу свойств композитных материалов химического и светового отверждения.
Химический композит
- Можно накладывать только одним слоем – высокая усадка, под пломбой развивается кариес, пломбы выпадают
- Отсутствие адгезии к дентину, сцепление только с эмалью
- Можно только пломбировать полости
- При смешивании двух паст свойства материала ухудшаются под воздействием кислорода
- Можно использовать только один оттенок материала – для передних зубов ХК не применимы
- Адгезив и сам материал были разработаны в 1970-е годы
Световой композит
- Можно накладывать небольшими порциями для уменьшения усадки, срок службы пломбы 10 лет и более
- Наличие специальных праймеров и адгезивов для дентина, сила сцепления с эмалью выше, чем у ХК
- Можно восстанавливать всё – даже отсутствующие части зуба
- Материал в виде одной пасты извлекается из шприца
- Можно комбинировать различные оттенки материала – для любых групп зубов
- Световые материалы прогрессировали в течение последних 30-40 лет
Как уже было сказано выше, химические композиты обладают, пожалуй, единственным преимуществом перед световыми – более низкая цена. Именно поэтому они и стали материалом для бюджета. Более дорогие световые материалы страховые компании не оплачивают. Виват страховой медицине!
Второе «преимущество» химических материалов – более быстрая работа с ними. Действительно, химические пломбы ставятся быстро, материал наносится одной порцией, и его не нужно засвечивать. Это позволяет уложиться в 20 минут, отведенные на прием одного пациента в нашей доблестной бюджетной стоматологии. Но вопрос – сколько простоит такая пломба – месяц? В лучшем случае – полгода-год. А что потом? Обтачивать зуб по новой, а когда нечего будет обтачивать – удаление зуба. Затем протезирование с обточкой соседних зубов, постепенное расшатывание опорных зубов, со временем – удаление оставшихся зубов, и съемные протезы в возрасте 50-60 лет. Но это еще не все. В результате ношения съемных протезов – атрофия альвеолярного гребня, снижение высоты лица и старческая гримаса в 60-70 лет. Вас устраивает такая перспектива? Тогда продолжайте лечиться в бесплатной стоматологии и смело ставьте химические пломбы.
Тем же, кто беспокоится о здоровье и красоте своих зубов и лица, рекомендуем учесть всё, изложенное в этой статье, и, следуя рекомендациям вашего стоматолога, доплатить за качественную световую пломбу. А также не торопиться удалять больные зубы, делая все возможное. чтобы их сохранить и вылечить.
Д.А. Полилов
Москва, 2016 г.
Композитные панели — что это, назначение, характеристики, преимущества и область применения
Содержание:
- Что такое композитный пластик
- Структура и характеристики композита
- Виды композитных панелей
- Типовые размеры
- Преимущества панелей
- Область применения
- Особенности выбора панелей
- Технология монтажа навесных вентилируемых фасадов
- Изготовление кассет
- Преимущества фасадов из композитных панелей
Композит объединяет в своем составе несколько различных материалов в единое целое.
Основу композитных панелей составляет пластичная матрица, армированная различными наполнителями. Внешне они представляют собой прямоугольные многослойные листы.
На строительном рынке представлены композитные материалы, различающиеся по составу наполнителей, количеству слоев, виду отделочных и защитных покрытий.
Структура и характеристики композита
Все слои листов композита соединены между собой по особой технологии, создающей прочную, надежную, устойчивую к расслаиванию конструкцию.
Лицевая поверхность может окрашиваться в разные цвета, быть однотонной или иметь различные рисунки.
Панели представляют собой прямоугольные листы с металлической или полимерной основой и теплоизоляционной прослойкой.
Внутренний слой покрывается антикоррозийным покрытием. На тыльную сторону панелей наносятся знаки в виде стрелок, указывающие направление резки при раскрое листов.
Внешний лицевой слой имеет декоративные и защитные слои из полиэстера или PVDF, защищающие материал от ультрафиолетовых лучей и неблагоприятных погодных факторов. Лицевая поверхность панелей может окрашиваться в разные цвета, иметь рисунок под древесину или кирпич, природный камень или декоративную штукатурку, быть матовой или глянцевой.
Для придания прочности, жесткости и укрепления панелей применяются алюминиевые, стальные или синтетические листы.
Основу композита составляет полимерный наполнитель, отвечающий за технические свойства материала.
Скрепляет многослойную конструкцию слой клея или смолы PVDF.
Рис.1. Структура алюминиевого композита.
Композитные панели могут эксплуатироваться при температурах от -50 до +80°С.
Материал не подвержен коррозии, устойчив к агрессивным природным воздействиям, не поражается плесенью и микроорганизмами. Относится к слабо горючим.
Нормами пожарной безопасности материал допускается к применению в облицовке индивидуальных жилых домов и общественных зданий.
Виды композитных панелей
На строительном рынке композитные панели представлены в нескольких разновидностях, отличающихся по составу и количеству слоев, размерам и цветовой палитре:
Алюминиевые
Состоят из тонких алюминиевых пластин. Характеризуются высокой прочностью и жесткостью при небольшом весе. Алюминиевые панели не боятся ветровых нагрузок. Стоят дороже аналогов. Могут устанавливаться на фасадах высотных зданий и не стабильных несущих ограждающих, рекламных и декоративных конструкциях.
Минеральные
Имеют в своем составе вспененный полиэтилен и антипиреновые соединения, снижающие горючесть материала. Под действием открытого огня материал не плавится. В процессе горения выделяется незначительное количество дыма
Полимерные
Основу материала составляет поликарбонат. Отличаются небольшим весом и доступной стоимостью. Уступают по прочности, жесткости и несущей способности алюминиевым и минеральным аналогам. Применяются для внутренней отделки помещений.
В качестве декоративного и защитного покрытия используются прочные и устойчивые составы:
- Краски PVDF — создают качественный декоративный слой, не выгорающий на солнце, не деформирующийся на морозе и в условиях жаркого климата. Не задерживают грязь и пыль. Не теряют привлекательности до 25 лет.
- Ламинирующие пленки способны имитировать натуральные материалы из дерева, кирпича, камня и металла. Служат от 15 до 20 лет. Отличаются разнообразием рисунков и расцветок, высоким качеством отделки и более дорогой, чем у аналогов ценой.
- Оксидные покрытия образуют на поверхности зеркальное, стойкое к коррозии долговечное покрытие, способное служить без потери качества до 20 лет.
Палитра цветов композитных панелей составляет более 200 позиций по каталогу RAL, из них более 17 — металлических оттенков.
Рис.2. Выбор оттенков композитных панелей.
Типовые размеры
Длина, мм |
Ширина,мм |
Толщина, мм |
1500 |
4000 |
От 2 до 6 |
1220 |
4000 |
|
1500 |
6000 |
|
1220 |
6000 |
Возможны и другие размеры панелей по индивидуальному заказу.
Преимущества панелей
Композитные материалы экологичны и безопасны. Отличаются хорошими теплозащитными качествами. Не выгорают на солнце. Сочетают в себе прочность, жесткость и пластичность.
Композитные плиты обладают высокими эксплуатационными показателями:
- Легкостью. Вес одного квадратного метра листа составляет от трех до восьми килограммов, в зависимости от используемых материалов. Композитные панели легче стальных листов аналогичной жесткости в 3-4 раза, алюминиевых — в 1,5-2 раза.
- Прочностью. Благодаря этим показателям, кассеты изготавливаются больших размеров, что позволяет производить монтажные работы в короткие сроки с минимальными трудозатратами.
- Стойкостью к температурным перепадам и агрессивным воздействиям окружающей среды. Могут эксплуатироваться в условиях жаркого климата и экстремально низких температур.
-
Надежностью и долговечностью.
Отделочные покрытия из композитных панелей могут служить до 50 лет без потери качества и привлекательного внешнего вида.
- Повышенной звукоизоляцией. В сочетании с утепляющими слоями и воздушной прослойкой при монтаже вентилируемых фасадов способны значительно повысить звукоизоляцию помещений и защитить от уличного шума.
Широкая цветовая гамма и отличная гибкость позволяет создавать уникальные конструкции фасадов и внутренние интерьеры зданий.
Вентилируемые фасады можно навешивать на любые стены без предварительной подготовки, что значительно экономит затраты на строительство или ремонт.
К отрицательным свойствам относятся низкая ремонтопригодность. При повреждении композитного листа отремонтировать его практически невозможно.
Риск появления царапин на облицовке повышает требования к монтажу, складированию и транспортировке материала.
Область применения
Одна из самых распространенных сфер использования композитных листов — устройство навесных вентилируемых фасадов.
Листы композита получили широкую популярность при строительстве и реконструкции зданий.
Рис.3. Использование композита при строительстве нестандартных объектов.
Листы из композита применяются при создании различных сооружений и конструкций:
- отделка лоджий и балконов, монтаж навесов и карнизов;
- изготовление вывесок, информационных и выставочных стендов, конструкций наружной рекламы;
- создание стел, указателей, малых архитектурных форм в городском дизайне;
- оформление стен, колонн, потолков, внутри зданий;
- устройство офисных перегородок, специальной мебели;
- обшивка холодильных камер и автомобильных рефрижераторов;
-
строительство автозаправочных станций, киосков, остановочных павильонов и прочих нестандартных объектов.
Композитные листы широко применяются в дизайне зданий. Легко имитируют кирпичи и натуральные камни, зеркала и металл.
Рис. 4. Фасад торгового центра из композитных кассет.
Композитные кассеты не рекомендуется монтировать на детские дошкольные и образовательные учреждения и больницы.
Особенности выбора
Для самостоятельного монтажа композитных конструкций стоит приобретать материал в комплекте с кронштейнами, направляющими профилями, крепежными деталями и другими приспособлениями.
От качества панелей зависит надежность монтажа и срок эксплуатации конструкций.
При выборе композитных панелей нужно руководствоваться следующими рекомендациями:
-
На внутренней стороне панели должна содержаться информация о дате выпуска, номере партии, указываться производственный код и тип панели.
- Любая партия композита комплектуется технической документацией, подтверждающей качество и огнестойкость материала.
- При получении товара проверяйте панели на целостность защитной пленки, отсутствие дефектов, вмятин и царапин. Важно помнить, что панели с высокой степенью горючести не могут использоваться при строительстве жилых домов и общественных помещений.
На защитной пленке указывается направление расположения композитных листов на фасаде, чтобы избежать разнотона при монтаже.
Рис.5. Маркировка материала на защитной пленке.
Технология монтажа навесных вентилируемых фасадов
Навесные вентилируемые фасады пользуются большой популярностью при отделке не только общественных зданий, но и современных частных домов.
Они монтируются по современным технологиям и подходят для стен из кирпича и газобетона, железобетонных панелей и дерева.
Конструкция вентфасада включает в себя:
- облицовку из композитных кассет;
- стальную подсистему;
- утепляющие, пароизолирующие и ветрозащитные материалы.
Между утеплителем и облицовочным слоем устраивается воздушный зазор.
Благодаря воздушной прослойке, работающей по принципу вытяжной трубы, конденсирующая под фасадной облицовкой влага вытягивается с восходящим воздушным потоком в атмосферу.
Кроме того, прослойка из воздуха является дополнительным теплоизолятором. Она сглаживает термические деформации, возникающие при температурных перепадах, тем самым предотвращает преждевременное разрушение несущих и ограждающих конструкций.
ия можно использовать стекло матовое или более темных тонов. В продаже имеется поликарбонат в широкой гамме цветов: опал, бронзовый, бирюзовый, голубой, оранжевый.
Возможно вас заинтересует:
Композитные панели | Размеры | Стоиомость листа |
ALTEC зеркало золотое (RAL 0007) al 0.![]() |
1500х4000х3 |
10352 руб |
ALTEC графит металлик (RAL 0009) al 0.21 | 1500х4000х3 | 4500 руб |
ALTEC шампань металлик (RAL 0004) al 0.21 | 1500х4000х3 | 4500 руб |
ALTEC бронза металлик (RAL 0002) al 0.21 | 1500х4000х3 | 4500 руб |
ALTEC золото металлик (RAL 0003) al 0.21 | 1500х4000х3 | 4500 руб |
ALTEC зеркало золотое (RAL 0007) al 0.3 | 1220х4000х3 | 9760 руб |
ALTEC зеркало серебрянное (RAL 0007) al 0.3 | 1220х4000х3 | 9760 руб |
ALTEC графит металлик (RAL 0009) al 0.![]() |
1220х4000х3 | 5002 руб |
ALTEC шампань металлик (RAL 0004) al 0.3 | 1220х4000х3 | 5002 руб |
ALTEC бронза металлик (RAL 0002) al 0.3 | 1220х4000х3 | 5002 руб |
Весь ассортимент >>>
Устройство навесных вентилируемых фасадов производится в определенной последовательности:
- Выполняется вертикальная разметка фасада при помощи лазерной рулетки, мерных реек и рулетки. Отмеченные точки соединяются горизонтальными и вертикальными линиями при помощи красящего малярного шнура.
-
В месте крепления кронштейнов высверливаются отверстия и вставляются анкерные дюбели.
- Монтируются кронштейны, состоящие из неподвижного несущего элемента и регулируемой подвижной вставки, которая закрепляется при помощи отвесов на нужном уровне. Шаг кронштейнов должен составлять 40-55 сантиметров по вертикали. Интервал направляющих по горизонтали нужно устанавливать исходя из размеров композитных кассет.
- На кронштейны каркаса устанавливаются плиты из минеральной ваты, пеноплекса или пенополистирола. В месте, где изоляция навешивается на выдвижку кронштейна, в плите делаются надрезы крест-накрест. Утеплитель в центре и по углам закрепляется на стене клеем.
- Поверх утеплителя укладывается паро- и ветрозащитная фасадная мембрана с нахлестом между полотнами в 10-15 сантиметров. Все слои крепятся к стене тарельчатыми дюбелями.
-
Для монтажа композитных панелей к кронштейнам на саморезы или заклепки крепятся вертикальные направляющие П-образной формы. В полость профилей заводятся распорные пластины, которые служат зацепом для фасадных кассет.
Важно обеспечить надежное и жесткое закрепление всех элементов каркаса строго в одной плоскости.
- Навешивание кассет нужно начинать с нижней части обрешетки, выравнивая панели строго по горизонтали и фиксируя в верхних углах при помощи саморезов. Следующие листы крепятся аналогично, с соблюдением одинаковых зазоров в 10-12 миллиметров.
Для изоляции металла от стены под каждым кронштейном устанавливаются терморазрывные прокладки из изолирующего материала.
Рис. 6. Монтажный узел навесного вентилируемого фасада.
Изготовление кассет
Для устройства фасадов из композита, предварительно, в соответствии с проектными чертежами, изготавливаются кассеты.
Для этого с четырех сторон композитного листа формируются углы с использованием фрезерных и гибочных станков.
Рис. 7. Схема развертки заготовки и готовая композитная кассета.
При формировании углов, на фрезерном станке вырезается слой композита в виде углов 90° или 135° или прямоугольника шириной 14 мм, оставляя в точке изгиба слой полиэтилена толщиной от 0,5 до 1,5 мм.
Рис. 8. Схема вариантов гибки композитных листов.
Преимущества фасадов из композитных панелей
Вентилируемые навесные фасады из композитных кассет пользуются большой популярностью из-за значительных преимуществ перед другими вариантами отделки:
- не требуют предварительного выравнивания стен;
- обеспечивают защиту несущих ограждающих конструкций от холода и жары, прямых солнечных лучей, дождя и ветра;
- способны утеплять и повышать шумоизоляцию зданий;
-
легкий вес навесной системы не требует дополнительного укрепления несущих конструкций.
Вентилируемые фасады исключают грязные процессы в отделке и позволяют монтировать конструкции в сжатые сроки независимости от времени года и погоды.
Рис. 9. Монтаж кассет из листов композита.
Строго соблюдая последовательность и технологию производства работ, можно создать надежное и красивое покрытие, придать фасаду неповторимый, яркий и современный внешний вид, повысить звукоизоляцию, добиться ощутимого энергосбережения здания.
Композитные клеи | Конструкционные клеи для композитов
Клеи для структурного склеивания для композитной промышленности
В производстве композитов часто используются возможности склеивания, выходящие за рамки традиционных методов склеивания. Chemique предлагает широкий ассортимент композитных клеев, способных удовлетворить даже самые высокие требования к конструкционным клеям.
Строгие требования композитной промышленности требуют наличия клеев, предназначенных для склеивания различных технических подложек. Композитные клеи, используемые при изготовлении самых разных продуктов, позволяют использовать множество комбинаций материалов. Композитные материалы, подходящие для склеивания с использованием этих клеев, включают:
- Углеродные волокна — используются в широком спектре продуктов благодаря своей прочности, жесткости и универсальности. Из-за требований к углеродным волокнам часто требуется ремонт, и выбор правильного соединения имеет решающее значение.
- Пластмассы — склеивание пластмасс во многом зависит от того, для чего они используются.При выборе наилучшего метода склеивания также необходимо учитывать другие факторы, такие как термостойкость или огнестойкость.
- Металлы — при соединении металлов с металлами или с другими материалами, такими как дерево или пластик, может быть сложно определить лучший клей. Chemique предлагает широкий выбор клеев практически для любого применения, в том числе для использования с нержавеющей сталью.
- Timbers — будь то склеивание древесины с бетоном для строительных целей или склеивание древесины для других целей, ассортимент композитов Chemique гарантирует надежное и долговечное решение.
- Бетон — Связующие и клеи для бетона Chemique обещают высокопрочное решение для склеивания бетона практически с любой другой поверхностью.
Если вы не уверены, какой метод лучше всего подойдет для вашего приложения, свяжитесь с нами, и мы укажем вам верное направление.
Мы предлагаем клеевые решения для рынков композитных материалов, в том числе:
- Конструкционные композиты
- Сотовые панели
- Панели для защиты от дождя
- Возобновляемая энергия
- Специальные транспортные панели
- Структурные изолированные панели
Клей для композитов | Конструкционные клеи для композитов
Клеи для структурного склеивания для композитной промышленности
В производстве композитов часто используются возможности склеивания, выходящие за рамки традиционных методов склеивания. Chemique предлагает широкий ассортимент композитных клеев, способных удовлетворить даже самые высокие требования к конструкционным клеям.
Строгие требования композитной промышленности требуют наличия клеев, предназначенных для склеивания различных технических подложек. Композитные клеи, используемые при изготовлении самых разных продуктов, позволяют использовать множество комбинаций материалов.
Композитные материалы, подходящие для склеивания с использованием этих клеев, включают:
- Углеродные волокна — используются в широком спектре продуктов благодаря своей прочности, жесткости и универсальности.Из-за требований к углеродным волокнам часто требуется ремонт, и выбор правильного соединения имеет решающее значение.
- Пластмассы — склеивание пластмасс во многом зависит от того, для чего они используются. При выборе наилучшего метода склеивания также необходимо учитывать другие факторы, такие как термостойкость или огнестойкость.
- Металлы — при соединении металлов с металлами или с другими материалами, такими как дерево или пластик, может быть сложно определить лучший клей.Chemique предлагает широкий выбор клеев практически для любого применения, в том числе для использования с нержавеющей сталью.
- Timbers — будь то склеивание древесины с бетоном для строительных целей или склеивание древесины для других целей, ассортимент композитов Chemique гарантирует надежное и долговечное решение.
- Бетон — Связующие и клеи для бетона Chemique обещают высокопрочное решение для склеивания бетона практически с любой другой поверхностью.
Композитные растворы Chemique также могут использоваться в качестве клея для ДПК. Они идеально подходят для использования с сэндвич-панелями из ДПК или с панелями из ДПК в целом.
Если вы не уверены, какой из наших композитных клеевых растворов лучше всего подойдет для вашего применения, свяжитесь с нами, и мы укажем вам правильное направление.
Мы предлагаем клеевые решения для рынков композитных материалов, в том числе:
- Конструкционные композиты
- Сотовые панели
- Панели для защиты от дождя
- Возобновляемая энергия
- Специальные транспортные панели
- Структурные изолированные панели
Композитные клеи | Конструкционные клеи для композитов
Клеи для структурного склеивания для композитной промышленности
В производстве композитов часто используются возможности склеивания, выходящие за рамки традиционных методов склеивания.Chemique предлагает широкий ассортимент композитных клеев, способных удовлетворить даже самые высокие требования к конструкционным клеям.
Строгие требования композитной промышленности требуют наличия клеев, предназначенных для склеивания различных технических подложек. Композитные клеи, используемые при изготовлении самых разных продуктов, позволяют использовать множество комбинаций материалов. Композитные материалы, подходящие для склеивания с использованием этих клеев, включают:
- Углеродные волокна — используются в широком спектре продуктов благодаря своей прочности, жесткости и универсальности.Из-за требований к углеродным волокнам часто требуется ремонт, и выбор правильного соединения имеет решающее значение.
- Пластмассы — склеивание пластмасс во многом зависит от того, для чего они используются. При выборе наилучшего метода склеивания также необходимо учитывать другие факторы, такие как термостойкость или огнестойкость.
- Металлы — при соединении металлов с металлами или с другими материалами, такими как дерево или пластик, может быть сложно определить лучший клей.Chemique предлагает широкий выбор клеев практически для любого применения, в том числе для нержавеющей стали.
- Timbers — будь то склеивание древесины с бетоном для строительных целей или склеивание древесины для других целей, ассортимент композитов Chemique гарантирует надежное и долговечное решение.
- Бетон — Связующие и клеи для бетона Chemique обещают высокопрочное решение для склеивания бетона практически с любой другой поверхностью.
Если вы не уверены, какой из наших композитных клеевых растворов лучше всего подойдет для вашего применения, свяжитесь с нами, и мы укажем вам верное направление.
Мы предлагаем клеевые решения для рынков композитных материалов, которые мы обслуживаем, в том числе:
- Конструкционные композиты
- Сотовые панели
- Панели для защиты от дождя
- Возобновляемая энергия
- Специальные транспортные панели
- Структурные изолированные панели
Все промышленные клеи для композитов
Все промышленные клеи для композитов | Композитное соединениеКлеи для композитов — вся промышленность
- Дом
- Клеи для композитов — вся промышленность
Permabond предлагает широкий спектр различных клеевых технологий для склеивания композитов.Если вам требуется быстрое отверждение за секунды или несколько часов для сборки деталей, Permabond может помочь вам найти подходящий композит для композитных материалов.
Основные характеристики клея для композитовПользователи клеев Permabond получают преимущества от функций, недоступных для механических креплений:
-Экономия затрат
-Уменьшение веса компонентов
-Улучшенное распределение напряжений
-Улучшенный внешний вид
-Ускоренный производственный процесс
-Устранение предварительного сверления
-Предотвращение утечек
-Предотвращение коррозии
-Широкий выбор материалов подложки
-Уменьшение шума и вибрации абсорбция
Отрасли, использующие клеи Permabond для склеивания композитов:
-Аэрокосмическая промышленность — интерьер кабины
-Автомобиль — легкие спортивные автомобили из углеродного волокна и запчасти для вторичного рынка
-Спортивное оборудование
-Медицинское протезирование
-Баки и чаны
-Морская техника
-Лопасти ветряной турбины
-Переоборудование транспортных средств, караваны и кемперы-автовозы
, фасады зданий, вывески и интерьер
Для получения дополнительной информации, включая таблицу выбора, загрузите брошюру по продукту.За персональной помощью в выборе лучшего продукта для вашего применения обращайтесь в Permabond.
Свяжитесь с нами для получения дополнительной информации
Брошюра о продукте (PDF)© 2016 ООО «Пермабонд». — Permabond является сертифицированной компанией ISO QMS — Щелкните здесь, чтобы получить pdf-копию нашего сертификата ISO QMS. Цифровые решения, предоставленные Rebel Interactive Group
.Клейкое покрытие | Обзор промышленных покрытий | Технология нанесения покрытий и дозирования
Адгезия — это состояние, в котором две поверхности были соединены химической или физической силой или их комбинацией посредством адгезивной среды.В этом разделе объясняются механизмы адгезии, а также типы и функции клеев.
Ваш путеводитель по технологии нанесения покрытий и дозирования
Понимание основ процессов нанесения покрытий и типов используемого оборудования помогает пользователям повысить качество и эффективность. Ознакомьтесь с этим подробным руководством, чтобы получить обзор процессов нанесения покрытия и дозирования, которые стали незаменимыми в современной обрабатывающей промышленности.
Скачать
Механизмы адгезии можно разделить на следующие три основные подкатегории.
Две поверхности скрепляются клеем, который затвердевает после заполнения отверстий и неровностей на поверхностях. Это называется «эффектом якоря» (или «эффектом застежки»).
Физическое взаимодействие Связывание — это принцип адгезии, основанный на силе Ван-дер-Ваальса (межмолекулярной силе), которая является силой притяжения между всеми молекулами.Эта сила также называется «вторичной силой сцепления».
Химическое взаимодействие между материалом мишени и клеем вызывает химическую связь между атомами, что приводит к относительно прочной адгезии. Это также называется «силой первичного связывания» и включает ковалентную и водородную связь.
- Материал мишени
- Клей
- Химическая связь
Приведенные выше классификации приведены только для примера.Есть много способов классифицировать типы адгезии, и некоторые из них могут отличаться от описанных выше.
Адгезия путем нанесения покрытия — это процесс склеивания объектов с помощью клея, который смачивает цель и затем затвердевает. Существуют различные типы клеев, в том числе жидкие и твердые. Твердые клеи должны расплавиться под действием тепла, и предметы склеиваются, когда клей затвердевает. Клеи можно разделить на следующие три основных типа.
- Однокомпонентные и двухкомпонентные клеи (например, уретановые или эпоксидные)
- Классифицируемый как жидкий клей, однокомпонентный клей отверждается под действием влаги воздуха или тепла.Двухкомпонентные клеи отверждаются при смешивании двух типов жидкости — смолы и отвердителя. По сравнению с клеями-расплавами двухкомпонентные клеи обычно обладают более высокой прочностью сцепления.
- Клеи-расплавы
- Эти твердые клеи (в виде блоков или гранул) перед использованием необходимо расплавить при нагревании. Этот тип отличается более коротким временем отверждения и меньшим количеством условий. Обычные материалы включают полиэфир, олефин, каучук, EVA и PA.
- Клеи-расплавы реактивные
- Реактивные клеи-расплавы — это клеи с термостойкими свойствами.Клей затвердевает под действием влажности окружающего воздуха. Эти клеи характеризуются низкими температурами плавления и покрытия и используются для различных типов мишеней.
Приведенные выше классификации приведены только для примера. Есть много способов классифицировать типы адгезии, и некоторые из них могут отличаться от описанных выше.
В то время как основная цель клеев состоит в том, чтобы связывать объекты вместе, существуют «функциональные клеи», которые предлагают различные свойства сцепления, такие как различные процессы отверждения и скорости сцепления.Также могут быть достигнуты дополнительные функции материала, такие как удельная проводимость, долговечность, прозрачность или эластичность.
Тип | Функция |
---|---|
Клей мгновенного отверждения | Клеи, которые быстро затвердевают (за 5 секунд или меньше). |
Клей контактного отверждения | Одна поверхность покрыта агентом A, а другая — агентом B.Отверждение начинается, когда агент A вступает в контакт с агентом B. Это делает ненужным предварительное смешивание агентов. |
УФ-отверждаемый клей | Эти клеи используются для склеивания светопропускающих материалов. Клей мгновенно затвердевает при воздействии УФ (ультрафиолетового) света. |
Клей анаэробного отверждения | Этот клей проникает через зазоры, например, вокруг винтов, и затвердевает в отсутствие воздуха (кислорода). |
Имущество | Функция |
---|---|
Прозрачность | Обеспечивает прозрачность с показателем преломления, эквивалентным показателю преломления стеклянных линз. |
Электропроводность | Обладает способностью поглощать электромагнитные волны для предотвращения радиопомех. |
Термостойкость | Обладает высокой термостойкостью (например,g., оксид алюминия, диоксид циркония или другие неорганические вещества). |
Эластичность | Обладает чрезвычайно высокой степенью эластичности. Используется для склеивания материалов с разными коэффициентами теплового расширения или для склеивания, требующего большей прочности. |
Жесткость | Обеспечивает высокую жесткость соединяемого участка за счет использования как «точечного» склеивания с резистивной сваркой, так и «поверхностного» склеивания клеями (сварка). |
В дополнение к вышеперечисленному, существуют также клеи, которые обладают различными другими свойствами и функциями, такими как герметизация, изоляция, огнестойкость, теплопроводность и пенообразование.
В то время как клеи и оборудование для нанесения покрытий стали более разнообразными и сложными, применение адгезивного склеивания также расширилось в более широком диапазоне областей. В частности, для конструкционных клеев растет спрос на точные адгезивные покрытия, такие как небольшое количество клеевого покрытия, которое удовлетворяет более тонкие требования к дизайну для дисплеев (ЖК-дисплеи и органические электролюминесцентные лампы) и интеллектуальных устройств (смартфоны, планшеты), а также для более прочного соединения различных материалы в поисках более легкого веса и большей жесткости в автомобильной и авиакосмической промышленности.
В общем, структурный клей — это клей, предназначенный для высокопрочного склеивания. Использование покрытия с такими адгезионными свойствами обеспечивает склеивание «площадей», в результате чего получается легкое и прочное соединение. Комбинируя соединение областей с «точечным» соединением, таким как точечная сварка, болты или заклепки, можно создать соединение с еще большей жесткостью. Типичным примером является «сварка», при которой используется точечная сварка в процессе сборки кузова автомобиля.
Конструкционные клеи широко используются в аэрокосмической промышленности на протяжении более полувека, в том числе для самолетов, вертолетов, сверхзвуковых реактивных самолетов, космических кораблей Apollo и космических челноков.
Сегодня потребность в склеивании различных материалов растет из-за все более широкого использования композитных материалов (мульти-материалов) в кузовах автомобилей и других продуктах для снижения нагрузки на окружающую среду и повышения производительности. В результате конструкционные легкие и высокопрочные клеи привлекают внимание не только в современных передовых областях, таких как освоение космоса, но и в областях массового производства, таких как автомобильная промышленность.
- Применение конструкционных клеев для склеивания различных материалов
Автомобильные Требование Склеивание композитных материалов для снижения веса и увеличения жесткости кузовов автомобилей Материал Алюминиевое шасси + внутренняя часть из углепластика Метод склеивания Конструкционный клей на основе уретана + небольшое количество болтов Крепление различных магнитов двигателя (например, серводвигателей FA) Требование Склеивание различных материалов с высокой термостойкостью и высокой прочностью Материал Nd (неодимовый) магнит + многослойный сердечник Метод склеивания Клей SGA (реактивный акриловый клей) Панель солнечной батареи (для искусственных спутников) Требование Устойчивость к тепловому циклу (от -150 ° C до + 200 ° C), устойчивость к излучению, прозрачность и т. Д. Материал Элемент солнечной батареи + защитное стекло Метод склеивания Силиконовый клей
Дом
Клеевые стержни Tecbond Adhesives — Power Adhesives
- Решения
- Tec
- Tecbond
- Spraytec
- Foundrytec
- Casttec
- Узел
- Vactac
- Groovtec
- Скимендер
- Hobbytec
- Overtec
- TackFix
- Газ-тек
- Дентменда
- Cabletac
- Peeltec
- Клеи для сыпучих материалов Tecbond
- Клей для насыпных материалов Beardow Adams
- Рынки
- Клеи для упаковки
- Клеи для сборки продукта
- Клеи для деревообработки
- Клеи для сердечников литейного производства
- Клеи для декоративно-прикладного искусства
- Клей для точек продаж
- Полипропиленовые адгезивы
- Клеи для полов
- Композитный клей для вакуумной инфузии
- Клеи для пены и матрасов
- Tec Поддержка
- Оборудование
- B-TEC 308
- B-TEC 808
- ГАЗ-ТЭК 600
- ТЭК 305-12
- ТЭК 806-12
- ТЭК 805-15
- ТЭК 810-12
- ТЭК 810-15
- ТЭК 820-12
- ТЭК 820-15
- ТЕС 3150
- ТЭК 3400
- ТЭК 6100
- ТЭК 6300
- ТЭК 7100
- ТЭК 7300
- Оборудование
- Около
- Контакты
- Работай с нами
- Решения
- Tec
- Tecbond
- Spraytec
- Foundrytec
- Casttec
- Узел
- Vactac
- Groovtec
- Скимендер
- Hobbytec
- Overtec
- TackFix
- Газ-тек
- Дентменда
- Cabletac
- Peeltec
- Клеи для сыпучих материалов Tecbond
- Клей для насыпных материалов Beardow Adams
- Рынки
- Клеи для упаковки
- Клеи для сборки продукта
- Клеи для деревообработки
- Клеи для сердечников литейного производства
- Клеи для декоративно-прикладного искусства
- Клей для точек продаж
- Полипропиленовые адгезивы
- Клеи для полов
- Композитный клей для вакуумной инфузии
- Клеи для пены и матрасов
- Tec Поддержка
- Оборудование
- Оборудование